A pyrolysis machine operates by thermally decomposing organic materials like biomass, plastics, or tires in the absence of oxygen. The process involves several stages: material preparation (crushing and drying), pyrolysis (heating to 400-900°C), and the generation of byproducts such as syngas, bio-oil, and bio-char. The machine ensures efficient energy use by recycling combustible gas and waste heat. The process is environmentally friendly, as it minimizes emissions and produces reusable byproducts for energy, industrial applications, and soil enrichment.
Key Points Explained:
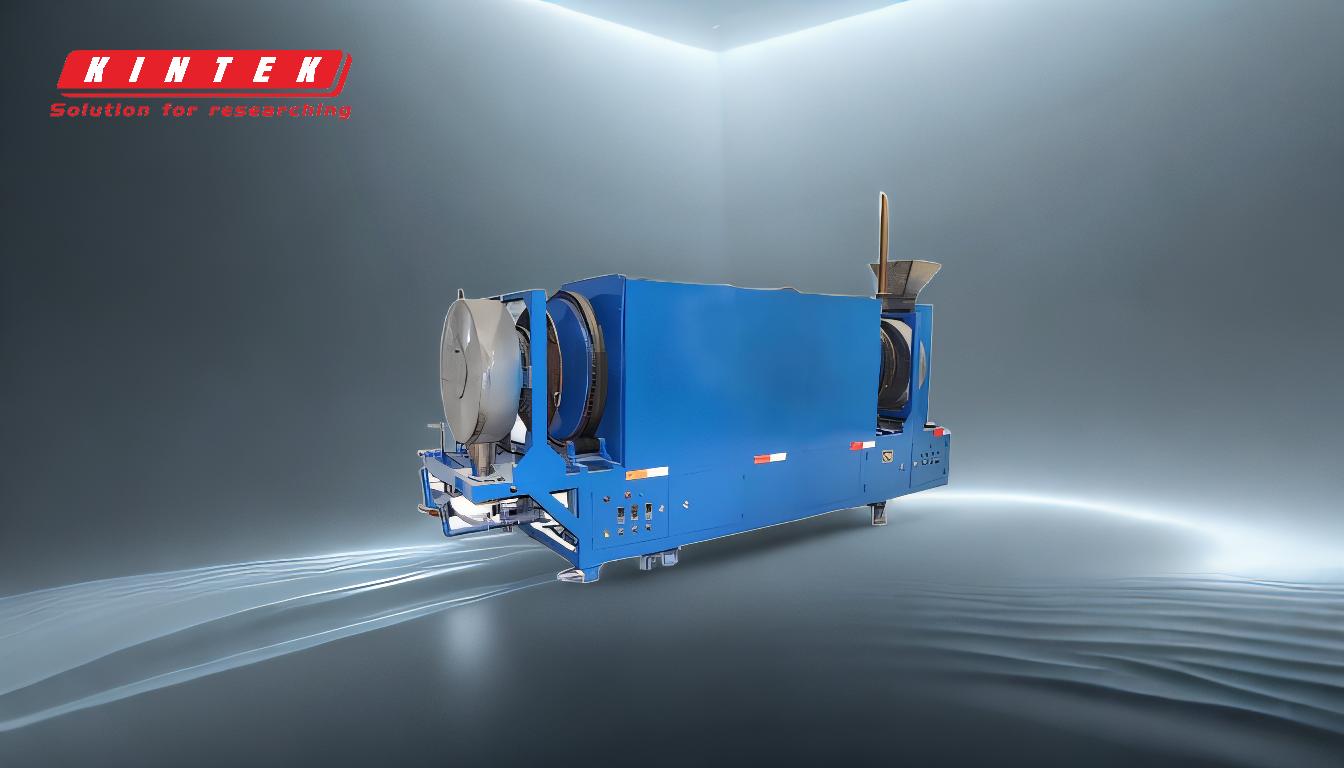
-
Material Preparation:
- Crushing and Drying: The feedstock (e.g., biomass, plastics, or tires) is first crushed to a size ≤ 30mm and dried to reduce moisture content to ≤ 15%. This ensures optimal pyrolysis conditions.
- Preheating: The material is preheated in an inner cylinder to prepare it for the pyrolysis process.
-
Pyrolysis Process:
- Heating in the Absence of Oxygen: The dried material is fed into a reactor and heated to temperatures between 400-900°C in an oxygen-free environment. This prevents combustion and instead causes thermal decomposition.
- Thermal Decomposition: The heat breaks down the larger molecules in the material into smaller components, producing syngas, bio-oil, and bio-char.
-
Byproduct Generation:
- Syngas: A mixture of hydrogen, carbon monoxide, and other gases, syngas can be used as fuel or further processed into biofuels.
- Bio-Oil: A liquid product that can be refined for use in transportation or industrial applications.
- Bio-Char: A solid residue that can be used as a soil amendment to improve soil health or as a sorbent for environmental cleanup.
-
Energy Recycling:
- Combustible Gas: About 20 minutes after feeding, combustible gas is generated. It is cleaned, desulfurized, and dust-removed before being reused to heat the reactor, ensuring energy efficiency.
- Waste Heat Flue Gas: Part of the waste heat from the flue gas is recycled to preheat the dryer, while the remaining flue gas is treated and discharged to minimize environmental impact.
-
Safety and Control Systems:
- The pyrolysis plant includes advanced safety and control systems to ensure efficient and safe operation. These systems monitor temperature, pressure, and gas composition to optimize the process and prevent accidents.
-
Environmental Benefits:
- The pyrolysis process is designed to be environmentally friendly. It reduces waste by converting it into valuable byproducts and minimizes emissions through gas cleaning and waste heat recycling.
By following these steps, a pyrolysis machine efficiently converts waste materials into useful products while minimizing environmental impact and maximizing energy recovery.
Summary Table:
Stage | Details |
---|---|
Material Preparation | - Crushing: Feedstock ≤ 30mm - Drying: Moisture ≤ 15% - Preheating |
Pyrolysis Process | - Heating: 400-900°C in oxygen-free environment - Thermal Decomposition |
Byproduct Generation | - Syngas: Fuel or biofuel - Bio-Oil: Industrial use - Bio-Char: Soil amendment |
Energy Recycling | - Combustible gas reused for heating - Waste heat recycled for drying |
Environmental Benefits | - Minimizes emissions - Converts waste into reusable byproducts |
Discover how a pyrolysis machine can transform your waste into valuable resources—contact us today!