The temperature of CVD (Chemical Vapor Deposition) coating typically ranges from 500°C to 1200°C, which is significantly higher than that of PVD (Physical Vapor Deposition) coating, which operates between 200°C and 400°C. The higher temperatures in CVD are necessary to facilitate the chemical reactions that form the coating on the substrate. These elevated temperatures enhance film quality by increasing denseness, improving surface reactions, and ensuring better film composition. The substrate temperature plays a crucial role in determining the film's properties, such as defect density, electron mobility, and optical characteristics. Higher temperatures help compensate for suspended bonds on the film surface, reducing defect density and improving overall film quality.
Key Points Explained:
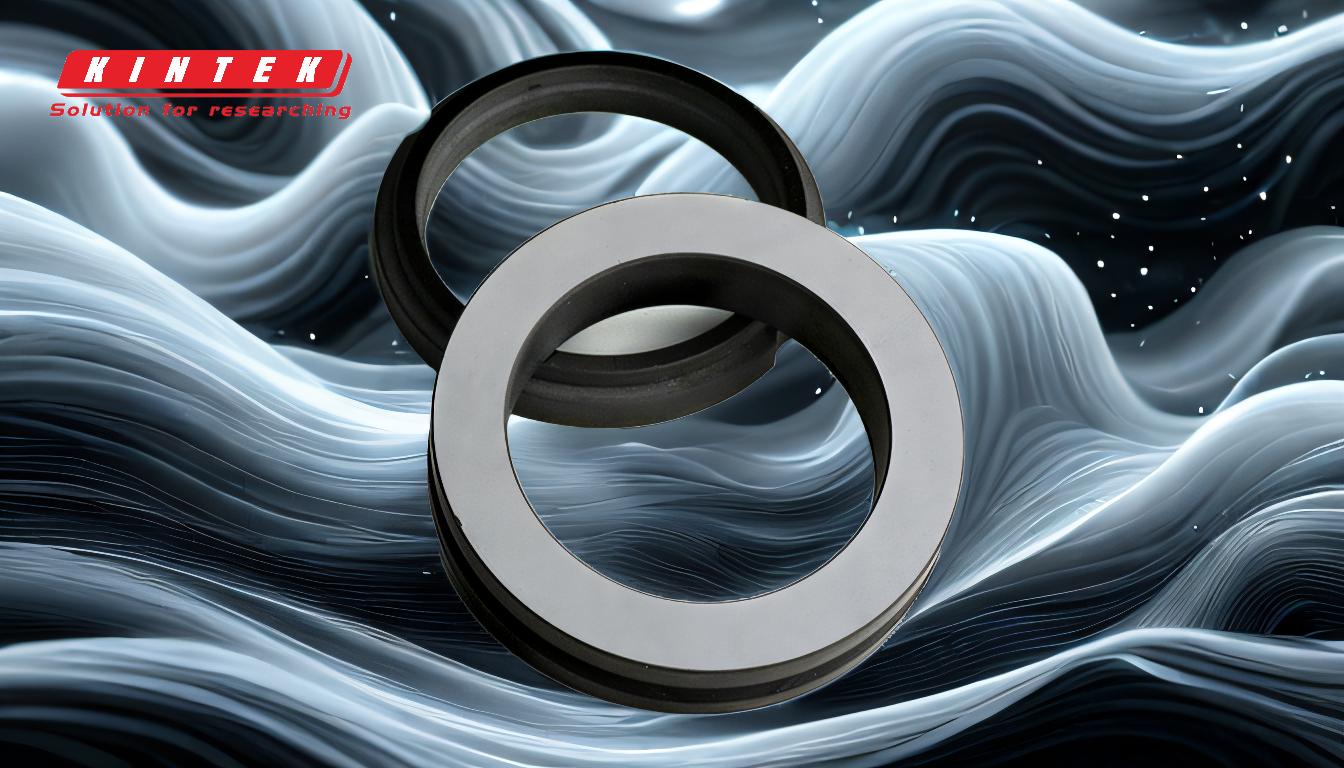
-
Temperature Range for CVD Coating:
- CVD coating processes typically require temperatures between 500°C and 1200°C. This high temperature range is essential for the chemical reactions that deposit the coating material onto the substrate. In contrast, PVD coating operates at much lower temperatures, usually between 200°C and 400°C.
-
Impact of Temperature on Film Quality:
- Higher temperatures in CVD processes lead to better film quality. They increase the denseness of the film, improve surface reactions, and enhance the overall composition of the film. This results in coatings with fewer defects and better mechanical and optical properties.
-
Role of Substrate Temperature:
- The temperature of the substrate during CVD coating significantly influences the local state density, electron mobility, and optical properties of the film. Higher substrate temperatures help compensate for suspended bonds on the film surface, which reduces defect density and improves the film's structural integrity.
-
Comparison with PVD Coating:
- PVD coating processes operate at lower temperatures (200°C to 400°C) compared to CVD. While PVD also produces high-quality coatings, the lower temperature range limits the types of materials that can be effectively deposited and the extent of chemical reactions that can occur during the process.
-
Advantages of Higher Temperatures in CVD:
- Higher temperatures in CVD processes provide several advantages, including the production of films with lower hydrogen content and slower etch rates in both wet and dry plasma etches. This results in more durable and stable coatings that are less prone to pinholes and other defects.
-
Process Steps in CVD:
- Although the references provided focus on PVD, it's important to note that CVD typically involves steps such as vaporization of the precursor material, chemical reaction to form the coating material, and deposition onto the substrate. The high temperatures facilitate these chemical reactions, ensuring a uniform and high-quality coating.
In summary, the temperature of CVD coating is significantly higher than that of PVD, ranging from 500°C to 1200°C. This high temperature is crucial for the chemical reactions that form the coating, leading to films with superior quality, fewer defects, and better mechanical and optical properties. The substrate temperature also plays a vital role in determining the film's characteristics, with higher temperatures generally resulting in better film quality.
Summary Table:
Aspect | CVD Coating | PVD Coating |
---|---|---|
Temperature Range | 500°C to 1200°C | 200°C to 400°C |
Impact on Film Quality | Higher denseness, fewer defects, better composition | High-quality but limited by lower temperatures |
Substrate Temperature Role | Influences defect density, electron mobility, and optical properties | Less impact due to lower temperatures |
Advantages | Durable, stable coatings with lower hydrogen content | Effective for specific materials and applications |
Learn how CVD coating can elevate your material performance—contact our experts today!