A tube furnace is a highly versatile piece of equipment used in various industrial and laboratory applications, primarily for heating materials to high temperatures under controlled conditions. The temperature of a tube furnace can vary significantly depending on its design, intended use, and the materials being processed. Generally, tube furnaces can achieve temperatures ranging from a few hundred degrees Celsius to over 1800°C, with some specialized models capable of reaching even higher temperatures. The ability to control the atmosphere within the furnace and the precise temperature regulation make tube furnaces ideal for processes requiring high thermal stability and uniformity. Factors such as the furnace's heating elements, insulation, and control systems play a critical role in determining its maximum temperature and performance.
Key Points Explained:
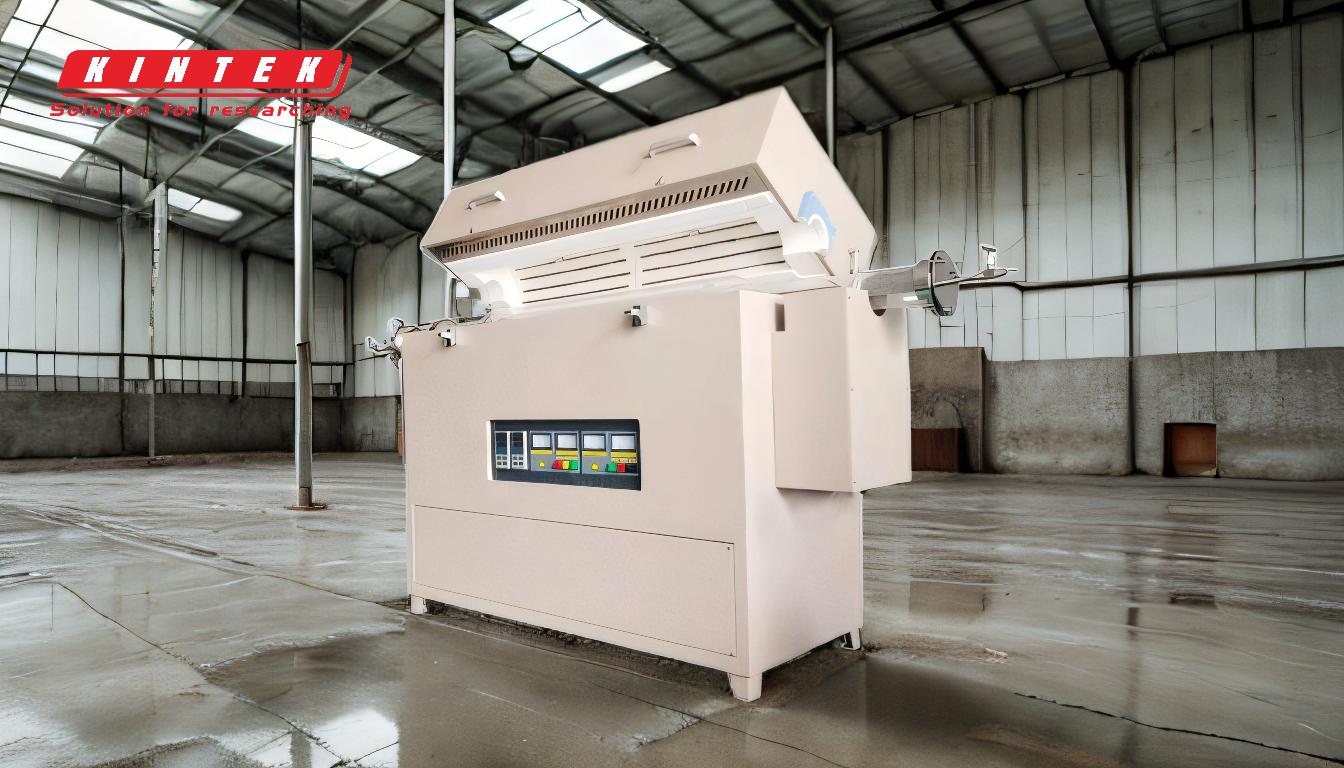
-
Temperature Range of a Tube Furnace:
- Tube furnaces are designed to operate across a wide temperature spectrum, typically ranging from 200°C to 1800°C, depending on the model and application. Some advanced models can exceed these limits, reaching temperatures up to 3000°C.
- The temperature range is influenced by the type of heating elements used (e.g., resistance wires, silicon carbide rods, or molybdenum disilicide) and the furnace's insulation materials.
- For example, furnaces with silicon carbide heating elements are suitable for high-temperature applications, while those with resistance wires are better for lower-temperature processes.
-
Factors Affecting Temperature Control:
- Heating Elements: The choice of heating elements determines the maximum achievable temperature. For instance, molybdenum disilicide elements are ideal for ultra-high temperatures, while Kanthal wires are better suited for moderate ranges.
- Insulation: High-quality insulation materials, such as ceramic fiber or refractory bricks, help maintain thermal efficiency and prevent heat loss, ensuring consistent temperature control.
- Control Systems: Modern tube furnaces use advanced control systems, including programmable logic controllers (PLCs) and thermocouples, to maintain precise temperature regulation. These systems allow for both heating and cooling processes to be automated and monitored in real-time.
-
Temperature Zones and Uniformity:
- Tube furnaces often feature multiple temperature zones, each with its own heating elements and control mechanisms. This design ensures uniform heat distribution across the length of the furnace tube, which is critical for processes requiring consistent thermal conditions.
- The uniformity of temperature is essential for applications like material synthesis, where even slight variations can affect the quality of the final product.
-
Influence of Tube Material and Dimensions:
- The material of the furnace tube (e.g., quartz, alumina, or silicon carbide) affects its thermal and mechanical properties, which in turn influence the furnace's performance and temperature capabilities.
- Quartz tubes are suitable for lower temperatures and corrosive environments.
- Alumina tubes can withstand higher temperatures and are chemically inert.
- Silicon carbide tubes are ideal for ultra-high-temperature applications.
- The length and diameter of the tube also play a role in heat transfer and residence time. Longer tubes improve reaction efficiency, while shorter tubes enhance gas-solid mixing.
- The material of the furnace tube (e.g., quartz, alumina, or silicon carbide) affects its thermal and mechanical properties, which in turn influence the furnace's performance and temperature capabilities.
-
Atmosphere Control and Its Impact on Temperature:
- Tube furnaces can operate in various atmospheres, including inert gases (e.g., argon or nitrogen), reducing gases (e.g., hydrogen), or vacuum conditions. The ability to control the atmosphere allows for higher heating temperatures and prevents oxidation or contamination of the materials being processed.
- For example, in a reducing atmosphere, higher temperatures can be achieved without damaging sensitive materials.
-
Applications and Temperature Requirements:
- The required temperature depends on the specific application. For instance:
- Material Synthesis: Often requires temperatures between 800°C and 1600°C.
- Annealing: Typically performed at 500°C to 1200°C.
- Sintering: May require temperatures up to 1800°C or higher.
- Each application has unique thermal requirements, and the tube furnace must be selected accordingly.
- The required temperature depends on the specific application. For instance:
-
Maintenance and Long-Term Performance:
- Over time, factors such as soiling, deposits, and wear can affect the furnace's temperature control. Regular maintenance, including cleaning and replacing worn components, is essential to ensure consistent performance.
- For example, in dental furnaces, deposits from ceramic or alloy materials can alter temperature profiles, necessitating periodic calibration.
In conclusion, the temperature of a tube furnace is highly customizable and depends on several factors, including its design, heating elements, insulation, and control systems. Understanding these factors is crucial for selecting the right furnace for specific applications and ensuring optimal performance.
Summary Table:
Factor | Details |
---|---|
Temperature Range | 200°C to 1800°C (up to 3000°C for advanced models) |
Heating Elements | Resistance wires, silicon carbide rods, molybdenum disilicide |
Insulation | Ceramic fiber, refractory bricks |
Control Systems | PLCs, thermocouples for precise regulation |
Tube Materials | Quartz (low temp), alumina (high temp), silicon carbide (ultra-high temp) |
Applications | Material synthesis (800°C–1600°C), annealing (500°C–1200°C), sintering (up to 1800°C) |
Atmosphere Control | Inert gases, reducing gases, vacuum |
Need a tube furnace tailored to your specific temperature requirements? Contact our experts today for personalized solutions!