Vacuum brazing is a specialized joining process that involves heating metal components in a vacuum environment to create strong, clean, and oxidation-free joints. This method is particularly advantageous for materials that are sensitive to oxidation or require high-purity joints. The process utilizes a vacuum brazing furnace, which consists of a vacuum system and a heating system to achieve the necessary conditions for brazing. The vacuum environment eliminates the need for flux, prevents oxidation, and ensures a high-quality joint. The process is automated and controlled by temperature instruments, making it efficient and precise.
Key Points Explained:
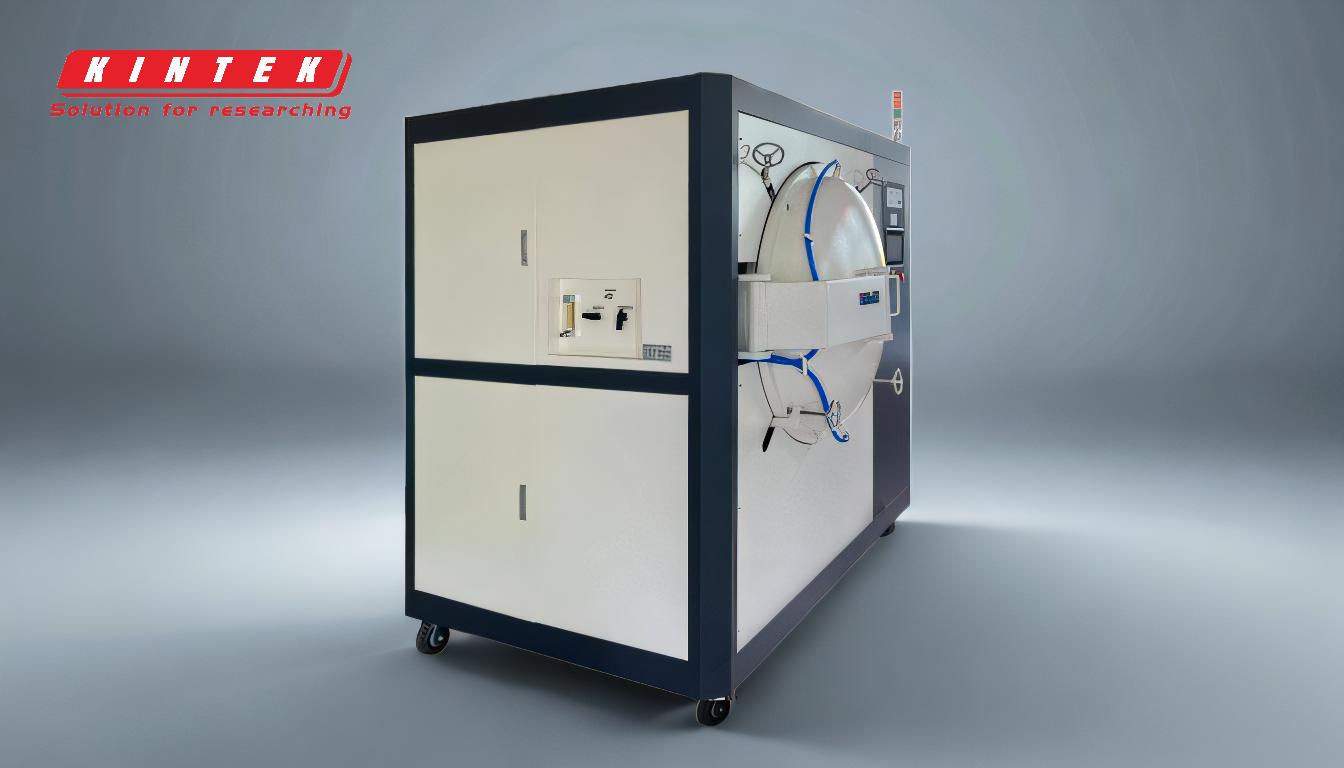
-
What is Vacuum Brazing?
- Vacuum brazing is a process that joins two or more metal components by heating them just below their melting points and using a filler metal to create a joint. The filler metal melts and flows into the joint by capillary action, forming a strong bond upon cooling.
- The process is performed in a vacuum environment to prevent oxidation and contamination, which is especially important for materials like titanium, stainless steel, and other high-performance alloys.
-
Role of the Vacuum Brazing Furnace:
- A vacuum brazing furnace is the core equipment used in this process. It consists of two main systems: the vacuum system and the heating system.
- The vacuum system creates and maintains the required vacuum level, typically using components like mechanical pumps, diffusion pumps, and Roots pumps. The highest achievable vacuum degree is generally around 7 × 10^-3 Pa.
- The heating system heats the workpiece to the brazing temperature, which is carefully controlled to ensure the filler metal melts and flows properly without damaging the base materials.
-
Steps in the Vacuum Brazing Process:
- Workpiece Preparation: The metal parts to be joined are cleaned and assembled with the filler metal placed in the joint area.
- Loading into the Furnace: The assembled workpiece is placed inside the vacuum chamber of the furnace.
- Vacuum Creation: The vacuum system evacuates air from the chamber to achieve the desired vacuum level. This step ensures an oxidation-free environment.
- Heating: The furnace heats the workpiece to the brazing temperature, causing the filler metal to melt and flow into the joint.
- Cooling: After brazing, the workpiece is cooled in the vacuum environment to a safe temperature to prevent oxidation upon exposure to air.
- Unloading: Once cooled, the workpiece is removed from the furnace, and the joint is inspected for quality.
-
Advantages of Vacuum Brazing:
- Oxidation-Free Joints: The vacuum environment eliminates the need for flux and prevents oxidation, resulting in clean and high-quality joints.
- Precision and Control: Automated temperature control ensures precise heating and cooling, reducing the risk of defects.
- Versatility: Vacuum brazing can join a wide range of materials, including those that are difficult to weld or braze in other environments.
- Minimal Post-Processing: The absence of flux and oxidation reduces the need for cleaning and finishing after brazing.
-
Applications of Vacuum Brazing:
- Vacuum brazing is widely used in industries such as aerospace, automotive, electronics, and medical devices, where high-strength, oxidation-free joints are critical.
- It is particularly suitable for joining complex assemblies with multiple joints, as the process can simultaneously create thousands of joints in a single cycle.
-
Comparison with Other Brazing Methods:
- Unlike furnace brazing, which relies on a controlled atmosphere, vacuum brazing eliminates the need for any external gas or flux, making it cleaner and more efficient.
- Compared to hydrogen brazing, vacuum brazing is safer and more versatile, as it does not require the use of flammable gases like hydrogen.
-
Key Considerations for Equipment Purchasers:
- When selecting a vacuum brazing furnace, consider factors such as the maximum achievable vacuum level, temperature range, chamber size, and automation capabilities.
- Ensure the furnace has reliable vacuum pumps and temperature control systems to maintain consistent performance.
- Look for furnaces with features like quick cooling systems and adjustable vacuum levels to enhance productivity and flexibility.
In summary, vacuum brazing is a highly effective joining process that leverages the capabilities of a vacuum brazing furnace to create strong, clean, and oxidation-free joints. Its advantages in precision, versatility, and minimal post-processing make it a preferred choice for high-performance applications across various industries.
Summary Table:
Key Aspect | Details |
---|---|
Process | Joins metal components using a filler metal in a vacuum environment. |
Environment | Vacuum prevents oxidation and contamination, ensuring high-quality joints. |
Equipment | Uses a vacuum brazing furnace with vacuum and heating systems. |
Advantages | Oxidation-free joints, precise temperature control, minimal post-processing. |
Applications | Aerospace, automotive, electronics, medical devices, and more. |
Comparison | Cleaner and safer than hydrogen brazing; no flux or external gas required. |
Ready to enhance your joining process with vacuum brazing? Contact us today to learn more!