Hydrogen plays a critical role in various furnace applications, particularly in heat treatment, sintering, and annealing processes. Its high thermal conductivity and reducing properties make it an ideal atmosphere for achieving specific material properties, such as oxide reduction, impurity removal, and enhanced sintering performance. Hydrogen is used in furnaces for processes like ceramic sintering, metallization, brazing, and semiconductor alloy processing. However, its use comes with challenges, including safety concerns due to its explosive nature and the brittleness of furnace components in reducing atmospheres. Despite these challenges, hydrogen's ability to create high-purity environments and improve material quality makes it indispensable in advanced manufacturing and material processing.
Key Points Explained:
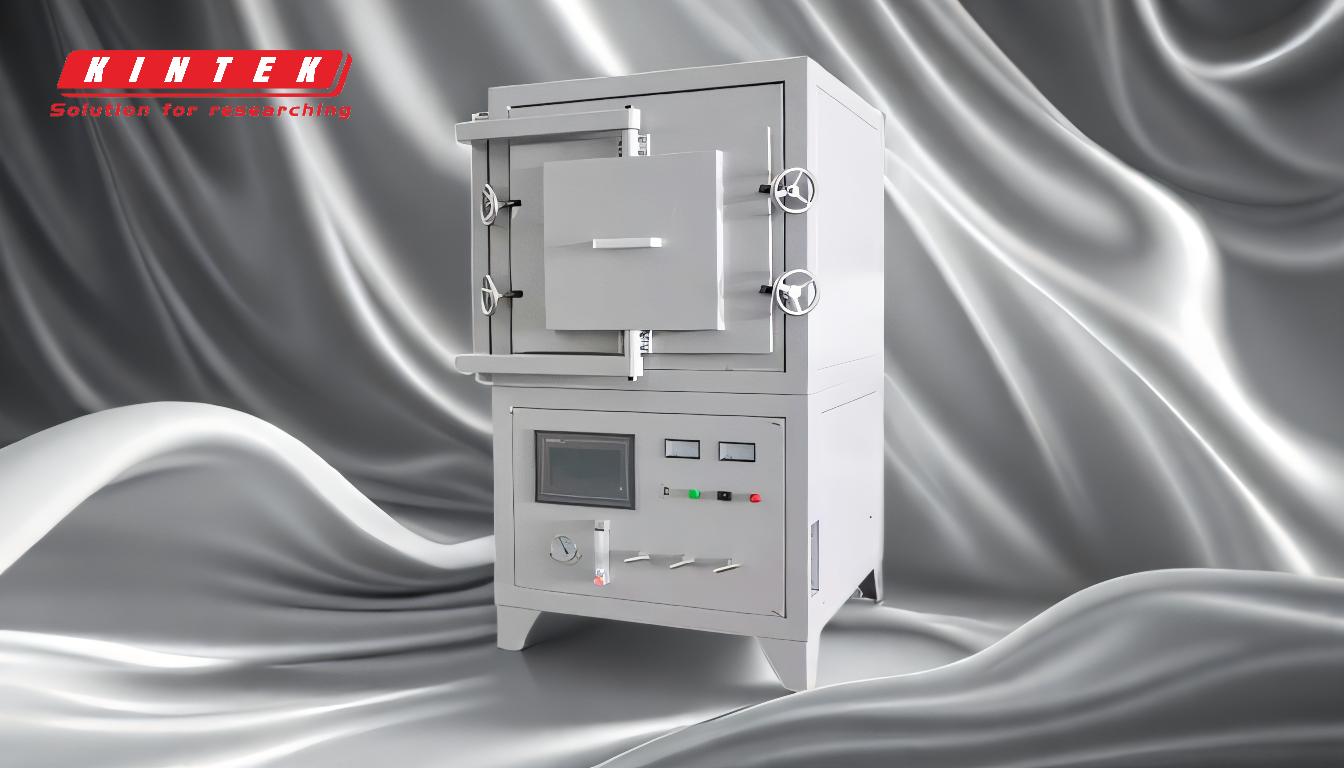
-
Primary Uses of Hydrogen in Furnaces:
- Sintering and Annealing: Hydrogen is widely used in sintering and annealing processes for materials like ceramics, metals, and semiconductors. It helps achieve high-purity environments, which are essential for producing high-quality materials.
- Oxide Reduction: Hydrogen reduces surface oxides and removes impurities such as silica from alloys, particularly in stainless steel. This is crucial for improving material properties and performance.
- Heat Treatment: Hydrogen's high thermal conductivity allows for rapid heating and cooling of metals, which is beneficial for heat treatment processes.
-
Advantages of Using Hydrogen:
- High Purity Atmosphere: Hydrogen provides a high-purity environment (>99.9995%), which is suitable for a wide range of materials and processes.
- Improved Material Quality: By reducing oxides and impurities, hydrogen enhances the quality of the final product, leading to better mechanical and thermal properties.
- Enhanced Furnace Performance: Hydrogen lowers the dew point in the furnace atmosphere, creating better reducing conditions and improving overall furnace performance.
-
Specific Applications:
- Ceramic Sintering: Hydrogen is used in ceramic sintering to achieve dense and high-strength ceramic components.
- Metallization and Brazing: It facilitates the metallization and brazing of metal parts, ensuring strong and durable bonds.
- Semiconductor Processing: Hydrogen is essential in semiconductor alloy processing, where high-purity environments are required to produce defect-free materials.
- Powder Metallurgy: It is used in sintering powder metallurgy to produce complex and high-performance metal parts.
-
Working Principle of Hydrogen Atmosphere Furnaces:
- Heating Medium: Hydrogen serves as the heating medium in hydrogen atmosphere furnaces, allowing materials to be heated to high temperatures in a controlled environment.
- Controlled Atmosphere: The furnace is designed to operate in a hydrogen or inert gas environment, ensuring that materials are processed without contamination.
-
Challenges and Considerations:
- Safety Concerns: Hydrogen is highly flammable and poses a risk of explosion, requiring strict safety measures and handling protocols.
- Material Brittleness: Components in hydrogen furnaces, such as resistors, can become brittle and have a shorter lifespan due to the reducing atmosphere.
- Hydrogen Availability: Obtaining hydrogen in sufficient quantities can be challenging, especially for large-scale industrial applications.
-
Specialized Furnaces:
- Hydrogen Reduction Furnace: This furnace is used for processing semiconductor materials, nanomaterials, and various powders under hydrogen protection. It allows for precise control over temperature and gas flow, ensuring optimal material properties.
- Hydrogen Sintering Furnace: Specifically designed for sintering, annealing, and welding of high-temperature materials, this furnace leverages hydrogen's reducing properties to achieve superior material quality.
-
Future Trends and Innovations:
- Advanced Safety Systems: Ongoing research focuses on developing safer hydrogen handling and storage systems to mitigate explosion risks.
- Improved Furnace Materials: Innovations in furnace design and materials aim to address the brittleness issue, extending the lifespan of furnace components.
- Sustainable Hydrogen Production: Efforts are being made to produce hydrogen more sustainably, reducing the environmental impact of its use in industrial processes.
In conclusion, hydrogen is a versatile and essential element in furnace applications, offering significant benefits in terms of material quality and process efficiency. However, its use requires careful consideration of safety and operational challenges to fully leverage its advantages.
Summary Table:
Aspect | Details |
---|---|
Primary Uses | Sintering, annealing, oxide reduction, heat treatment |
Advantages | High-purity atmosphere (>99.9995%), improved material quality, enhanced performance |
Applications | Ceramic sintering, metallization, brazing, semiconductor processing |
Challenges | Safety concerns, material brittleness, hydrogen availability |
Specialized Furnaces | Hydrogen reduction furnace, hydrogen sintering furnace |
Future Trends | Advanced safety systems, improved furnace materials, sustainable production |
Discover how hydrogen can optimize your furnace processes—contact our experts today!