Vacuum brazing is a specialized process used to join metals in a vacuum environment, ensuring clean, oxidation-free joints. The temperature for vacuum brazing typically ranges between 500°C and 1200°C, depending on the materials being joined and the filler metal used. The process involves placing assembled parts in a vacuum brazing furnace, evacuating the chamber to remove residual gases, and gradually heating to the brazing temperature. This allows the filler metal to melt, flow, and bond with the base metals, creating a strong, durable joint. The precise temperature and heating profile are critical to achieving optimal results, and modern vacuum furnaces are equipped with advanced control systems to ensure uniformity and accuracy.
Key Points Explained:
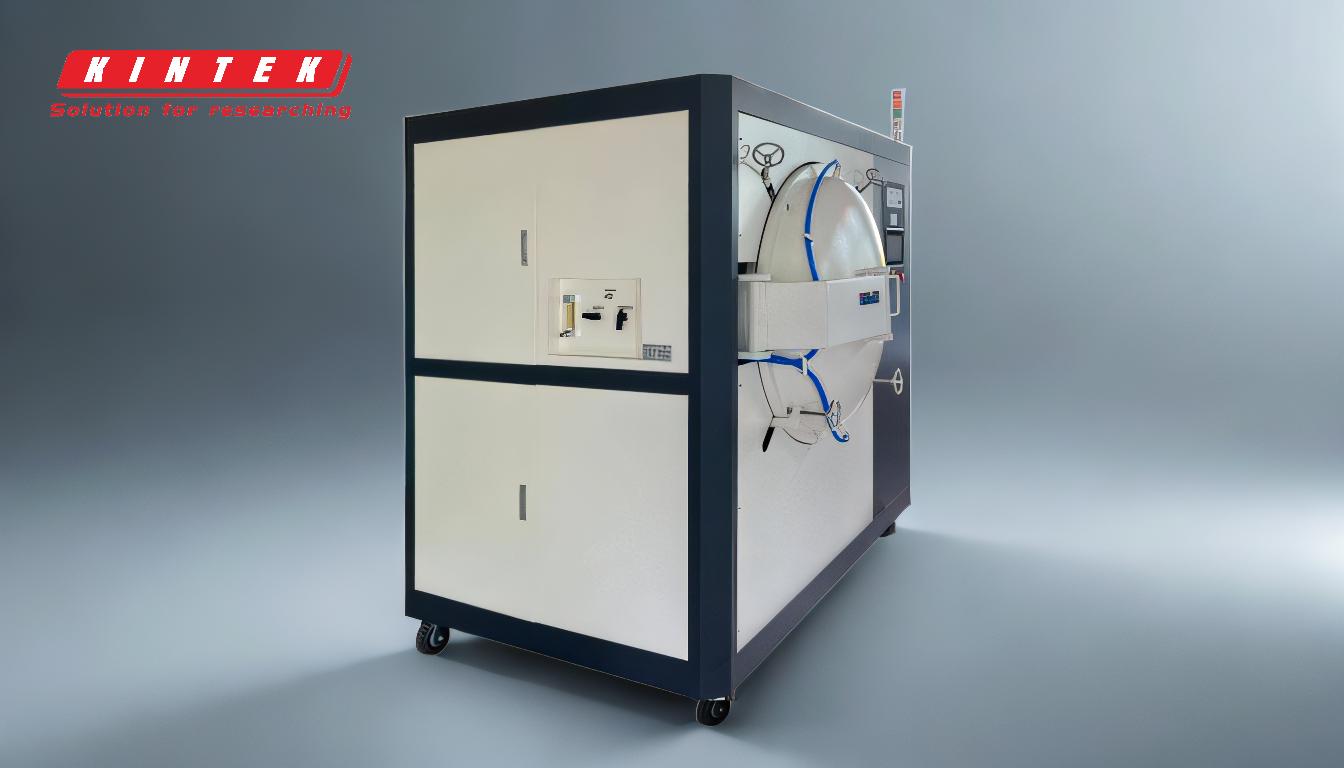
-
Temperature Range for Vacuum Brazing:
- The typical temperature range for vacuum brazing is between 500°C and 1200°C. This range is chosen based on the melting point of the filler metal and the thermal properties of the base materials.
- For example, aluminum alloys are typically brazed at lower temperatures (around 500°C to 600°C), while nickel-based alloys may require temperatures up to 1200°C.
-
Role of the Vacuum Brazing Furnace:
- A vacuum brazing furnace is designed to create a controlled environment free from oxygen and other reactive gases. This prevents oxidation and ensures clean, high-quality joints.
- The furnace is evacuated to remove residual gases, and the temperature is gradually increased to the brazing temperature. This controlled heating process is essential for proper filler metal flow and bonding.
-
Heating and Cooling Process:
- The heating process in a vacuum brazing furnace is carefully controlled to ensure uniform temperature distribution. This is achieved using multiple heating zones and advanced temperature control systems, such as PID controllers or PLC systems.
- After brazing, the furnace is cooled slowly to prevent thermal stress and warping. Some furnaces also offer gas quenching options for faster cooling when required.
-
Temperature Uniformity and Control:
- Temperature uniformity is critical in vacuum brazing to ensure consistent joint quality. Factors such as insulation design, heating zone configuration, and gas flow patterns influence uniformity.
- Modern vacuum furnaces are equipped with thermocouples and temperature controllers to monitor and adjust the temperature accurately. A minimum of three heating zones is typically required for proper power input trimming and adjustment.
-
Maximum Operating Temperature:
- The maximum operating temperature of a vacuum brazing furnace can vary widely, typically ranging from 1,500°F (815°C) to 5,400°F (2,982°C). However, most brazing processes are conducted at the lower end of this range.
- For example, a typical vacuum brazing furnace might have a maximum operating temperature of 1400°C, which is sufficient for most brazing applications.
-
Process Monitoring and Safety:
- Operators must monitor key parameters such as water pressure, water flow, and water temperature during the heating process to ensure safe and efficient operation.
- In case of water supply interruption, a backup system should be activated immediately to prevent damage to the furnace and ensure continuous cooling.
-
Typical Heating Program:
- A standard vacuum brazing program involves pumping the system to base pressure, raising the hot zone temperature to 800°C, and holding it for 20 minutes. The temperature is then gradually increased to 1100°C over an hour and held for 1.5 hours.
- This step-by-step heating process ensures proper filler metal melting and bonding while minimizing thermal stress on the components.
-
Applications and Specifications:
- Vacuum brazing is widely used in industries such as aerospace, automotive, and electronics, where high-strength, oxidation-free joints are required.
- A typical vacuum brazing furnace might have a working zone of 1200 x 1200 x 1200 mm, a maximum gross load of 1500 kg, and the ability to operate with partial pressures of nitrogen, argon, or hydrogen. These specifications make it suitable for a wide range of applications.
By understanding these key points, equipment and consumable purchasers can make informed decisions when selecting a vacuum brazing furnace and optimizing the brazing process for their specific needs.
Summary Table:
Key Aspect | Details |
---|---|
Temperature Range | 500°C to 1200°C, depending on materials and filler metal. |
Heating Process | Controlled, gradual heating in a vacuum furnace for uniform distribution. |
Cooling Process | Slow cooling to prevent thermal stress; gas quenching options available. |
Maximum Operating Temp | Up to 1400°C for most brazing applications. |
Typical Heating Program | Pump to base pressure, heat to 800°C, hold, then increase to 1100°C. |
Applications | Aerospace, automotive, electronics for high-strength, oxidation-free joints. |
Ready to optimize your vacuum brazing process? Contact our experts today for tailored solutions!