Physical Vapor Deposition (PVD) is a versatile and precise coating technique used to deposit thin films of materials onto substrates. The thickness of PVD coatings typically ranges from 0.00004 to 0.0002 inches (or approximately 1 to 5 micrometers). This range is ideal for applications requiring tight tolerances, such as in the aerospace, medical, and electronics industries. The thickness of PVD coatings is influenced by factors such as deposition parameters, material properties, and process conditions. Below, we explore the key aspects of PVD thickness and the factors that influence it.
Key Points Explained:
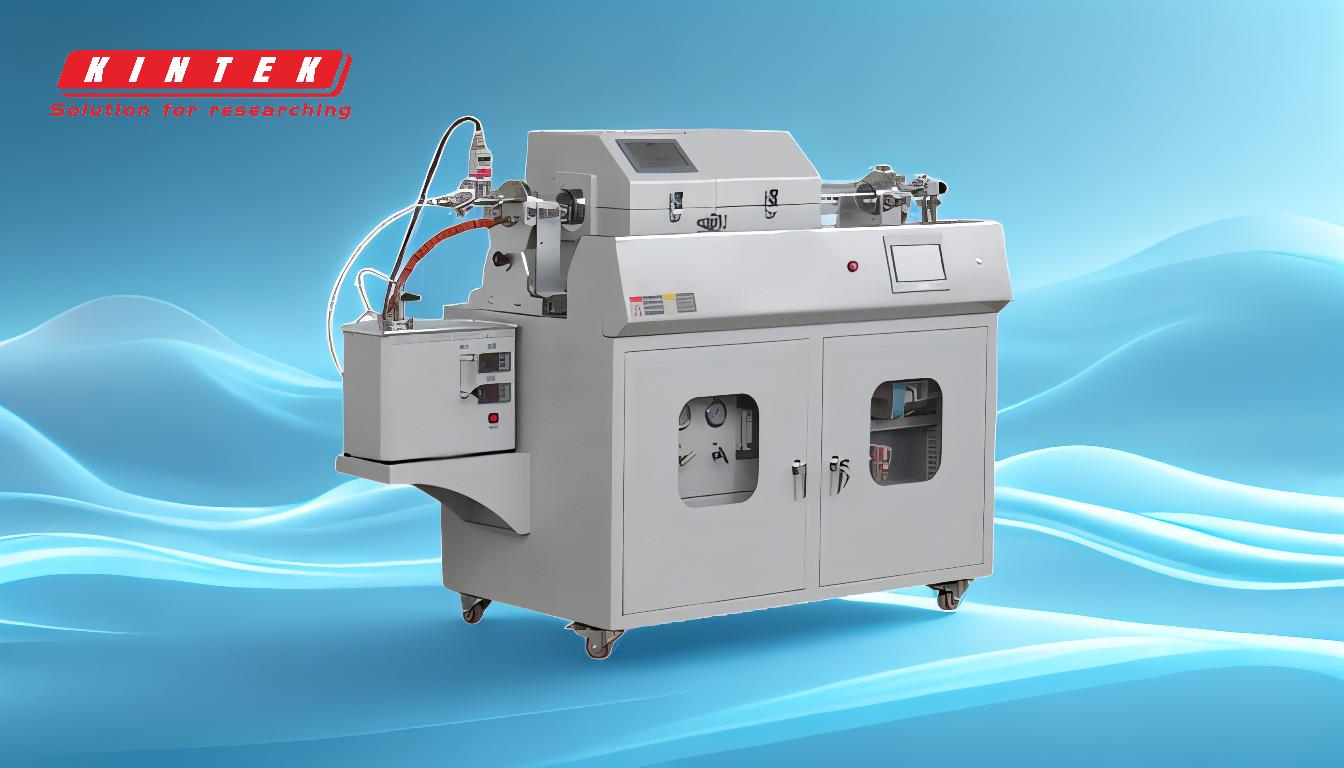
-
Typical Thickness Range of PVD Coatings
- The average thickness of PVD coatings is 0.00004 to 0.0002 inches (1 to 5 micrometers).
- This range is suitable for applications requiring high precision, such as cutting tools, medical devices, and optical components.
- The thin nature of PVD coatings ensures minimal dimensional changes to the substrate, making it ideal for tight-tolerance applications.
-
Factors Influencing PVD Coating Thickness
-
Deposition Time and Power:
- Longer deposition times and higher power levels result in thicker coatings.
- For example, sputtering processes are influenced by the cycle time and the power applied to the target material.
-
Material Properties:
- The mass and evaporation rate of the source material affect the deposition rate and final thickness.
- Materials with higher molecular weights may require longer deposition times to achieve the desired thickness.
-
Substrate Preparation:
- A smooth and clean substrate surface ensures uniform deposition, while rough surfaces may lead to non-uniform thickness.
-
Vacuum Conditions:
- A higher degree of vacuum improves the free path of source material molecules, reducing impurities and ensuring consistent thickness.
-
Energy of Coating Particles:
- The energy level of particles during deposition (ranging from tens to thousands of electron volts) influences the density and thickness of the coating.
-
Deposition Time and Power:
-
Advantages of PVD Coating Thickness
-
Precision and Uniformity:
- PVD coatings replicate the substrate's surface finish, ensuring uniform thickness even on complex geometries.
-
No Excessive Build-Up:
- The thin nature of PVD coatings prevents excessive material build-up, maintaining the substrate's dimensions.
-
Environmental Friendliness:
- PVD is a clean process that produces pure, high-quality coatings without harmful byproducts.
-
Precision and Uniformity:
-
Applications of PVD Coating Thickness
-
Cutting Tools:
- Thin PVD coatings enhance wear resistance and extend tool life without altering the tool's dimensions.
-
Medical Devices:
- PVD coatings provide biocompatibility and corrosion resistance in thin, precise layers.
-
Optics and Electronics:
- The ability to deposit ultra-thin, uniform coatings makes PVD ideal for optical lenses, semiconductors, and displays.
-
Cutting Tools:
-
Comparison with Other Coating Methods
- PVD coatings are generally thinner than those produced by Chemical Vapor Deposition (CVD) or electroplating.
- Unlike CVD, PVD does not require high temperatures or heat treatment, making it suitable for temperature-sensitive substrates.
In summary, the thickness of PVD coatings is a critical parameter that depends on various process and material factors. The ability to control thickness precisely makes PVD a preferred choice for industries requiring high-performance, durable, and dimensionally accurate coatings.
Summary Table:
Aspect | Details |
---|---|
Typical Thickness Range | 0.00004 to 0.0002 inches (1 to 5 micrometers) |
Key Influencing Factors | Deposition time, power, material properties, substrate preparation, vacuum |
Advantages | Precision, uniformity, minimal build-up, environmental friendliness |
Applications | Cutting tools, medical devices, optics, electronics |
Comparison with Other Methods | Thinner than CVD and electroplating, no high temperatures required |
Discover how PVD coatings can enhance your applications—contact our experts today!