Calcination furnaces are designed to operate at high temperatures, typically ranging from 800°C to 1300°C, depending on the specific application. The temperature range is influenced by the materials being processed, the desired chemical or physical transformations, and the efficiency of the furnace. Factors such as temperature control, calibration, and furnace design play a critical role in achieving consistent and accurate results. Additionally, selecting a furnace with a maximum temperature slightly higher than the required usage temperature ensures optimal performance and longevity of the equipment.
Key Points Explained:
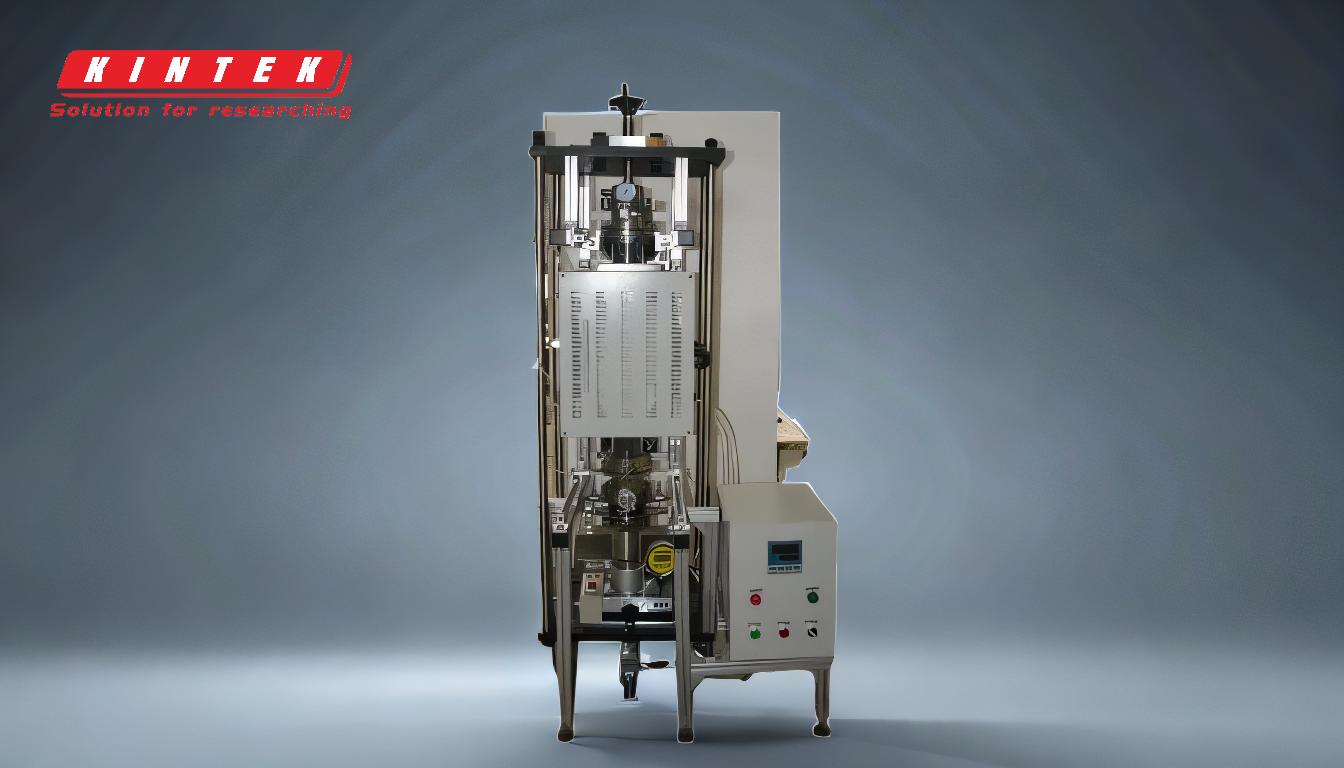
-
Typical Temperature Range for Calcination Furnaces:
- Calcination furnaces generally operate at temperatures between 800°C and 1300°C.
- This range is suitable for processes like thermal decomposition, removal of volatile components, or phase transformations in materials such as ceramics, metals, and minerals.
- The exact temperature depends on the specific application and the material being processed.
-
Factors Influencing Temperature Control:
- Temperature control in furnaces can be affected by:
- Chemical and physical influences: Reactions occurring within the furnace can alter the temperature profile.
- Soiling and deposits: Residues from materials like ceramics, alloys, or soldering materials can impact heat distribution and temperature accuracy.
- Calibration processes: Variations in calibration methods by manufacturers can lead to differences in actual versus set temperatures.
- Temperature control in furnaces can be affected by:
-
Importance of Furnace Design and Configuration:
- When selecting or configuring a calcination furnace, consider:
- Mass of the hot zone: This affects heat distribution and energy efficiency.
- Operating temperature range: Ensure the furnace can handle the required temperatures.
- Gas-flow distribution and loading strategy: These influence uniformity of heating and process outcomes.
- For optimal performance, the furnace's maximum temperature should be 100 to 200°C higher than the actual usage temperature.
- When selecting or configuring a calcination furnace, consider:
-
Material-Specific Temperature Requirements:
- The temperature and duration of calcination depend on:
- The material being processed (e.g., ceramics, metals, or minerals).
- The desired density or properties of the final product.
- For example, sintering furnaces used in dental applications require precise temperature control to achieve the desired density and strength in ceramic or alloy components.
- The temperature and duration of calcination depend on:
-
Continuous vs. Batch Furnaces:
- Continuous furnaces are ideal for processes requiring consistent, permanent temperature conditions, such as annealing or hardening.
- Batch furnaces are more versatile and can handle varying materials and temperature profiles, making them suitable for calcination processes with specific temperature and time requirements.
-
Impact of Temperature Accuracy on Results:
- The accuracy of the actual temperature in the furnace is critical for achieving consistent results.
- Variations in temperature due to calibration differences or furnace construction types can affect the quality of the final product.
- Regular maintenance and calibration are essential to maintain temperature accuracy and ensure reliable performance.
-
Practical Considerations for Purchasers:
- When purchasing a calcination furnace, evaluate:
- The maximum temperature and whether it meets your process requirements.
- The energy efficiency and operating costs of the furnace.
- The durability and maintenance requirements of the equipment.
- Choosing a furnace with a slightly higher maximum temperature than needed provides a safety margin and ensures long-term reliability.
- When purchasing a calcination furnace, evaluate:
By understanding these key points, purchasers can make informed decisions when selecting a calcination furnace, ensuring it meets their specific temperature and process requirements while maintaining efficiency and reliability.
Summary Table:
Aspect | Details |
---|---|
Typical Temperature Range | 800°C to 1300°C, depending on materials and processes. |
Factors Influencing Control | Chemical/physical reactions, soiling, calibration methods. |
Furnace Design | Mass of hot zone, gas-flow distribution, loading strategy. |
Material-Specific Needs | Temperature and duration vary by material (ceramics, metals, minerals). |
Continuous vs. Batch | Continuous for consistent temps; batch for varied profiles. |
Temperature Accuracy | Critical for consistent results; regular calibration is essential. |
Purchasing Considerations | Max temperature, energy efficiency, durability, and maintenance. |
Ready to optimize your high-temperature processes? Contact us today for expert guidance on selecting the perfect calcination furnace!