Thin film deposition is a critical technology used in various industries, including electronics, optics, and energy, to create thin layers of material on a substrate. The process involves several phases, such as adsorption, surface diffusion, and nucleation, which are influenced by material properties, substrate characteristics, and deposition methods. Thin film deposition techniques are broadly categorized into chemical methods, like Chemical Vapor Deposition (CVD), and physical methods, such as Physical Vapor Deposition (PVD). Each method has unique advantages and is chosen based on the material properties and application requirements. Advanced technologies, including atomic resolution imaging, have significantly enhanced the precision and capabilities of thin film deposition. The process typically involves steps like selecting a pure material source, transporting it to the substrate, depositing it, and optionally treating the film to achieve desired properties.
Key Points Explained:
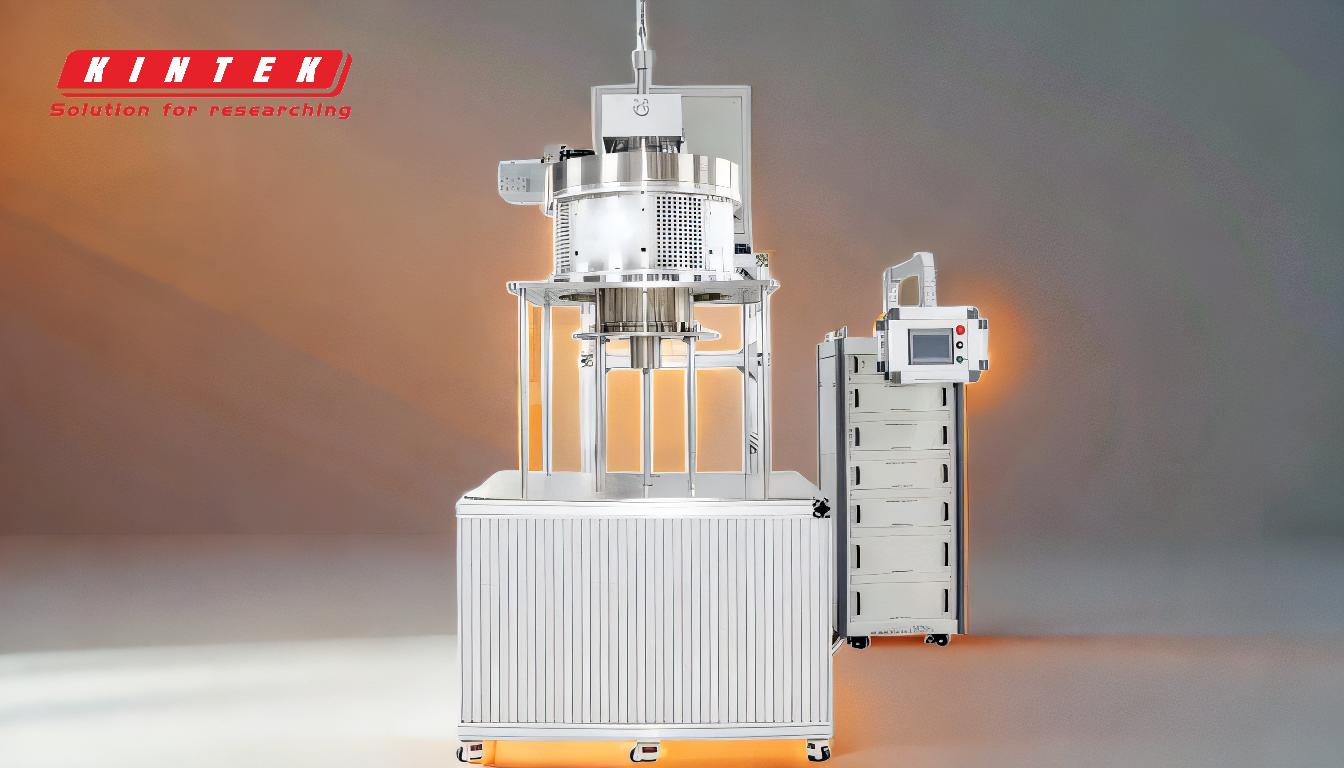
-
Phases of Thin Film Deposition:
- Adsorption: The initial phase where material atoms or molecules adhere to the substrate surface.
- Surface Diffusion: The movement of adsorbed atoms or molecules across the substrate surface.
- Nucleation: The formation of small clusters or nuclei on the substrate, which grow into a continuous thin film.
- These phases are influenced by factors such as material properties, substrate conditions, and deposition parameters.
-
Categories of Thin Film Deposition:
-
Chemical Methods: These involve chemical reactions at the substrate surface to deposit materials. Examples include:
- Chemical Vapor Deposition (CVD): A process where gaseous reactants form a solid film on the substrate through chemical reactions.
-
Physical Methods: These rely on mechanical or thermal processes to create material sources for deposition. Examples include:
- Physical Vapor Deposition (PVD): A technique where a material is vaporized and then condensed onto the substrate.
-
Chemical Methods: These involve chemical reactions at the substrate surface to deposit materials. Examples include:
-
Common Materials Used in Thin Film Deposition:
- Metals: Often used for conductive layers in electronics.
- Oxides: Such as copper oxide (CuO) and indium tin oxide (ITO), used in applications like solar cells and transparent conductive films.
- Compounds: Like copper indium gallium diselenide (CIGS), which is popular in photovoltaic applications due to its high efficiency.
-
Steps in Thin Film Deposition:
- Material Selection: Choosing a pure material source (target) suitable for the desired film properties.
- Transportation: Moving the target material to the substrate, often through a medium like a fluid or vacuum.
- Deposition: Forming a thin film on the substrate by depositing the target material.
- Post-Deposition Treatment: Optional steps like annealing or heat treatment to enhance film properties.
- Analysis: Evaluating the film's properties and modifying the deposition process if necessary to achieve the desired characteristics.
-
Advancements in Thin Film Deposition:
- The development of advanced technologies, such as atomic resolution surface imaging, has significantly improved the precision and control of thin film deposition processes.
- Techniques like sputtering-based methods continue to evolve, enabling new applications and improved performance in various industries.
-
Applications of Thin Film Deposition:
- Electronics: Used in the fabrication of semiconductors, sensors, and displays.
- Optics: Applied in anti-reflective coatings, mirrors, and optical filters.
- Energy: Utilized in solar cells, batteries, and fuel cells to enhance efficiency and performance.
By understanding these key aspects, one can appreciate the complexity and importance of thin film deposition technology in modern manufacturing and research. The choice of method and materials depends on the specific application, and ongoing advancements continue to expand the possibilities for this versatile technology.
Summary Table:
Aspect | Details |
---|---|
Phases | Adsorption, Surface Diffusion, Nucleation |
Methods | Chemical (CVD), Physical (PVD) |
Common Materials | Metals, Oxides (CuO, ITO), Compounds (CIGS) |
Steps | Material Selection, Transportation, Deposition, Post-Treatment, Analysis |
Advancements | Atomic resolution imaging, sputtering-based methods |
Applications | Electronics, Optics, Energy |
Discover how thin film deposition can revolutionize your projects—contact our experts today!