Vacuum hot pressing is a specialized process used in materials science and manufacturing to create high-density, high-strength materials under controlled conditions. It combines heat and pressure in a vacuum environment to sinter or bond materials, ensuring minimal contamination and oxidation. This technique is widely used for producing advanced materials like ceramics, composites, and metal powders, making it essential for research, teaching, and industrial applications. The vacuum environment eliminates unwanted reactions, allowing for precise control over material properties.
Key Points Explained:
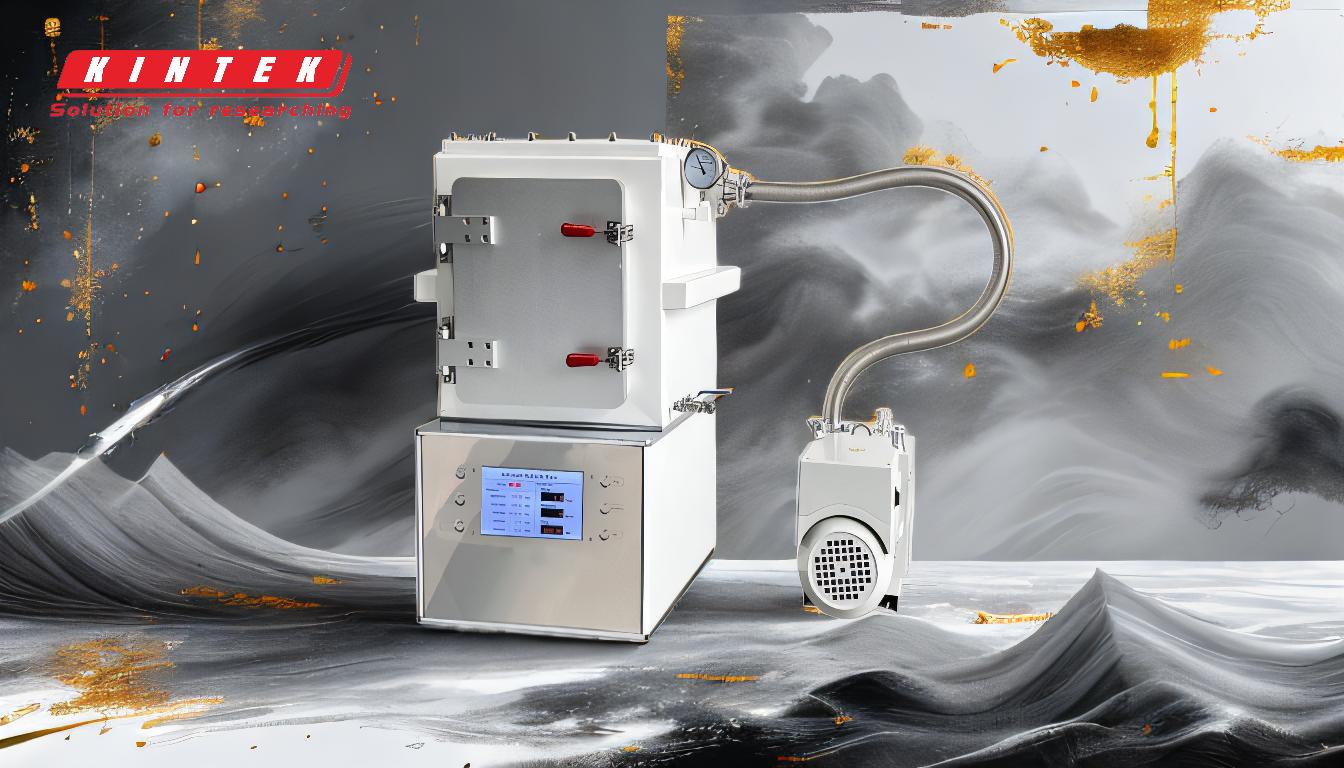
-
Definition and Purpose of Vacuum Hot Pressing
- Vacuum hot pressing involves applying heat and pressure to materials in a vacuum environment to achieve sintering or bonding.
- The primary purpose is to create dense, high-strength materials with minimal impurities or oxidation.
- It is particularly useful for materials like ceramics, composites, and metal powders, which require precise control over their microstructure and properties.
- The vacuum hot press environment ensures that the process is free from oxygen and reactive gases, preventing contamination and enabling high-quality results.
-
How Vacuum Hot Pressing Works
- The process takes place in a vacuum furnace, which is designed to maintain a low-pressure environment.
- Heating elements, such as resistance or induction heating, are used to generate and control high temperatures.
- Pressure is applied simultaneously to the material, ensuring densification and bonding.
- The vacuum environment eliminates oxidation, decarburization, and contamination, which are common issues in conventional sintering or bonding processes.
-
Applications of Vacuum Hot Pressing
- Hot Press Sintering: Used for sintering metal and ceramic powders to create dense, strong materials.
- Composite Preparation: Ideal for producing ceramic/metal composites and intermetallic compounds.
- Diffusion Welding: Facilitates research and development of diffusion welding processes for joining similar or dissimilar materials.
- Densification: Enables densification of oxygen, nitrogen, boron, carbon compounds, and their mixtures, which are challenging to process under normal conditions.
-
Advantages of Vacuum Hot Pressing
- High Purity: The vacuum environment prevents contamination, ensuring high-purity materials.
- Controlled Microstructure: Precise control over temperature and pressure allows for tailored material properties.
- Versatility: Suitable for a wide range of materials, including nonmetals, ceramics, and metals.
- Improved Mechanical Properties: The process enhances density, strength, and durability of the final product.
-
Comparison with Other Processes
- Unlike conventional sintering, vacuum hot pressing eliminates oxidation and contamination, resulting in superior material quality.
- Compared to vacuum brazing, which uses a lower-melting-point filler material, vacuum hot pressing directly bonds materials under heat and pressure without the need for additional filler.
-
Equipment and Design Considerations
- The vacuum hot press furnace is constructed with high-quality materials to withstand extreme temperatures and maintain a vacuum seal.
- Heating elements and pressure mechanisms are carefully designed to ensure uniform heat distribution and consistent pressure application.
- The furnace chamber is optimized for vacuum conditions, enabling efficient heat transfer and minimal energy loss.
-
Challenges and Limitations
- Cost: The equipment and operational costs are higher compared to conventional sintering methods.
- Complexity: The process requires precise control over temperature, pressure, and vacuum levels, making it more complex to operate.
- Material Limitations: While versatile, some materials may not be suitable for vacuum hot pressing due to their thermal or mechanical properties.
-
Future Trends and Innovations
- Advancements in vacuum furnace technology are improving energy efficiency and reducing costs.
- Research is focused on expanding the range of materials that can be processed using vacuum hot pressing.
- Automation and digital control systems are being integrated to enhance precision and reproducibility.
In summary, vacuum hot pressing is a critical process for producing advanced materials with high density, strength, and purity. Its ability to operate in a controlled vacuum environment makes it indispensable for applications in research, teaching, and industrial production. As technology advances, this method is expected to play an even greater role in materials science and manufacturing.
Summary Table:
Aspect | Details |
---|---|
Definition | Combines heat and pressure in a vacuum to sinter or bond materials. |
Purpose | Creates dense, high-strength materials with minimal impurities or oxidation. |
Applications | Sintering, composite preparation, diffusion welding, densification. |
Advantages | High purity, controlled microstructure, versatility, improved properties. |
Challenges | High cost, operational complexity, material limitations. |
Discover how vacuum hot pressing can enhance your material production—contact us today!