Low Pressure Chemical Vapor Deposition (LPCVD) is a widely used technique in semiconductor manufacturing and material science for depositing thin films on substrates. The temperature range for LPCVD processes typically varies depending on the specific material being deposited, the desired film properties, and the equipment used. Generally, LPCVD operates at temperatures ranging from 300°C to 900°C. This range allows for the deposition of high-quality films with good uniformity and conformality, which are critical for applications in microelectronics, MEMS, and other advanced technologies.
Key Points Explained:
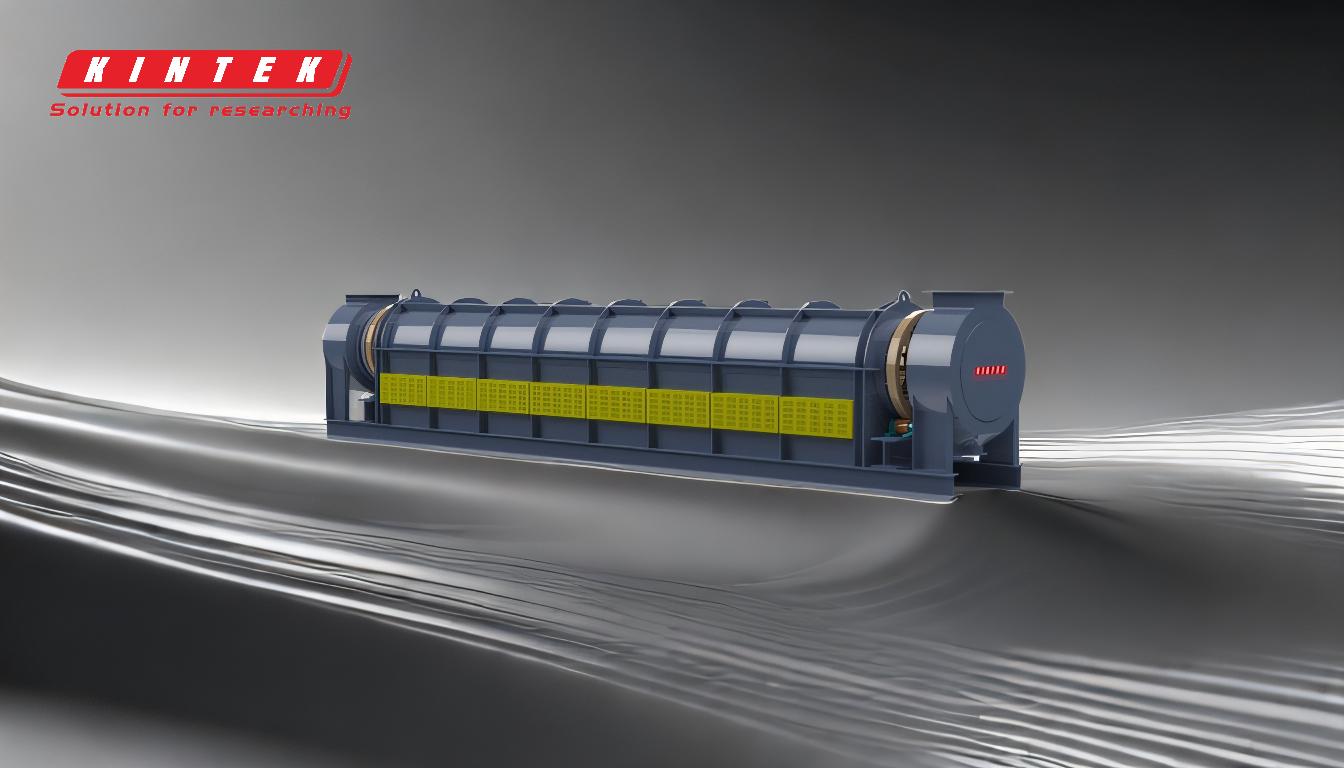
-
Typical Temperature Range for LPCVD:
- LPCVD processes generally operate within a temperature range of 300°C to 900°C. This range is chosen based on the specific material being deposited and the desired film properties.
- For example, silicon nitride (Si₃N₄) is often deposited at temperatures around 700°C to 900°C, while polysilicon films are typically deposited at 550°C to 650°C.
-
Factors Influencing Temperature Selection:
- Material Properties: The thermal stability and reactivity of the precursor materials determine the required temperature. Higher temperatures are often needed for materials that require more energy to decompose or react.
- Film Quality: Higher temperatures generally improve film quality by enhancing surface mobility and reducing defects. However, excessive temperatures can lead to unwanted reactions or degradation of the substrate.
- Deposition Rate: Temperature directly affects the deposition rate. Higher temperatures typically result in faster deposition, but this must be balanced against potential adverse effects on film quality.
-
Applications of LPCVD at Different Temperatures:
- Low-Temperature LPCVD (300°C to 500°C): Used for depositing materials that are sensitive to high temperatures, such as certain polymers or organic films. These temperatures are also suitable for substrates that cannot withstand high thermal stress.
- Medium-Temperature LPCVD (500°C to 700°C): Commonly used for depositing polysilicon and silicon dioxide films, which are essential in semiconductor device fabrication.
- High-Temperature LPCVD (700°C to 900°C): Ideal for depositing high-quality silicon nitride and other refractory materials that require high thermal energy for proper film formation.
-
Equipment Considerations:
- Furnace Design: LPCVD reactors are designed to maintain precise temperature control across the entire substrate. Multi-zone furnaces are often used to ensure uniform heating.
- Pressure Control: LPCVD operates at low pressures (typically 0.1 to 1 Torr), which reduces gas-phase reactions and improves film uniformity. The combination of low pressure and precise temperature control is key to achieving high-quality films.
-
Challenges and Trade-offs:
- Thermal Budget: High-temperature LPCVD processes can impose a significant thermal budget on the substrate, potentially affecting its structural integrity or introducing unwanted dopant diffusion.
- Uniformity and Conformality: Achieving uniform and conformal films at lower temperatures can be challenging, as surface mobility is reduced. Advanced reactor designs and process optimization are often required to address these issues.
In summary, the temperature range for LPCVD is highly dependent on the specific application and material requirements. By carefully selecting the appropriate temperature and optimizing process parameters, high-quality thin films can be deposited for a wide range of advanced technologies.
Summary Table:
Aspect | Details |
---|---|
Typical Temperature | 300°C to 900°C |
Low-Temperature LPCVD | 300°C to 500°C (sensitive materials, low thermal stress substrates) |
Medium-Temperature | 500°C to 700°C (polysilicon, silicon dioxide for semiconductors) |
High-Temperature | 700°C to 900°C (silicon nitride, refractory materials) |
Key Factors | Material properties, film quality, deposition rate, equipment design |
Applications | Microelectronics, MEMS, advanced material science |
Need help optimizing your LPCVD process? Contact our experts today for tailored solutions!