The vapor condensation method for the production of nanoparticles is a widely used technique in nanotechnology. It involves the evaporation of a solid material in a high-temperature environment, followed by rapid cooling (condensation) of the vapor to form nanoparticles. This process is typically carried out in a vacuum or inert gas atmosphere to prevent contamination and oxidation. The method is highly versatile, allowing for the production of a wide range of nanoparticles, including metals, oxides, and semiconductors. The size, shape, and composition of the nanoparticles can be controlled by adjusting parameters such as temperature, pressure, and the rate of cooling. This technique is particularly valued for its ability to produce high-purity nanoparticles with uniform size distribution.
Key Points Explained:
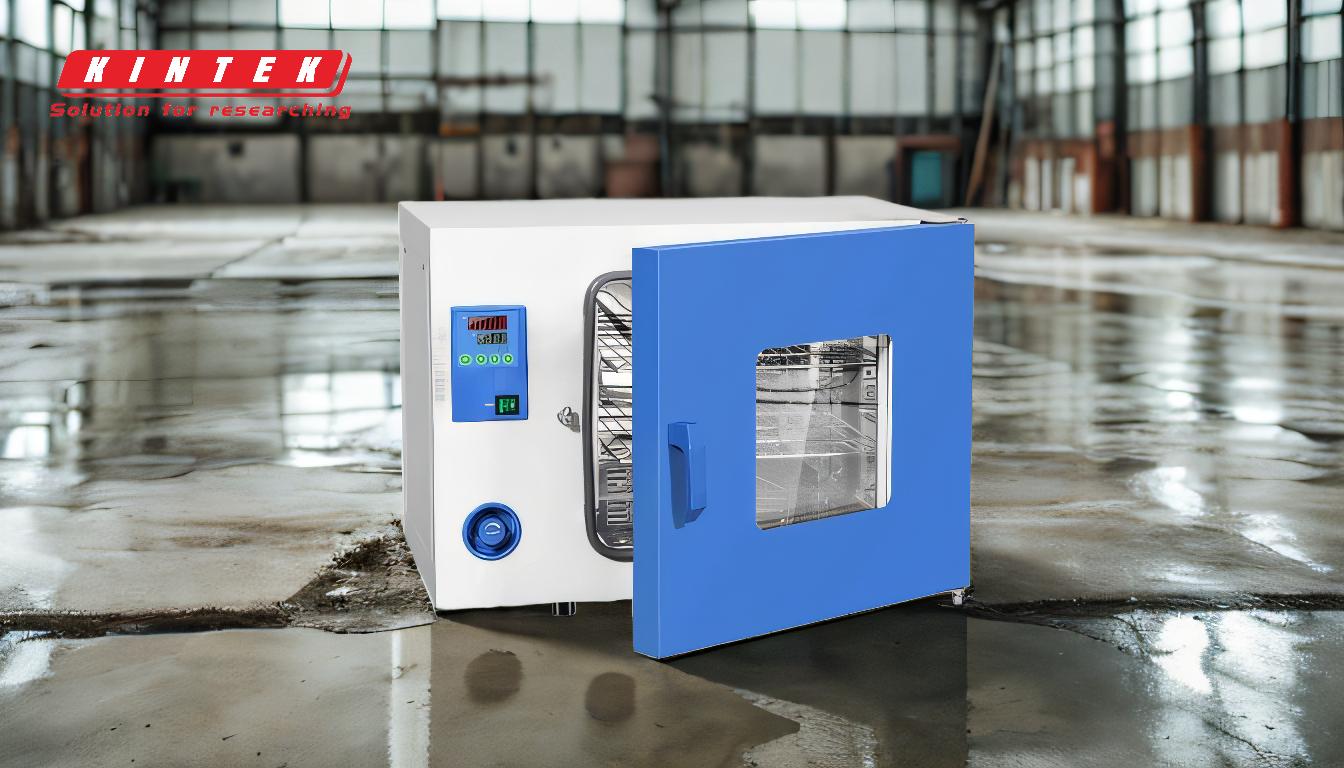
-
Basic Principle of Vapor Condensation Method:
- The vapor condensation method involves the transformation of a solid material into vapor at high temperatures, followed by rapid cooling to condense the vapor into nanoparticles.
- This process is typically conducted in a vacuum or inert gas environment to ensure the purity and quality of the nanoparticles.
-
Steps Involved in the Process:
- Evaporation: The solid material is heated to a high temperature until it evaporates. This can be achieved using various heating methods, such as resistive heating, laser ablation, or arc discharge.
- Condensation: The vapor is then rapidly cooled, often using a cold gas or liquid, causing it to condense into nanoparticles. The rapid cooling is crucial for controlling the size and morphology of the nanoparticles.
- Collection: The nanoparticles are collected on a substrate or in a liquid medium for further processing or analysis.
-
Control of Nanoparticle Properties:
- Size Control: The size of the nanoparticles can be controlled by adjusting the rate of cooling and the concentration of the vapor. Faster cooling rates generally result in smaller nanoparticles.
- Shape Control: The shape of the nanoparticles can be influenced by the type of substrate used for collection and the cooling environment.
- Composition Control: By using different materials or mixtures, nanoparticles with various compositions can be produced. This allows for the creation of composite or alloy nanoparticles.
-
Advantages of the Vapor Condensation Method:
- High Purity: The use of a vacuum or inert gas environment minimizes contamination, resulting in high-purity nanoparticles.
- Uniform Size Distribution: The method allows for the production of nanoparticles with a narrow size distribution, which is important for many applications.
- Versatility: The technique can be used to produce a wide range of nanoparticles, including metals, oxides, and semiconductors.
-
Applications of Nanoparticles Produced by Vapor Condensation:
- Catalysis: Nanoparticles are widely used as catalysts in chemical reactions due to their high surface area and reactivity.
- Electronics: Nanoparticles are used in the fabrication of electronic devices, such as transistors and sensors, due to their unique electrical properties.
- Medicine: Nanoparticles are used in drug delivery systems, imaging, and diagnostics due to their ability to interact with biological systems at the molecular level.
-
Challenges and Limitations:
- Energy Consumption: The process requires high temperatures, which can be energy-intensive.
- Scalability: While the method is effective for laboratory-scale production, scaling up to industrial levels can be challenging.
- Cost: The equipment and materials required for the vapor condensation method can be expensive, particularly for high-purity applications.
In summary, the vapor condensation method is a powerful technique for the production of nanoparticles with controlled size, shape, and composition. Its ability to produce high-purity nanoparticles with uniform size distribution makes it highly valuable for a wide range of applications in catalysis, electronics, and medicine. However, challenges related to energy consumption, scalability, and cost must be addressed to fully realize its potential in industrial applications.
Summary Table:
Aspect | Details |
---|---|
Basic Principle | Evaporation of solid material followed by rapid cooling to form nanoparticles. |
Environment | Conducted in vacuum or inert gas to prevent contamination. |
Key Steps | Evaporation → Condensation → Collection. |
Control Parameters | Temperature, pressure, cooling rate. |
Advantages | High purity, uniform size distribution, versatility. |
Applications | Catalysis, electronics, medicine. |
Challenges | Energy consumption, scalability, cost. |
Interested in learning more about nanoparticle production? Contact our experts today for tailored solutions!