A hydraulic press system is a complex assembly designed to apply controlled pressure using hydraulic force. It typically includes a mainframe, a power system, and hydraulic control instruments. The system operates by using hydraulic cylinders to generate force, which is then transferred to the press head or platen. This force can be precisely controlled to perform various industrial tasks such as molding, forging, and pressing. The system's efficiency and precision make it indispensable in industries requiring high-pressure applications.
Key Points Explained:
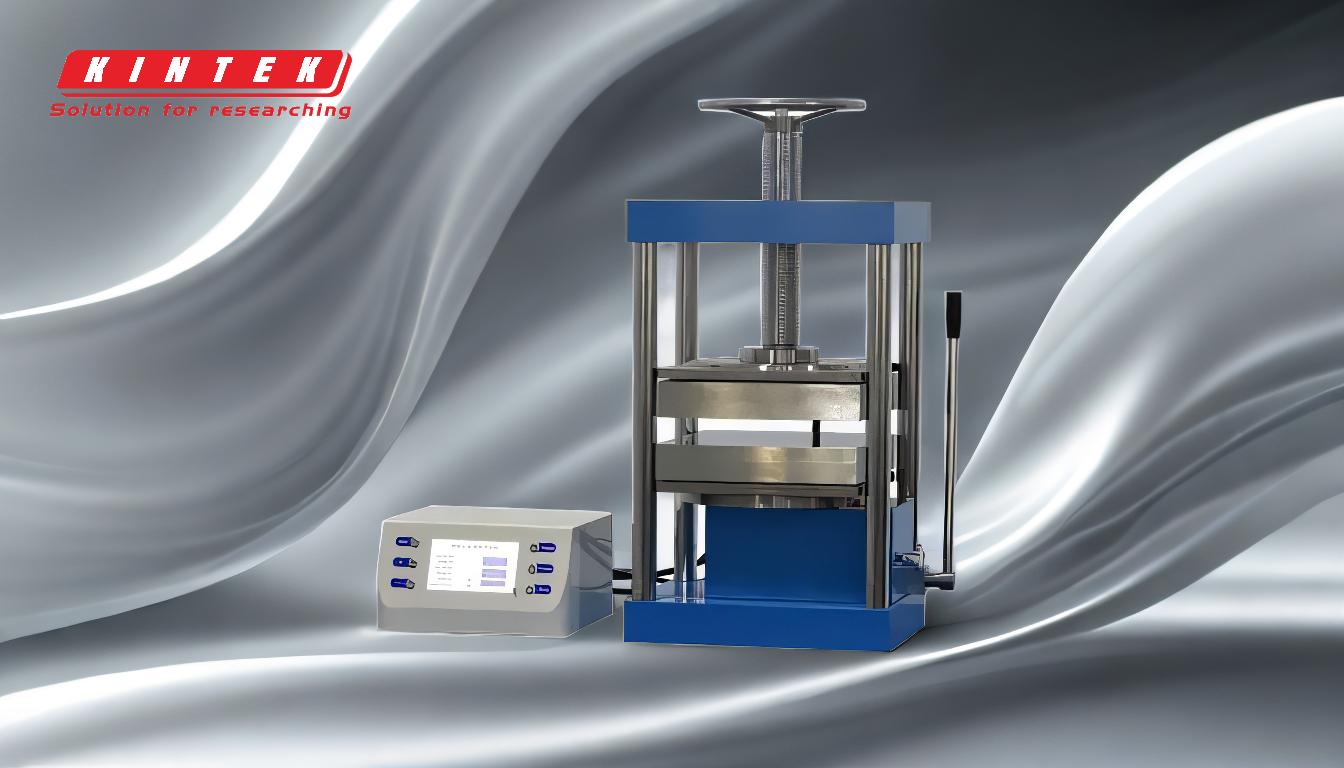
-
Main Components of a Hydraulic Press System:
- Mainframe Machine: This is the structural backbone of the hydraulic press, providing stability and support. It typically includes columns, frames, and solid steel sheets that connect the base to the head of the press.
- Power System: This system generates the necessary hydraulic force. It usually consists of hydraulic cylinders and pumps that convert mechanical energy into hydraulic energy.
- Hydraulic Control Instrument: This component regulates the flow and pressure of the hydraulic fluid, ensuring precise control over the press's operations.
-
Hydraulic Cylinders and Platens:
- Hydraulic Cylinders: These are the primary actuators in a hydraulic press, responsible for generating the force required for pressing. They move up and down, driven by hydraulic fluid.
- Platens: These are the flat surfaces that come into direct contact with the material being pressed. They are typically made of steel, ground, and chromium-plated to prevent sticking and corrosion. Platens often have holes drilled through them for the passage of hot oil or steam, which is crucial in processes like hydraulic hot press machine operations.
-
Operation and Control:
- Pressure Application: The hydraulic press applies pressure uniformly across the material, ensuring consistent results. The bottom bed moves up and down, while the top head remains stationary, allowing for precise control over the pressing process.
- Control Systems: Modern hydraulic presses are equipped with advanced control systems that allow for precise regulation of pressure, temperature, and timing. This is particularly important in applications requiring high precision, such as in the manufacturing of composite materials.
-
Applications and Advantages:
- Versatility: Hydraulic presses are used in a wide range of industries, including automotive, aerospace, and manufacturing. They are capable of performing tasks such as molding, forging, and pressing with high precision.
- Efficiency: The ability to generate high force with relatively low energy input makes hydraulic presses highly efficient. They are also capable of operating at high speeds, further enhancing their productivity.
- Durability: The robust construction of hydraulic presses ensures long-term durability and reliability, even under heavy use.
-
Maintenance and Safety:
- Regular Maintenance: To ensure optimal performance, hydraulic presses require regular maintenance, including checking hydraulic fluid levels, inspecting seals and hoses, and ensuring that all moving parts are properly lubricated.
- Safety Features: Modern hydraulic presses are equipped with various safety features, such as emergency stop buttons, safety guards, and pressure relief valves, to protect operators and prevent accidents.
In summary, the hydraulic press system is a sophisticated and versatile tool that plays a critical role in many industrial processes. Its ability to generate and control high-pressure forces with precision makes it an invaluable asset in manufacturing and material processing. Understanding its components, operation, and maintenance is essential for maximizing its efficiency and ensuring safe operation.
Summary Table:
Component | Description |
---|---|
Mainframe Machine | Structural backbone providing stability and support. |
Power System | Generates hydraulic force using cylinders and pumps. |
Hydraulic Control Instrument | Regulates fluid flow and pressure for precise control. |
Hydraulic Cylinders | Actuators that generate force for pressing. |
Platens | Flat surfaces for material pressing, often heated for specific applications. |
Control Systems | Advanced systems for precise pressure, temperature, and timing regulation. |
Applications | Molding, forging, and pressing in industries like automotive and aerospace. |
Advantages | High efficiency, durability, and versatility. |
Maintenance | Regular checks on fluid levels, seals, hoses, and lubrication. |
Safety Features | Emergency stops, safety guards, and pressure relief valves. |
Ready to enhance your industrial processes with a hydraulic press? Contact us today for expert guidance!