DC sputtering is a versatile and widely used technique in the field of thin film deposition, particularly in industries requiring high precision and durability. It involves the use of a direct current (DC) to ionize inert gas atoms, which then bombard a target material, causing atoms to be ejected and deposited onto a substrate. This process is essential for creating thin films with specific properties, such as uniformity, low roughness, and high density. DC sputtering is employed in various applications, including semiconductor manufacturing, optical coatings, and protective layers for aerospace and medical tools. Its ability to produce high-quality, durable coatings makes it indispensable in modern technology and material science.
Key Points Explained:
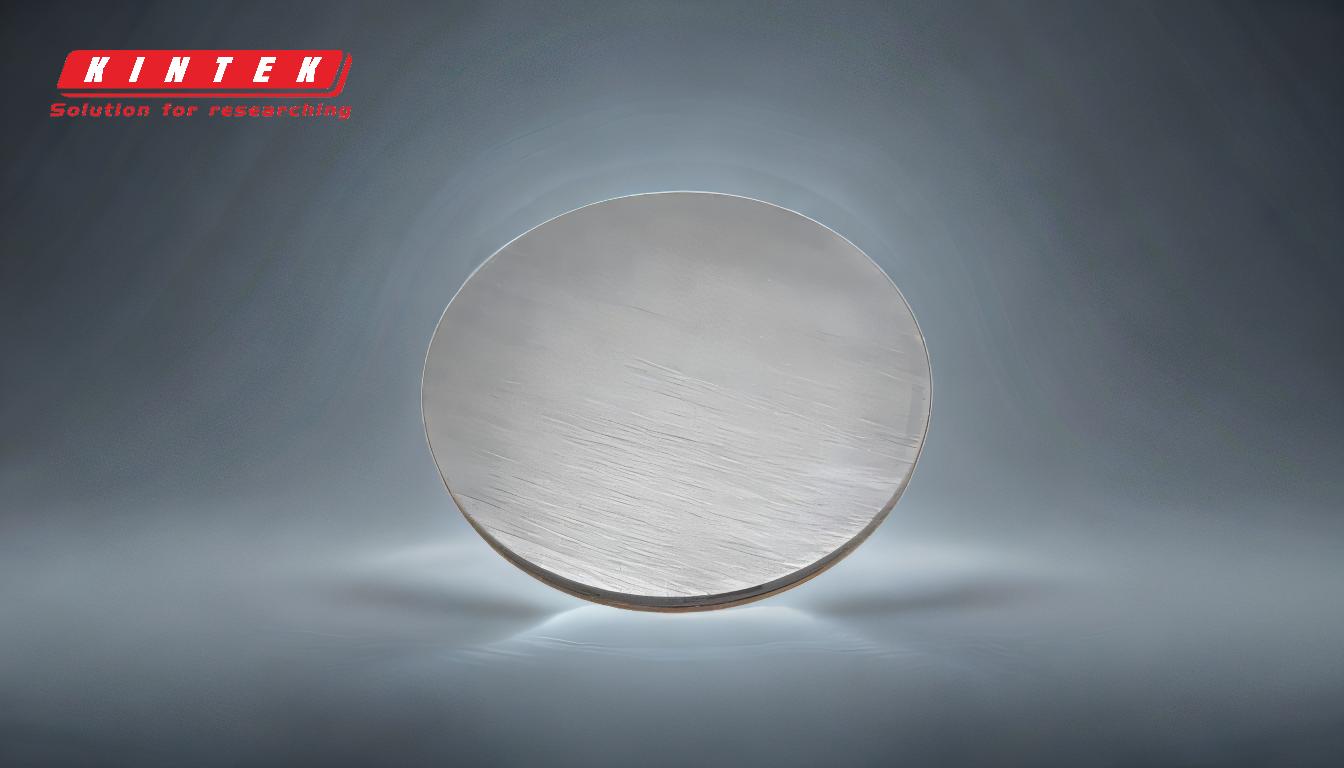
-
Definition and Mechanism of DC Sputtering:
- DC sputtering is a physical vapor deposition (PVD) technique where a target material is bombarded with ionized gas molecules (typically argon) in a low-pressure environment. The collision of gas ions with the target ejects microscopic particles, which then deposit onto a nearby substrate, forming a thin film.
- This process is driven by a direct current (DC) voltage, which ionizes the gas and accelerates the ions toward the target material.
-
Applications in Thin Film Deposition:
- Semiconductor Industry: DC sputtering is used to create chemically resistant thin film coatings essential for semiconductor devices. These coatings protect delicate components and enhance performance.
- Optical Industry: It is employed to produce polarization filters and other optical coatings that require precise thickness and uniformity.
- Aerospace and Defense: DC sputtering is used to apply gadolinium films for neutron radiography, a critical technique in these sectors.
- Architectural Glass: Large area surfaces, such as energy-efficient windows, are coated using DC sputtering to improve durability and functionality.
-
Advantages of DC Sputtering:
- Uniformity: The process ensures a uniform distribution of the deposited material, which is crucial for applications requiring consistent film properties.
- Low Roughness: Films produced by DC sputtering exhibit low surface roughness, enhancing their performance in optical and electronic applications.
- High Density: The deposited films are dense and durable, making them suitable for protective coatings and corrosion resistance.
-
Specific Material Applications:
- Molybdenum, Tantalum, and Niobium-Based Films: These materials are commonly deposited using DC sputtering due to their excellent mechanical and electrical properties. For example, molybdenum thin films improve the scratch resistance of nickel-titanium shape memory alloys.
- Dielectric Stacks: DC sputtering is used to create dielectric stacks that electrically isolate surgical tools, ensuring safety and functionality in medical applications.
-
Role in Advanced Material Development:
- DC sputtering is a key technique for developing advanced materials and coatings. It enables the creation of thinner, lighter, and more durable products, which are essential in industries such as electronics, aerospace, and healthcare.
-
Comparison with Other Sputtering Techniques:
- While DC sputtering is highly effective for conductive materials, other sputtering techniques, such as RF (Radio Frequency) sputtering, are used for non-conductive materials. DC sputtering is preferred for its simplicity and efficiency in depositing metals and alloys.
-
Future Trends and Innovations:
- The ongoing development of DC sputtering technology focuses on improving deposition rates, reducing costs, and expanding the range of materials that can be deposited. Innovations in target design and gas ionization techniques are expected to enhance the performance and versatility of DC sputtering in various industries.
In summary, DC sputtering is a critical technology in modern material science and industrial applications. Its ability to produce high-quality, durable thin films with precise properties makes it indispensable in fields ranging from electronics to aerospace. As technology advances, DC sputtering is likely to play an even more significant role in the development of innovative materials and coatings.
Summary Table:
Key Aspect | Details |
---|---|
Definition | A PVD technique using DC voltage to ionize gas and deposit thin films. |
Applications | Semiconductors, optical coatings, aerospace, medical tools, and more. |
Advantages | Uniformity, low roughness, high density, and durability. |
Materials Used | Molybdenum, tantalum, niobium, and dielectric stacks. |
Future Trends | Improved deposition rates, cost reduction, and expanded material range. |
Discover how DC sputtering can enhance your projects—contact our experts today!