Vacuum furnace heat treatment is a specialized process that involves heating materials in a controlled, vacuum environment to achieve specific metallurgical properties. This method is widely used in industries requiring high precision and quality, such as aerospace, automotive, and tool manufacturing. The vacuum environment prevents oxidation and contamination, ensuring a pure and defect-free end product. Heating is primarily achieved through radiation, and the spacing of workpieces within the furnace is crucial for uniform heating. The process allows for precise temperature control and can include various treatments like annealing, brazing, and sintering. Additionally, quenching can be performed by rapidly cooling the workpiece in a water tank, ensuring the desired material properties are achieved.
Key Points Explained:
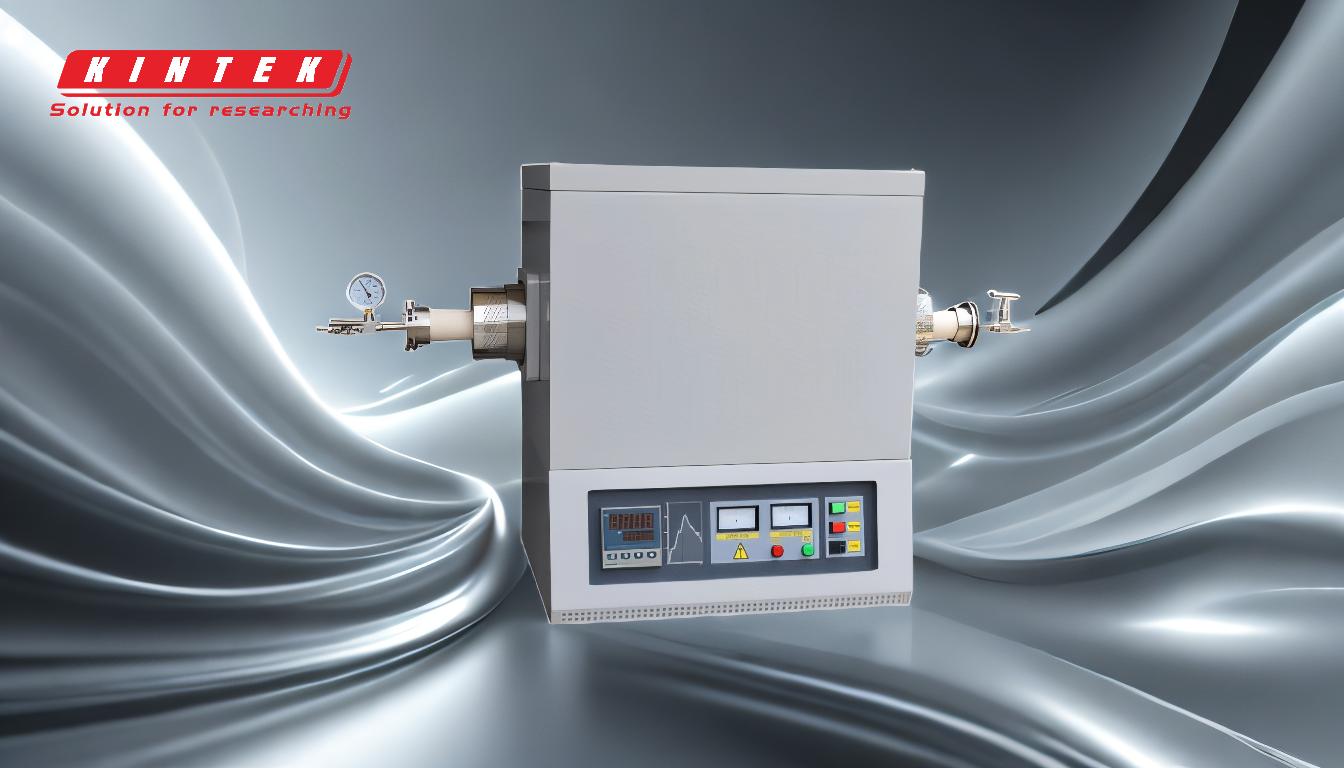
-
Vacuum Environment:
- A vacuum furnace operates by removing air from the chamber, creating a controlled atmosphere. This is particularly beneficial when a specific gaseous medium is required or when atmospheric interference must be avoided.
- The absence of oxygen prevents oxidation, leading to a higher purity end product free from contaminants and defects. This is crucial for applications requiring high precision and quality, such as in the aerospace and automotive industries.
-
Heating Mechanism:
- Heating in a vacuum furnace is primarily achieved through radiation. This method ensures that heat is transferred uniformly to the workpieces.
- The spacing of workpieces within the furnace is important to ensure even heat distribution. Proper spacing prevents hotspots and ensures that all parts of the workpiece are heated uniformly.
-
Hot Zone:
- The hot zone is the core area of the vacuum furnace where the heating elements, often made of molybdenum rods, are located. These elements are resistively heated to temperatures exceeding 1300°C (2372°F) under vacuum conditions.
- The design and materials of the hot zone are critical for maintaining high temperatures and ensuring efficient heat transfer to the workpieces.
-
Quenching Process:
- Quenching is a rapid cooling process used to achieve specific material properties. In a vacuum furnace, quenching can be performed by moving a water tank to just below the furnace hood.
- The furnace door is opened, and the workpiece is lowered into the water tank using a chain mechanism. This rapid cooling process helps in achieving the desired hardness and strength in the material.
-
Benefits of Vacuum Furnace Heat Treatment:
- Prevention of Oxidation: The vacuum environment prevents oxidation, ensuring a clean and defect-free surface.
- Precise Temperature Control: The controlled atmosphere allows for accurate temperature management, ensuring uniform heating and consistent results.
- Versatility: Vacuum furnaces can perform various heat treatment processes, including annealing, brazing, and sintering, without the risk of atmospheric interference.
- High Purity: The absence of contaminants results in a higher purity end product, which is essential for high-performance applications.
For more detailed information on vacuum furnaces, you can visit vacuum furnace.
Summary Table:
Key Aspect | Details |
---|---|
Vacuum Environment | Prevents oxidation and contamination, ensuring high-purity end products. |
Heating Mechanism | Radiation ensures uniform heating; proper spacing of workpieces is crucial. |
Hot Zone | Heating elements (e.g., molybdenum rods) reach temperatures >1300°C. |
Quenching Process | Rapid cooling in water tanks achieves desired material hardness and strength. |
Benefits | Oxidation prevention, precise temperature control, versatility, high purity. |
Learn how vacuum furnace heat treatment can elevate your material processing—contact our experts today for tailored solutions!