The temperature of sintered iron typically ranges between 900°C and 1,500°C, depending on the desired density, material properties, and sintering method. Sintering is a critical process that involves heating iron powder or particles below their melting point to bond them into a solid structure. The exact temperature is influenced by factors such as the material composition, particle size, and the presence of additives or binders. Higher temperatures generally lead to denser and stronger sintered iron, but the process must be carefully controlled to avoid defects such as warping or excessive grain growth. The sintering environment (e.g., air, vacuum, or inert gas) and cooling rate also play significant roles in determining the final properties of the sintered iron.
Key Points Explained:
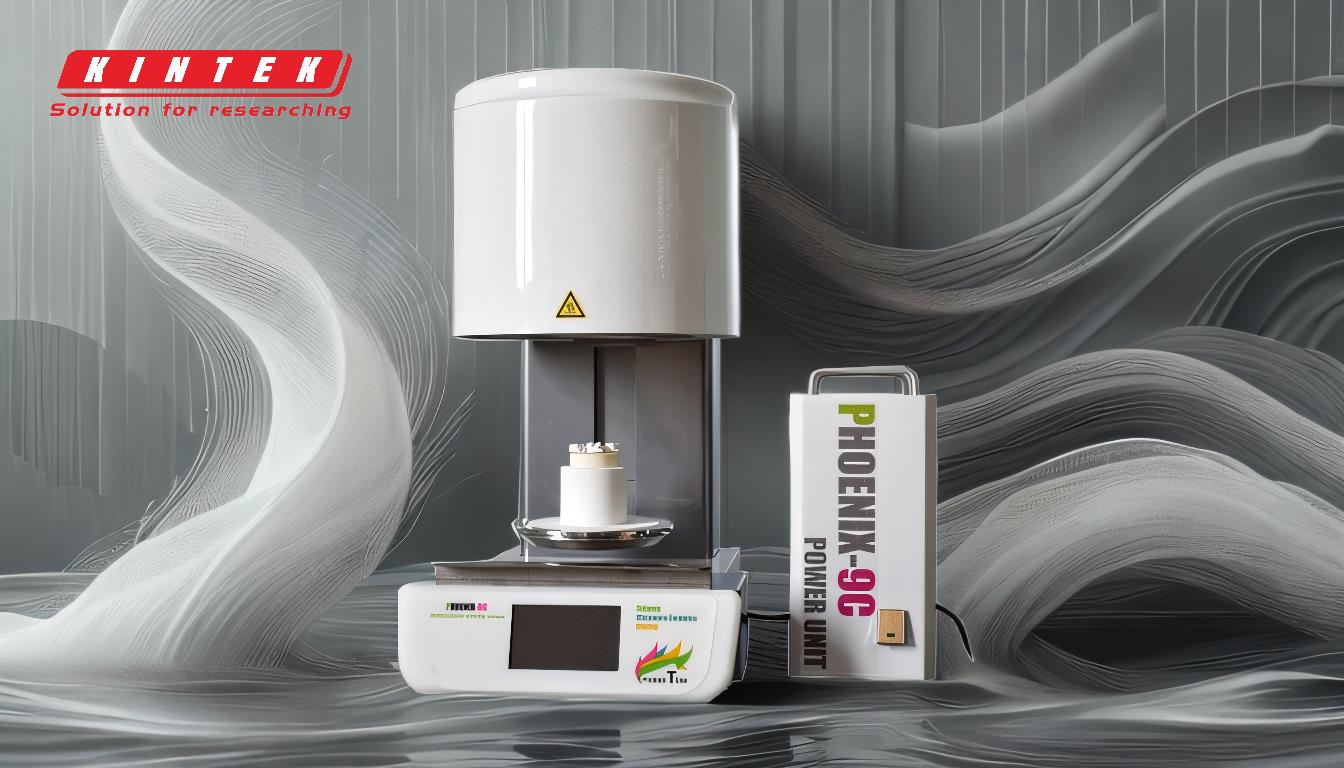
-
Temperature Range for Sintered Iron:
- Sintered iron is typically processed at temperatures between 900°C and 1,500°C.
- The exact temperature depends on the desired density, material properties, and sintering method.
- Higher temperatures (closer to 1,500°C) result in denser and stronger sintered iron, as they promote better particle bonding and reduced porosity.
-
Factors Influencing Sintering Temperature:
- Material Composition: The presence of additives or binders can alter the optimal sintering temperature.
- Particle Size: Smaller particles sinter at lower temperatures due to their higher surface energy, which enhances densification.
- Sintering Environment: The atmosphere (e.g., air, vacuum, or inert gas) affects the sintering kinetics and final properties. For example, vacuum sintering prevents oxidation and allows for higher temperatures.
- Heating and Cooling Rates: Controlled heating and cooling rates are critical to avoid defects such as warping or excessive grain growth.
-
Sintering Process Parameters:
- Temperature Ramp Rate: The rate at which the temperature is increased from 900°C to the sintering temperature is crucial. A controlled ramp rate ensures uniform heating and minimizes thermal stress.
- Hold Time: The duration at the sintering temperature affects the degree of densification and bonding.
- Cooling Rate: Slow cooling from the sintering temperature back to around 900°C helps achieve the desired microstructure and mechanical properties.
-
Impact of Sintering Temperature on Material Properties:
- Density: Higher sintering temperatures result in denser iron, often reaching close to the theoretical maximum density.
- Strength: High-temperature sintering increases tensile strength, bending fatigue strength, and impact energy.
- Microstructure: Temperature influences grain size and phase transformations, which in turn affect mechanical properties.
-
Sintering Techniques and Equipment:
- Furnace Types: Sintering can be carried out in belt conveyor, push, or batch furnaces, depending on the production scale and requirements.
- Controlled Atmosphere: The use of a controlled atmosphere (e.g., vacuum or inert gas) is essential to prevent oxidation and achieve uniform sintering.
- Layer Thickness and Speed: For large-scale sintering, layer thickness (250-500mm) and machine speed (1.5-4m/min) are controlled to ensure consistent sintering.
-
Practical Considerations for Sintered Iron:
- Defect Prevention: Careful control of temperature, heating rate, and cooling rate is necessary to avoid defects such as warping, cracking, or excessive grain growth.
- Optimization: The sintering process must be optimized based on the specific application and desired properties of the sintered iron.
- Energy Efficiency: Balancing temperature and process parameters can improve energy efficiency and reduce production costs.
In summary, the temperature of sintered iron is a critical parameter that must be carefully controlled to achieve the desired density, strength, and microstructure. The sintering process involves a combination of temperature control, atmosphere management, and process optimization to produce high-quality sintered iron for various industrial applications.
Summary Table:
Parameter | Details |
---|---|
Temperature Range | 900°C to 1,500°C |
Key Influencing Factors | Material composition, particle size, sintering environment, cooling rate |
Impact on Properties | Higher temperatures increase density, strength, and reduce porosity |
Sintering Equipment | Belt conveyor, push, or batch furnaces with controlled atmosphere |
Defect Prevention | Controlled heating/cooling rates and optimized process parameters |
Need help optimizing your sintering process? Contact our experts today for tailored solutions!