Twin-screw granulation is a modern, continuous manufacturing process used primarily in the pharmaceutical industry for moist granulation. It involves the use of two intermeshing screws within a barrel to mix, granulate, and densify powder materials into granules. This method has gained prominence since the early 2000s due to its efficiency, scalability, and ability to produce consistent, high-quality granules. It is particularly advantageous for companies transitioning to continuous manufacturing, as it offers precise control over process parameters and reduces material waste. Twin-screw granulation is a key technology in the advancement of pharmaceutical production, enabling faster and more flexible manufacturing processes.
Key Points Explained:
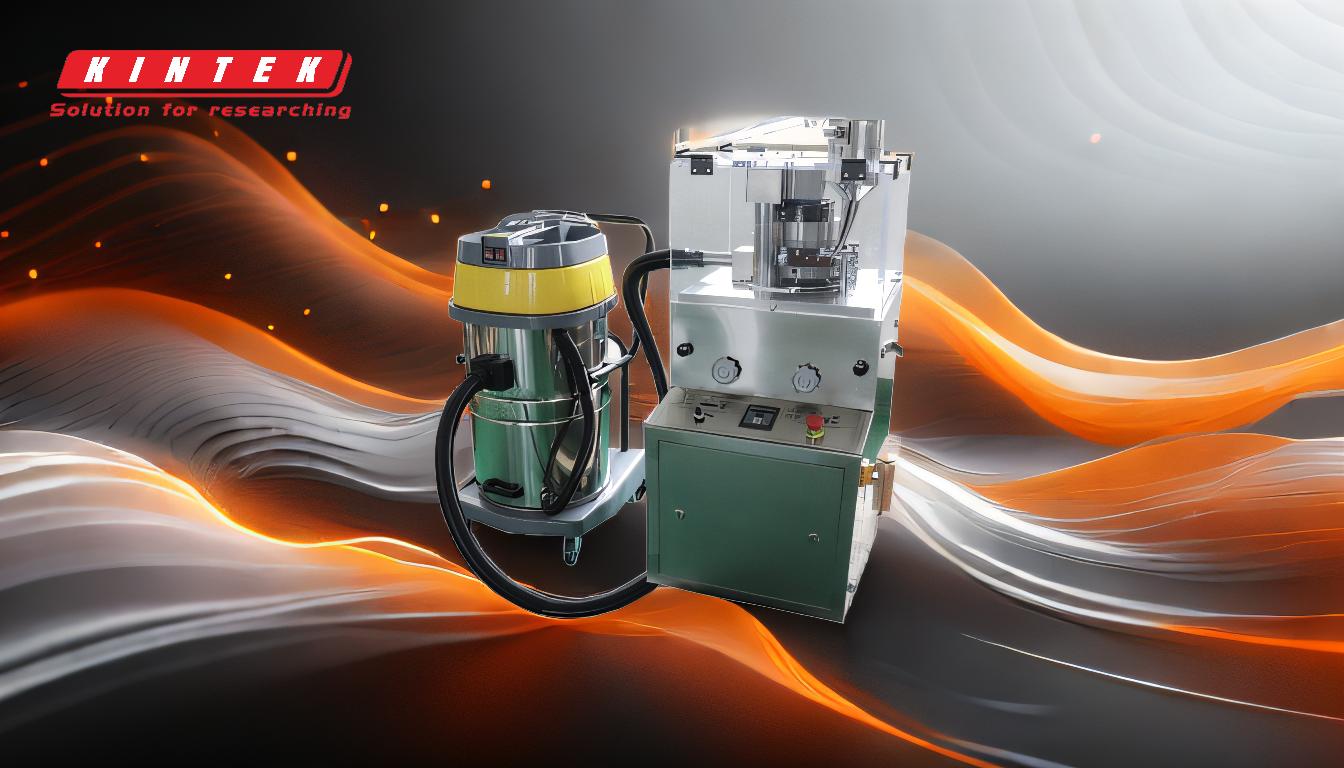
-
Definition and Purpose of Twin-Screw Granulation:
- Twin-screw granulation is a continuous process used for moist granulation, where powder materials are mixed, wetted, and densified into granules.
- It is particularly significant in pharmaceutical manufacturing, where consistent granule quality is critical for downstream processes like tableting or capsule filling.
-
Historical Context:
- Twin-screw granulation emerged as a prominent method in the early 2000s.
- It was developed to address the limitations of traditional batch granulation methods, such as variability in product quality and inefficiencies in scaling up production.
-
Key Components of the Process:
- Twin-Screw Extruder: The core equipment consists of two intermeshing screws rotating within a barrel. The screws convey, mix, and compress the material.
- Liquid Addition System: A controlled system for adding binder or solvent to the powder blend to facilitate granule formation.
- Barrel Design: The barrel is divided into zones with specific functions, such as feeding, mixing, granulating, and densifying.
-
Advantages of Twin-Screw Granulation:
- Continuous Processing: Unlike batch methods, twin-screw granulation operates continuously, reducing downtime and improving efficiency.
- Scalability: The process is easily scalable from lab to production scale, making it suitable for both R&D and commercial manufacturing.
- Consistency and Control: Precise control over process parameters (e.g., screw speed, liquid addition rate) ensures uniform granule size and density.
- Reduced Material Waste: Continuous operation minimizes material loss and improves yield.
-
Applications in Pharmaceutical Manufacturing:
- Twin-screw granulation is widely used for producing granules for tablets, capsules, and other solid dosage forms.
- It supports the development of continuous manufacturing lines, which are increasingly adopted by pharmaceutical companies to enhance productivity and regulatory compliance.
-
Challenges and Considerations:
- Equipment Design: Proper selection of screw configuration and barrel zones is critical to achieving desired granule properties.
- Process Optimization: Parameters such as feed rate, screw speed, and liquid-to-solid ratio must be optimized for each formulation.
- Regulatory Compliance: Continuous manufacturing processes require robust validation and control strategies to meet regulatory standards.
-
Future Trends:
- Twin-screw granulation is expected to play a pivotal role in the shift toward continuous manufacturing in the pharmaceutical industry.
- Advances in process analytical technology (PAT) and real-time monitoring are likely to further enhance the efficiency and reliability of this method.
By understanding these key points, equipment and consumable purchasers can make informed decisions about adopting twin-screw granulation technology for their manufacturing processes.
Summary Table:
Key Aspect | Details |
---|---|
Definition | Continuous moist granulation process using twin-screw extruders. |
Purpose | Produces consistent, high-quality granules for pharmaceutical applications. |
Advantages | Continuous processing, scalability, precise control, reduced material waste. |
Applications | Tablets, capsules, and solid dosage forms in pharmaceutical manufacturing. |
Challenges | Equipment design, process optimization, and regulatory compliance. |
Future Trends | Role in continuous manufacturing and advancements in real-time monitoring. |
Ready to enhance your pharmaceutical manufacturing process? Contact us today to learn more about twin-screw granulation!