Vacuum heat treatment is a specialized process used to harden metals by heating them in a vacuum environment. This method ensures that no air or contaminants interfere with the treatment, resulting in more predictable and superior outcomes. The process involves using a vacuum pump to remove air from a sealed chamber where the heat treatment occurs. Key classifications of vacuum heat treatment include vacuum sintering, vacuum brazing, vacuum quenching, and others, each tailored to specific metal properties and desired outcomes. This technique is particularly beneficial for achieving high-quality, flawless metal joints and surfaces.
Key Points Explained:
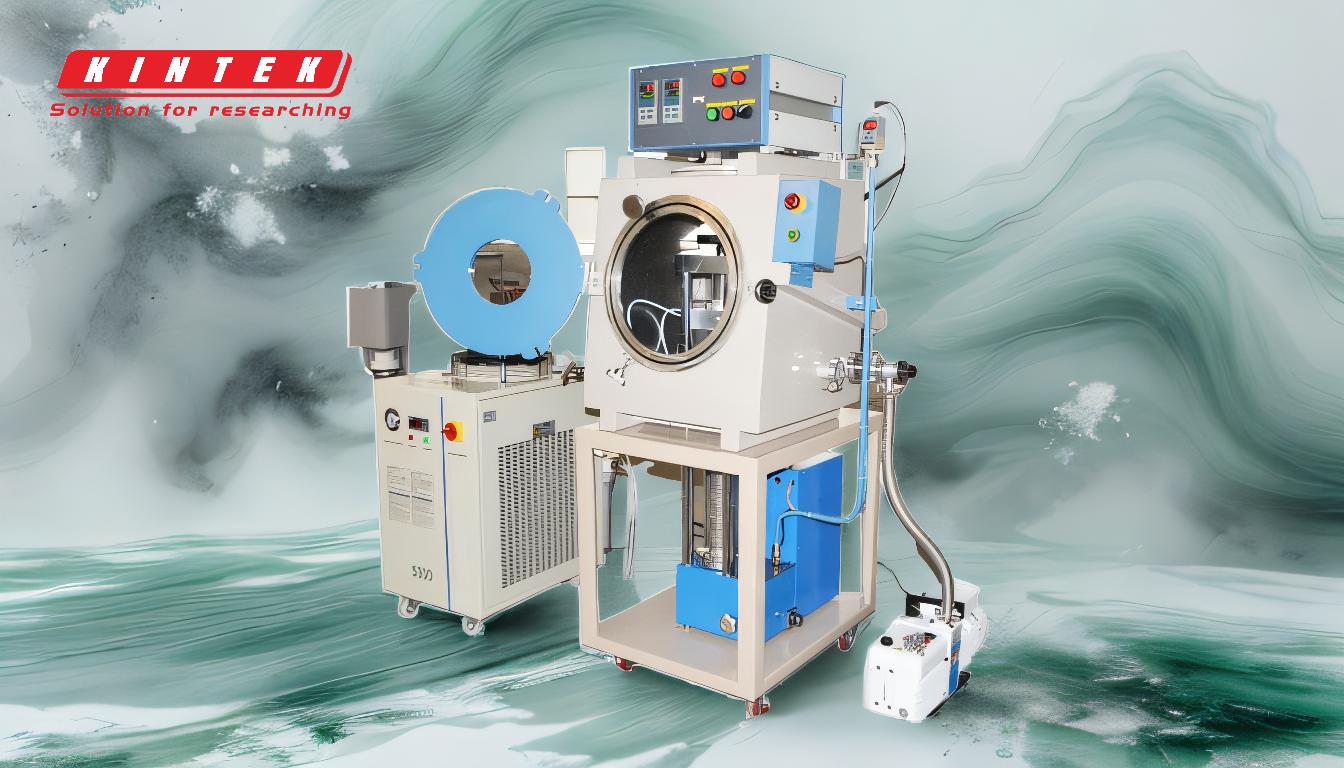
-
Vacuum Environment:
- Definition: A vacuum environment is created by using a vacuum pump to remove air from a sealed chamber. This ensures that the heat treatment process occurs without any atmospheric interference.
- Importance: The absence of air prevents oxidation and contamination, leading to cleaner and more precise results. This is crucial for achieving high-quality metal properties.
-
Process Overview:
- Heating: Metals are heated to specific temperatures just below their melting points. This controlled heating is essential for achieving the desired hardness and structural integrity.
- Cooling: After heating, the metals are cooled at controlled rates. This step is critical for determining the final properties of the metal, such as hardness and toughness.
-
Types of Vacuum Heat Treatment:
- Vacuum Sintering: This process involves heating powdered metals to just below their melting points to form a solid mass. It is commonly used in the production of metal components with complex shapes.
- Vacuum Brazing: This technique connects two metal pieces by heating them and using a filler metal to create a smooth, flawless joint. It is widely used in industries requiring high-strength, leak-tight joints.
- Vacuum Quenching: This process rapidly cools heated metals to achieve high hardness and strength. It is essential for components that require high wear resistance.
- Vacuum Tempering: After quenching, tempering is done to reduce brittleness and improve toughness. This step balances hardness and ductility.
- Vacuum Annealing: This process softens metals by heating them and then slowly cooling them. It is used to improve machinability and reduce internal stresses.
- Vacuum Solution Treatment: This involves heating metals to dissolve alloying elements and then rapidly cooling them to retain a supersaturated solid solution. It is crucial for enhancing the mechanical properties of alloys.
- Vacuum Aging Heat Treatment: This process involves heating metals at lower temperatures for extended periods to precipitate secondary phases. It is used to improve strength and hardness.
- Vacuum Normalizing: This process involves heating metals to a temperature above their critical range and then air cooling them. It is used to refine the grain structure and improve mechanical properties.
- Vacuum Degassing: This process removes dissolved gases from molten metals. It is essential for producing high-quality, defect-free metal castings.
- Magnetic Annealing: This process involves heating magnetic materials in a vacuum to improve their magnetic properties. It is used in the production of high-performance magnetic components.
- Dehydroxylation: This process removes hydroxyl groups from materials. It is used in the production of ceramics and other materials requiring high purity.
-
Advantages of Vacuum Heat Treatment:
- Oxidation Prevention: The vacuum environment prevents oxidation, leading to cleaner and more precise results.
- Contamination Control: The absence of air ensures that no contaminants interfere with the process, resulting in higher quality outcomes.
- Predictable Results: The controlled environment and precise temperature management lead to more predictable and consistent results.
- Enhanced Properties: Vacuum heat treatment can significantly improve the mechanical properties of metals, such as hardness, strength, and toughness.
-
Applications:
- Aerospace: Vacuum heat treatment is used to produce high-strength, lightweight components for aircraft and spacecraft.
- Automotive: This process is essential for manufacturing durable and high-performance automotive parts.
- Medical Devices: Vacuum heat treatment is used to produce biocompatible and high-strength medical implants and instruments.
- Tooling: This process is crucial for producing high-performance cutting tools and dies that require exceptional hardness and wear resistance.
In summary, vacuum heat treatment is a highly specialized and controlled process that offers numerous advantages over traditional heat treatment methods. By eliminating oxidation and contamination, it ensures superior metal properties and predictable results, making it indispensable in various high-tech industries.
Summary Table:
Aspect | Details |
---|---|
Vacuum Environment | Removes air to prevent oxidation and contamination, ensuring precise results. |
Process Overview | Heating metals below melting points, followed by controlled cooling. |
Types | Vacuum sintering, brazing, quenching, tempering, annealing, and more. |
Advantages | Oxidation prevention, contamination control, predictable results. |
Applications | Aerospace, automotive, medical devices, tooling. |
Learn how vacuum heat treatment can enhance your metal components—contact our experts today!