A rotary furnace, also known as a rotating furnace, is a versatile piece of equipment used in various industrial processes such as calcination, sintering, and heat treatment. The temperature of a rotary furnace typically ranges between 600°C and 1200°C, depending on the specific application and materials being processed. Some specialized rotary furnaces can reach temperatures up to 1000°C or higher, making them suitable for high-temperature applications. The furnace operates by feeding materials into the higher end, where they are heated by burners using fuels like pulverized coal, heavy oil, or gaseous fuel. The flue gas exits from the higher end, creating a counterflow with the materials. This design ensures efficient heat transfer and uniform temperature distribution.
Key Points Explained:
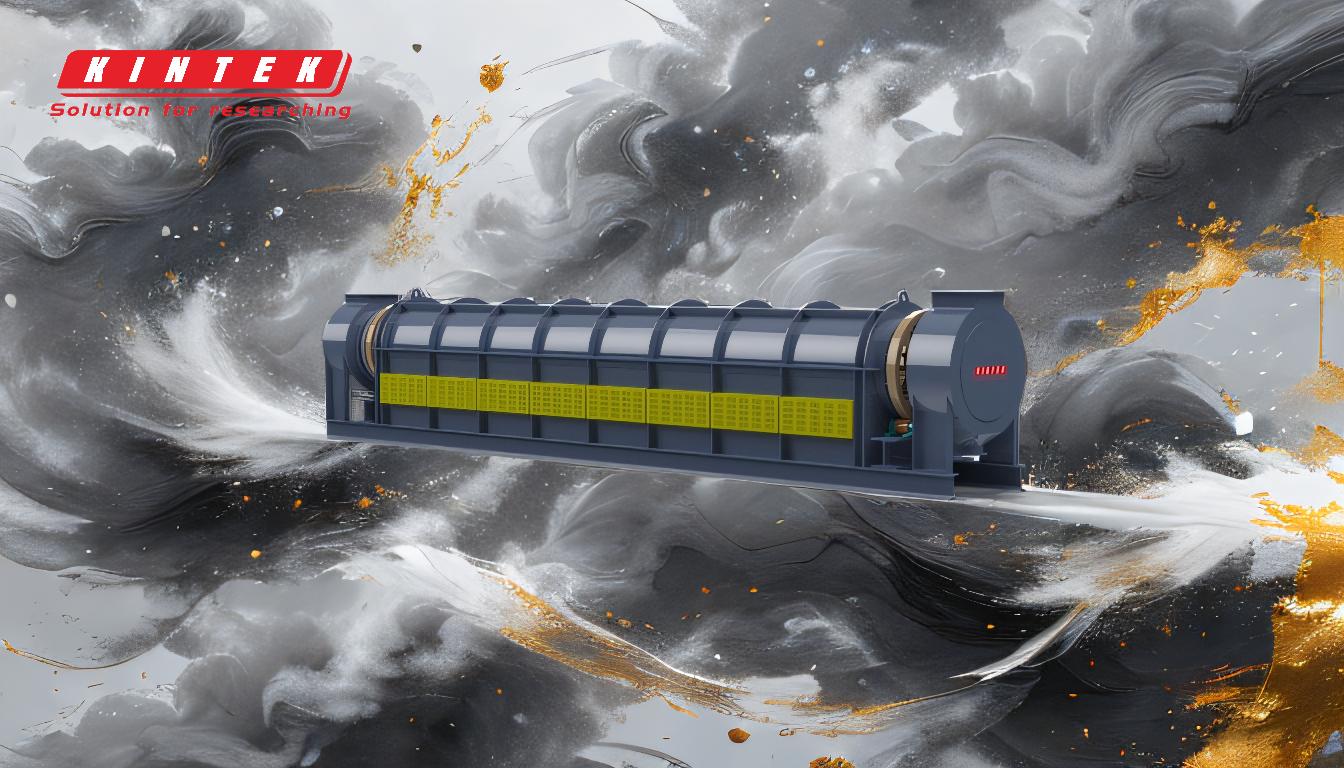
-
Temperature Range of Rotary Furnaces:
- The operating temperature of a rotary furnace typically ranges between 600°C and 1200°C, depending on the application. For example, processes like calcination or sintering may require specific temperature ranges to achieve the desired material properties.
- Some advanced rotary furnaces, such as rotary tube furnaces, can reach temperatures up to 1000°C or higher, making them suitable for high-temperature applications like material testing or advanced heat treatment.
-
Factors Influencing Temperature:
- Material Type: The type of material being processed significantly influences the required temperature. For instance, metals and ceramics often require higher temperatures compared to organic materials.
- Application: Different industrial processes, such as calcination, sintering, or heat treatment, have specific temperature requirements. For example, calcination of limestone typically occurs at around 900°C, while sintering of ceramics may require temperatures closer to 1200°C.
- Furnace Design: The design and insulation of the furnace also play a role in determining the maximum achievable temperature. Well-insulated furnaces can maintain higher temperatures more efficiently.
-
Fuel and Combustion System:
- Rotary furnaces use fuels such as pulverized coal, heavy oil, or gaseous fuels to generate heat. The combustion system is designed to inject fuel into the furnace head end, where it burns and heats the materials.
- The flue gas exits from the higher end, creating a counterflow with the materials. This design ensures efficient heat transfer and uniform temperature distribution throughout the furnace.
-
Applications of Rotary Furnaces:
- Calcination: Used to thermally decompose materials like limestone or gypsum at high temperatures.
- Sintering: A process used to compact and form solid materials, often used in ceramic and metal processing.
- Heat Treatment: Used to alter the physical and chemical properties of materials, such as hardening or annealing metals.
-
Comparison with Other Furnaces:
- Rotary furnaces are often compared to vertical vacuum furnaces, which typically operate at temperatures ranging from 538°C to 1315°C. While both types of furnaces are used for high-temperature applications, rotary furnaces are particularly suited for continuous processing of bulk materials due to their rotating design.
-
Advantages of Rotary Furnaces:
- Uniform Heating: The rotating mechanism ensures that materials are evenly heated, reducing the risk of hot spots or uneven processing.
- Versatility: Rotary furnaces can handle a wide range of materials and processes, making them suitable for diverse industrial applications.
- Efficiency: The counterflow design maximizes heat transfer efficiency, reducing fuel consumption and operational costs.
By understanding these key points, equipment and consumable purchasers can make informed decisions when selecting a rotating furnace for their specific needs. Whether for high-temperature processing or continuous material treatment, rotary furnaces offer a reliable and efficient solution.
Summary Table:
Aspect | Details |
---|---|
Temperature Range | 600°C to 1200°C, with some models reaching up to 1000°C or higher. |
Factors Influencing | Material type, application, and furnace design. |
Fuel Types | Pulverized coal, heavy oil, or gaseous fuels. |
Key Applications | Calcination, sintering, and heat treatment. |
Advantages | Uniform heating, versatility, and high efficiency. |
Need a rotary furnace for your industrial needs? Contact us today to find the perfect solution!