E-beam evaporation is a highly efficient thin-film deposition technique used primarily in industries requiring high-purity, high-density coatings. It involves using an electron beam to heat and vaporize a target material in a vacuum environment, which then deposits onto a substrate. This method is known for its rapid deposition rates, excellent material utilization, and ability to work with a wide range of materials, including metals, ceramics, and semiconductors. However, it is limited by its line-of-sight nature, making it unsuitable for coating complex geometries. Despite its limitations, e-beam evaporation is widely used in applications such as optical coatings, semiconductor manufacturing, and nanotechnology due to its precision and high-quality results.
Key Points Explained:
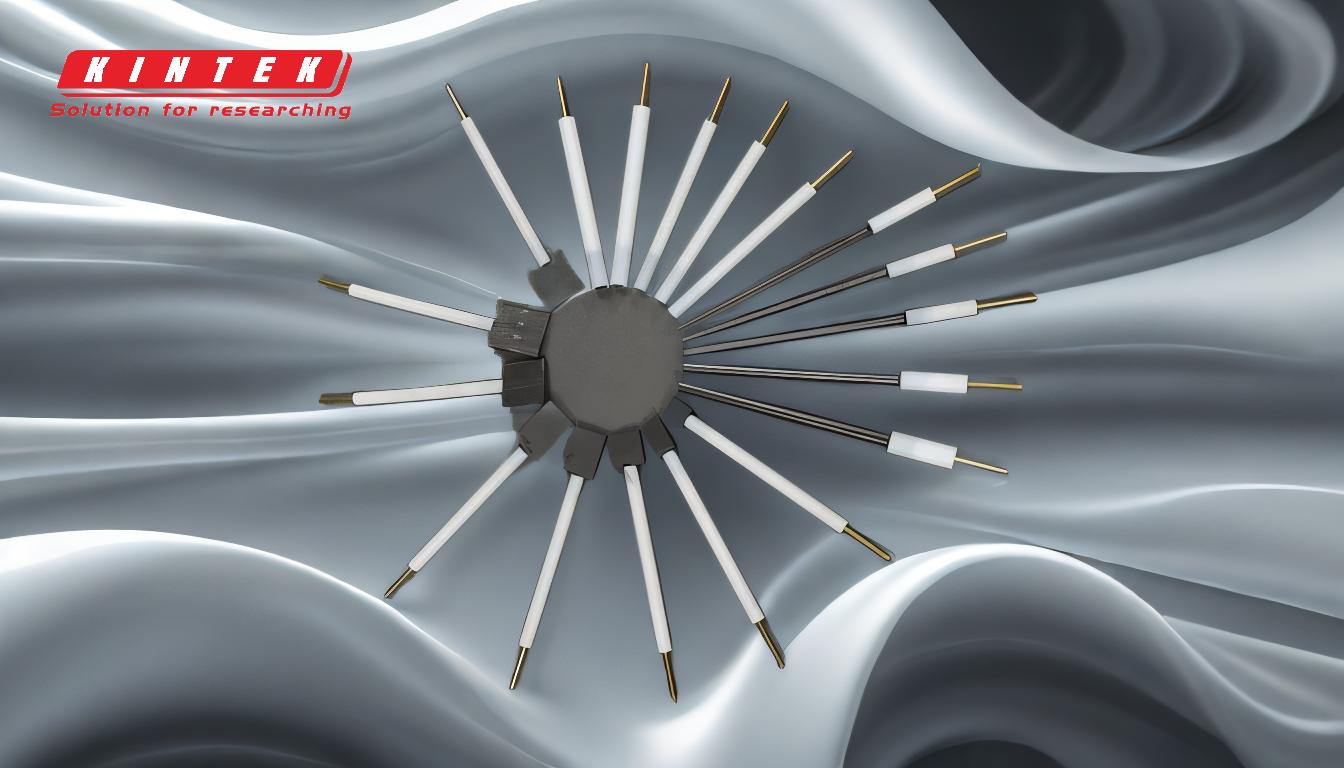
-
Rapid Vapor Deposition Rates:
- E-beam evaporation offers deposition rates ranging from 0.1 μm/min to 100 μm/min, making it one of the fastest thin-film deposition methods available. This high speed is particularly beneficial for large-scale industrial applications where time efficiency is critical.
-
High-Density Coatings with Excellent Adhesion:
- The process produces coatings with high density and strong adhesion to the substrate. This is due to the high-energy electron beam, which ensures that the vaporized material bonds effectively with the substrate, resulting in durable and long-lasting coatings.
-
High-Purity Films:
- The vacuum environment minimizes contamination risks, leading to the deposition of high-purity films. This is crucial for applications in semiconductor manufacturing and optics, where even minor impurities can significantly affect performance.
-
Multi-Layer Deposition Capability:
- E-beam evaporation allows for the deposition of multiple layers without the need to vent the vacuum chamber. This capability is essential for creating complex, multi-layered structures used in advanced optical coatings and electronic devices.
-
Compatibility with a Wide Variety of Materials:
- The technique is compatible with a broad range of materials, including metals, ceramics, and semiconductors. This versatility makes it a preferred choice for diverse applications across various industries.
-
High Material Utilization Efficiency:
- E-beam evaporation is highly efficient in terms of material usage, with minimal waste. This efficiency is particularly important when working with expensive or rare materials.
-
System Components:
- The e-beam evaporation system consists of a vacuum chamber, an electron beam source, and a crucible. The electron beam source, typically made from tungsten, is heated to over 2,000 degrees Celsius to generate electrons. Magnets focus these electrons into a beam directed at the crucible, which holds the source material. The crucible is water-cooled to prevent melting and contamination of the source material.
-
Limitations:
- Despite its advantages, e-beam evaporation has some limitations. It is a line-of-sight deposition method, making it unsuitable for coating the inner surfaces of complex geometries. Additionally, secondary electron emission and X-ray production can cause energy loss, and filament degradation can lead to inconsistent evaporation rates.
In summary, e-beam evaporation is a powerful and versatile deposition technique with numerous advantages, including rapid deposition rates, high-purity films, and compatibility with a wide range of materials. However, its limitations, such as the inability to coat complex geometries and potential energy loss, must be considered when selecting this method for specific applications.
Summary Table:
Key Feature | Description |
---|---|
Rapid Deposition Rates | 0.1 μm/min to 100 μm/min, ideal for large-scale industrial applications. |
High-Density Coatings | Strong adhesion and durable coatings due to high-energy electron beams. |
High-Purity Films | Minimal contamination in vacuum environments, crucial for semiconductors. |
Multi-Layer Deposition | Enables complex, multi-layered structures without venting the vacuum chamber. |
Wide Material Compatibility | Works with metals, ceramics, and semiconductors for diverse applications. |
High Material Utilization | Efficient material usage with minimal waste, ideal for expensive materials. |
Limitations | Line-of-sight method, unsuitable for complex geometries; potential energy loss. |
Interested in leveraging e-beam evaporation for your projects? Contact our experts today to learn more!