The temperature of sinter making varies depending on the material being processed and the desired characteristics of the final product. Sintering typically occurs in a temperature range of 750°C to 1300°C, with some high-temperature sintering processes reaching up to 1700°C. The process involves heating powdered materials to a temperature below their melting point, allowing particles to bond and diffuse, resulting in densification and grain growth. The temperature profile, including ramp rates, hold times, and cooling rates, is critical for achieving optimal material properties. High-temperature sintering can enhance mechanical properties such as tensile strength, bending fatigue strength, and impact energy.
Key Points Explained:
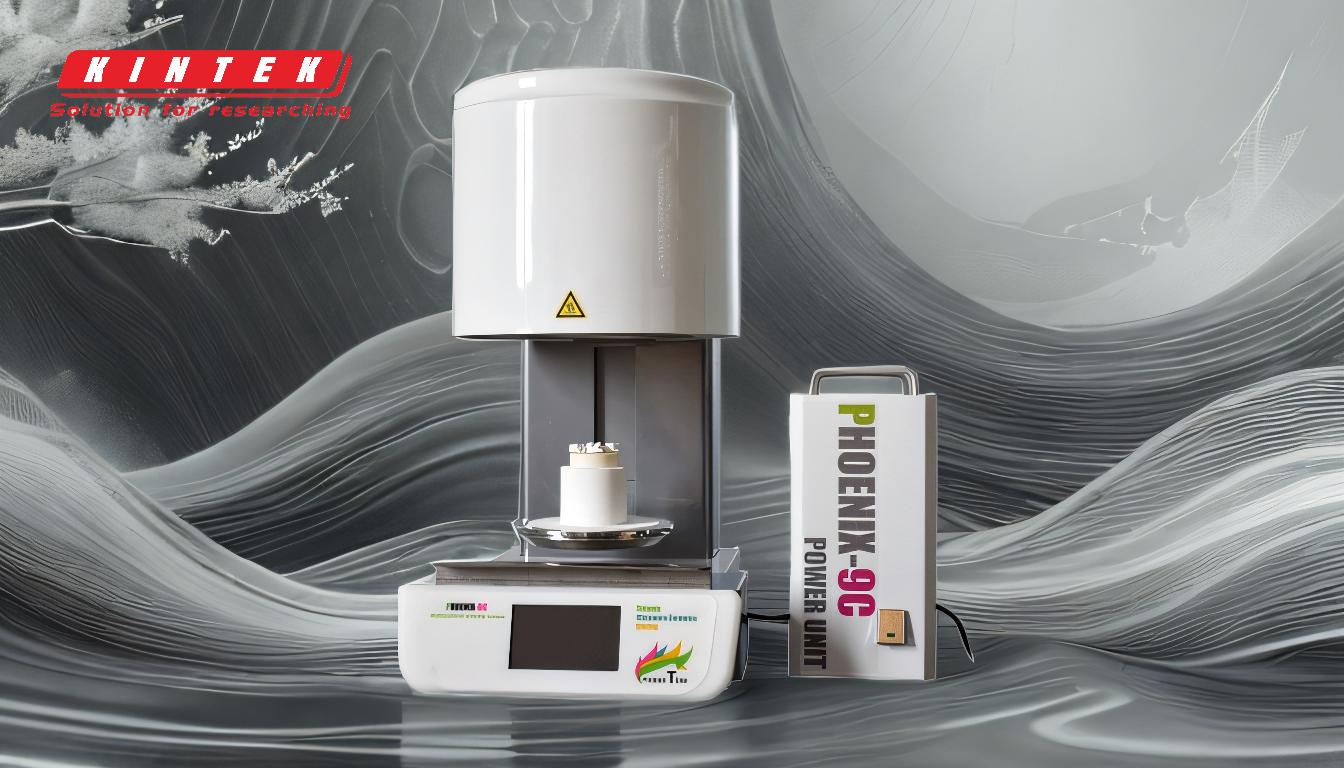
-
Temperature Range for Sintering:
- Sintering typically occurs between 750°C and 1300°C, depending on the material and desired properties.
- Some high-temperature sintering processes can reach up to 1700°C, especially for materials with extremely high melting points like tungsten and molybdenum.
-
Importance of Temperature Control:
- Ramp Rate: The rate at which the temperature increases from 900°C to the top temperature is critical. A controlled ramp rate ensures uniform heating and prevents thermal stresses.
- Hold Time: Maintaining a consistent temperature during the hold time allows for proper diffusion and bonding of particles.
- Cooling Rate: The rate of cooling back to about 900°C is also crucial. Controlled cooling prevents cracking and ensures the desired microstructure.
-
Effect of Temperature on Material Properties:
- High-Temperature Sintering: Temperatures at the higher end of the range (up to 1700°C) can significantly improve mechanical properties such as tensile strength, bending fatigue strength, and impact energy.
- Low-Temperature Sintering: Temperatures at the lower end (750°C to 900°C) are sufficient for some materials but may not achieve the same level of densification or mechanical strength.
-
Atmosphere and Cooling Rate:
- The sintering atmosphere (air, vacuum, or inert gases like argon/nitrogen) plays a role in the process, but temperature remains the primary variable affecting the outcome.
- Cooling rate must be carefully managed to avoid defects and ensure the final product meets specifications.
-
Applications and Materials:
- Sintering is commonly used for materials with high melting points, such as ceramics, metals, and composites.
- The process is widely applied in industries like aerospace, automotive, and electronics, where high-performance materials are required.
By understanding these key points, a purchaser can better evaluate sintering equipment and consumables, ensuring they meet the specific temperature and process requirements for their application.
Summary Table:
Aspect | Details |
---|---|
Temperature Range | 750°C to 1300°C (up to 1700°C for high-temperature sintering) |
Key Factors | Ramp rate, hold time, cooling rate, and sintering atmosphere |
Material Properties | Improved tensile strength, bending fatigue strength, and impact energy |
Applications | Aerospace, automotive, electronics, and high-performance materials |
Need help selecting the right sintering equipment? Contact our experts today for tailored solutions!