Vacuum furnace brazing is a high-precision metal-joining process conducted in a vacuum environment to create strong, clean, and durable joints without oxidation or contamination. This method is ideal for complex assemblies and sensitive materials, offering precise temperature control and eliminating the need for flux. The process involves heating components to the melting point of a filler metal, which flows into the joint through capillary action, followed by controlled cooling to minimize stress and distortion. Post-brazing treatments may be applied to achieve desired properties. Vacuum furnace brazing is widely used in industries requiring high-quality, leak-tight joints, such as aerospace, automotive, and electronics.
Key Points Explained:
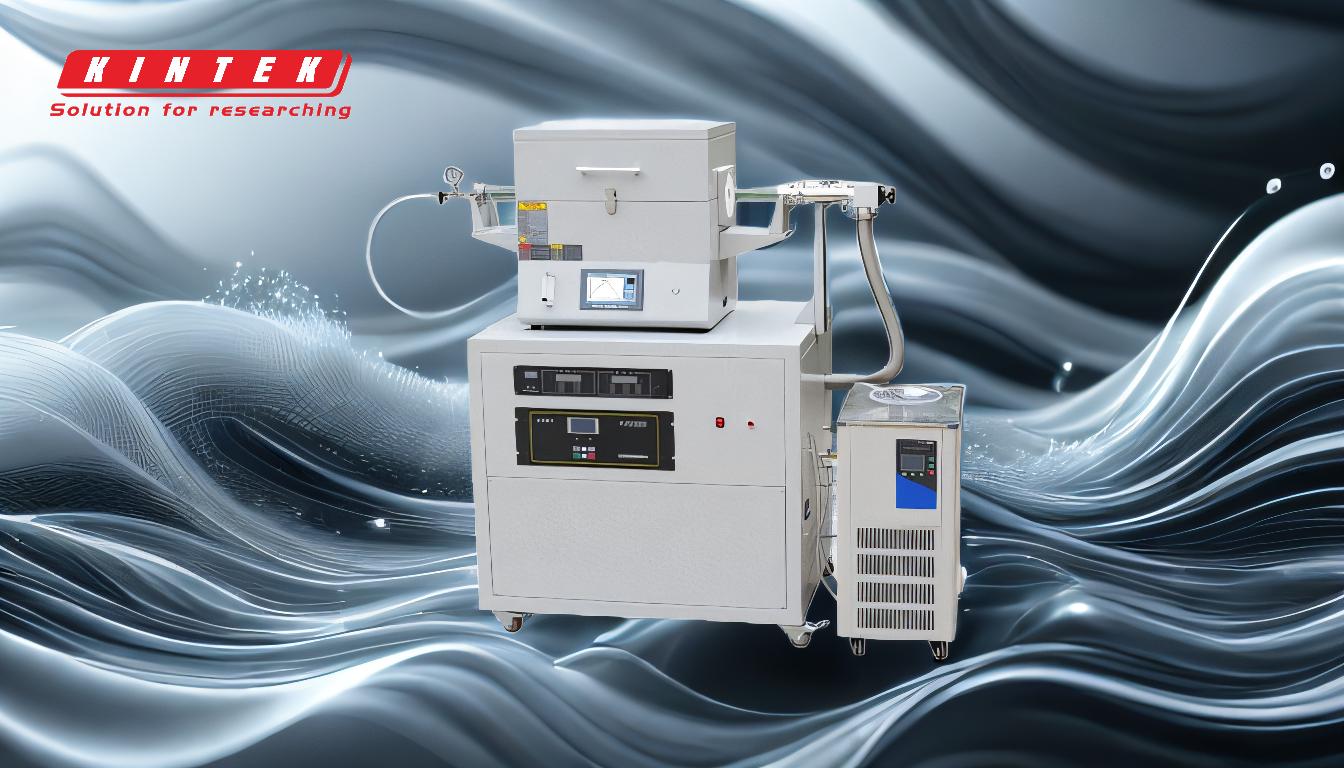
-
Definition and Process of Vacuum Furnace Brazing:
- Vacuum furnace brazing is a metal-joining technique performed in a vacuum furnace, which operates in a low-pressure, oxygen-free environment to prevent oxidation and contamination.
- The process involves heating the components to the melting point of a filler metal, which flows into the joint through capillary action, creating a strong bond.
- After brazing, the furnace is cooled slowly to room temperature to minimize thermal stress and distortion.
-
Advantages of Vacuum Furnace Brazing:
- High-Quality Joints: Produces joints with minimal voids and excellent mechanical properties.
- No Flux Required: Eliminates the risk of contamination from flux residues.
- Oxidation Prevention: The vacuum environment ensures clean, oxidation-free joints.
- Precise Temperature Control: Suitable for joining materials with different melting points.
- Complex Component Compatibility: Ideal for intricate assemblies and sensitive materials.
- Environmentally Friendly: Generates minimal waste and avoids harmful byproducts.
-
Key Components of a Vacuum Furnace:
- Vacuum Chamber: Constructed with high-quality materials to withstand high temperatures and maintain a vacuum seal.
- Heating Elements: Utilize resistance, induction, or radiation heating to generate and control temperatures.
- Cooling System: Uses inert gas to rapidly cool the metal after processing, ensuring controlled cooling rates.
-
Applications and Significance:
- Vacuum furnace brazing is widely used in industries requiring high-quality, leak-tight joints, such as aerospace, automotive, and electronics.
- It is particularly suitable for joining complex components and assemblies that demand precise temperature control and clean, contamination-free joints.
-
Post-Brazing Treatments:
- After cooling, the brazed parts are inspected for quality.
- Additional treatments such as heat treatment, machining, or surface finishing may be performed to achieve the desired properties and appearance.
-
Comparison with Other Brazing Methods:
- Unlike traditional furnace brazing, vacuum furnace brazing eliminates the need for flux and provides a cleaner, more controlled environment.
- It offers superior joint quality and is better suited for sensitive materials and complex geometries.
By leveraging the unique capabilities of a vacuum furnace, vacuum furnace brazing ensures high-quality, durable, and precise metal joints, making it an indispensable process in modern manufacturing.
Summary Table:
Aspect | Details |
---|---|
Definition | High-precision metal-joining process in a vacuum environment. |
Key Advantages | No flux required, oxidation prevention, precise temperature control. |
Applications | Aerospace, automotive, electronics—ideal for complex, leak-tight joints. |
Post-Brazing Treatments | Heat treatment, machining, or surface finishing for desired properties. |
Comparison | Superior to traditional brazing, cleaner, and better for sensitive materials. |
Learn how vacuum furnace brazing can enhance your manufacturing process—contact our experts today!