Thermal evaporation is a widely used physical vapor deposition (PVD) technique for thin-film deposition. It involves heating a solid material in a high vacuum chamber until it evaporates, creating a vapor cloud. The vaporized material travels through the vacuum and condenses onto a substrate, forming a thin film. This process relies on thermal energy, typically provided by a resistive heating element or an electron beam, to achieve the necessary vapor pressure. The vacuum environment ensures minimal contamination and allows the vapor to travel unimpeded, resulting in a uniform and high-quality coating. Thermal evaporation is particularly useful for applications like OLEDs and thin-film transistors due to its simplicity and effectiveness.
Key Points Explained:
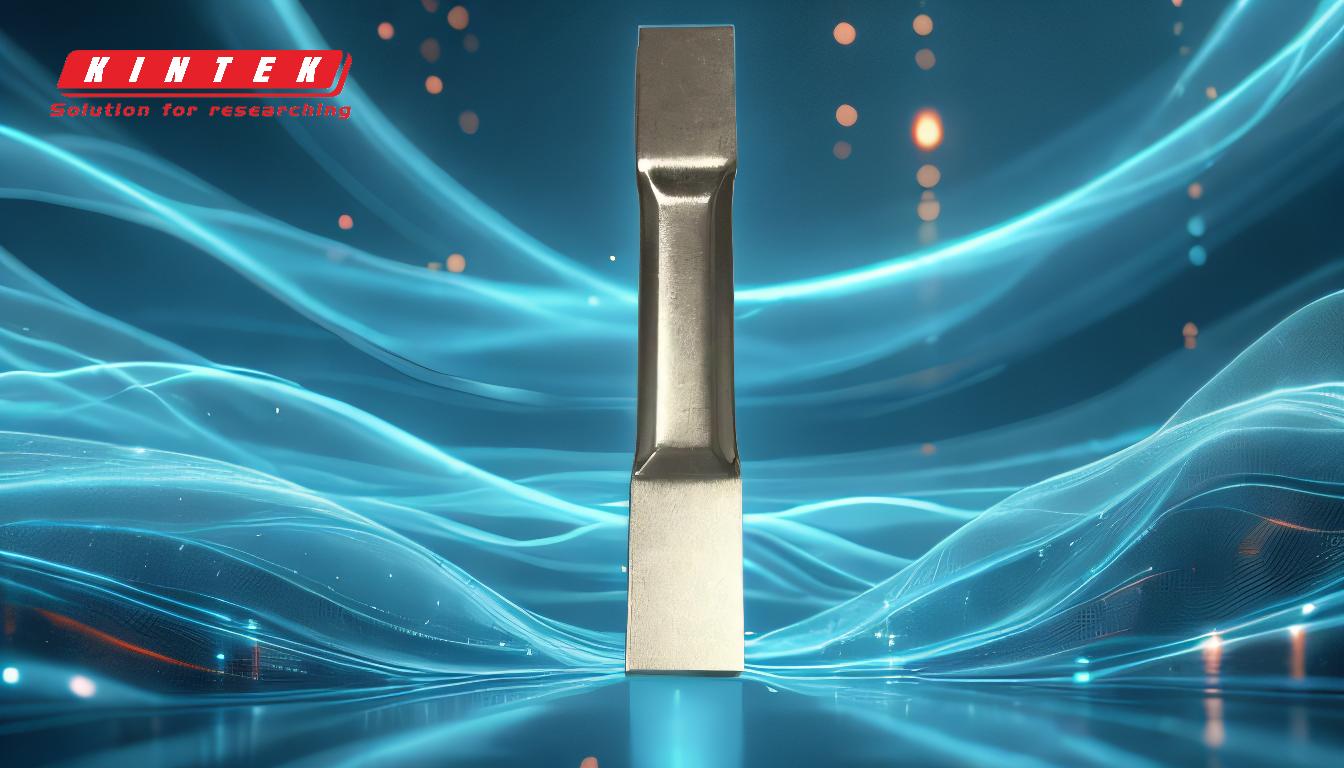
-
Definition and Purpose:
- Thermal evaporation is a physical vapor deposition (PVD) method used to deposit thin films on substrates.
- It is commonly employed in industries requiring precise and uniform coatings, such as electronics, optics, and semiconductors.
-
Process Overview:
- A solid material (target) is placed in a high vacuum chamber.
- The material is heated using thermal energy, typically from a resistive heating element (e.g., tungsten) or an electron beam.
- The heat causes the material to reach a temperature where it evaporates, creating a vapor cloud.
-
Role of Vacuum Environment:
- The high vacuum environment is crucial for the process:
- It minimizes contamination from air or other gases.
- It allows the vaporized material to travel without scattering or reacting with other atoms.
- Even a low vapor pressure is sufficient in a vacuum to create a vapor stream.
- The high vacuum environment is crucial for the process:
-
Deposition Mechanism:
- The vaporized material forms a stream that traverses the vacuum chamber.
- Upon reaching the substrate, the vapor condenses and adheres to the surface, forming a thin film.
- The vacuum ensures uniform deposition and high film quality.
-
Heat Sources:
- Resistive Heating: A tungsten heating element is commonly used to melt and evaporate the target material.
- Electron Beam Evaporation: An electron beam is directed at the target material, providing localized heating and evaporation.
- Both methods are effective, with the choice depending on the material properties and application requirements.
-
Advantages of Thermal Evaporation:
- Simplicity: The process is straightforward and easy to implement.
- High Purity: The vacuum environment ensures minimal contamination.
- Versatility: Suitable for a wide range of materials, including metals, semiconductors, and organic compounds.
- Uniformity: Produces consistent and high-quality thin films.
-
Applications:
- OLEDs (Organic Light-Emitting Diodes): Used to deposit organic layers in display technology.
- Thin-Film Transistors: Essential for creating electronic components in devices like smartphones and tablets.
- Optical Coatings: Used in lenses, mirrors, and other optical components to enhance performance.
- Semiconductors: Critical for depositing conductive and insulating layers in microelectronics.
-
Challenges and Considerations:
- Material Compatibility: Not all materials can withstand the high temperatures required for evaporation.
- Film Thickness Control: Precise control is needed to achieve the desired film properties.
- Equipment Cost: High vacuum systems and heating elements can be expensive.
- Scalability: While effective for small-scale applications, scaling up for mass production can be challenging.
-
Comparison with Other Deposition Methods:
- Sputtering: Uses energetic ions to dislodge atoms from a target, offering better adhesion and uniformity for some materials.
- Chemical Vapor Deposition (CVD): Involves chemical reactions to deposit films, suitable for complex materials but requires higher temperatures and more complex equipment.
- Thermal evaporation is often preferred for its simplicity and effectiveness in specific applications.
-
Future Trends:
- Improved Heating Techniques: Advances in electron beam and laser heating could enhance precision and efficiency.
- Hybrid Methods: Combining thermal evaporation with other techniques (e.g., sputtering) to achieve superior film properties.
- Automation and Control: Integration of advanced sensors and AI for real-time monitoring and optimization of the deposition process.
In summary, thermal evaporation is a fundamental and versatile thin-film deposition technique. Its reliance on thermal energy and vacuum environments ensures high-quality, uniform coatings, making it indispensable in modern technology and manufacturing.
Summary Table:
Aspect | Details |
---|---|
Definition | A PVD technique for depositing thin films using thermal energy. |
Process | Heating a solid material in a vacuum to create a vapor that condenses. |
Heat Sources | Resistive heating or electron beam evaporation. |
Advantages | High purity, simplicity, versatility, and uniform film quality. |
Applications | OLEDs, thin-film transistors, optical coatings, and semiconductors. |
Challenges | Material compatibility, film thickness control, and equipment cost. |
Future Trends | Improved heating techniques, hybrid methods, and automation. |
Discover how thermal evaporation can enhance your thin-film processes—contact us today for expert guidance!