Furnaces utilize a variety of insulation materials to ensure energy efficiency, heat retention, and structural integrity. The most common insulation materials include refractory bricks, ceramic fibers, ceramic wool, mineral wool, and high-purity microcrystalline alumina fiber products. These materials are chosen based on their thermal insulation properties, durability, and ability to withstand high temperatures. The insulation can be fibrous (like blankets or mats) or rigid (like boards, slabs, or bricks), and often, furnaces employ multi-layered insulation systems for enhanced performance. The choice of insulation material depends on the specific type of furnace and its operational requirements.
Key Points Explained:
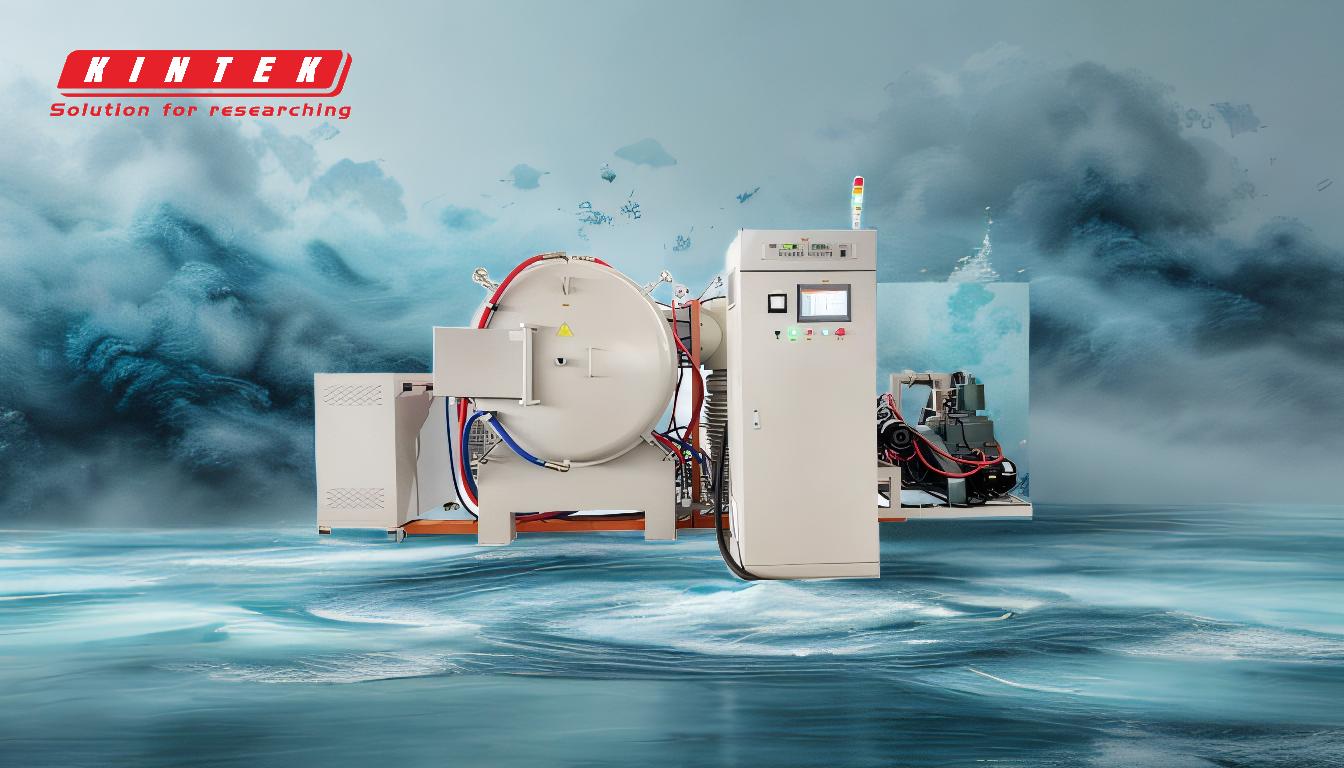
-
Types of Insulation Materials:
- Refractory Bricks: These are rigid, durable materials made from heat-resistant ceramics. They are commonly used in furnaces due to their ability to withstand extremely high temperatures and provide excellent thermal insulation. Lightweight refractory bricks are often preferred for their reduced heat storage capacity, which improves energy efficiency.
- Ceramic Fibers: These are fibrous materials made from alumina-silica compounds. They are lightweight, flexible, and offer superior thermal insulation. Ceramic fibers are often used in the form of blankets, mats, or boards and are ideal for applications requiring rapid heating and cooling cycles.
- Ceramic Wool: Similar to ceramic fibers, ceramic wool is a type of fibrous insulation material that provides excellent thermal insulation and reduces heat loss. It is often used in muffle furnaces for its ability to maintain high temperatures with minimal energy consumption.
- Mineral Wool: This is another type of fibrous insulation material, made from molten rock or slag. It is used in combination with ceramic wool in some furnaces to enhance thermal insulation properties.
- High-Purity Microcrystalline Alumina Fiber: This advanced insulation material offers exceptional thermal insulation and heat preservation. It is used in high-performance furnaces where maintaining precise temperature control is critical.
-
Forms of Insulation:
- Fibrous Insulation: This includes materials like ceramic fiber blankets, mats, and boards. Fibrous insulation is lightweight, flexible, and easy to install. It is particularly effective in applications where rapid temperature changes occur.
- Rigid Insulation: This includes materials like refractory bricks, boards, and slabs. Rigid insulation is more durable and provides structural support in addition to thermal insulation. It is commonly used in the lining of furnaces to protect the outer structure from high temperatures.
-
Multi-Layered Insulation:
- Many modern furnaces use a multi-layered insulation system to enhance performance. This involves combining different types of insulation materials (e.g., refractory bricks and ceramic fibers) in layers to optimize thermal efficiency and reduce heat loss. Multi-layered insulation also helps in achieving uniform temperature distribution within the furnace.
-
Application in Different Furnace Types:
- Batch Furnaces: These furnaces may use either fibrous or rigid insulation, depending on the specific application. Fibrous insulation is often preferred for its flexibility and ease of installation, while rigid insulation is chosen for its durability and structural support.
- Muffle Furnaces: These furnaces typically use a combination of ceramic wool and mineral wool for insulation. Some muffle furnaces also use ordinary refractory bricks or ceramic fibers. The choice of insulation material depends on the desired thermal performance and operational requirements of the furnace.
-
Benefits of High-Quality Insulation:
- Energy Conservation: High-quality insulation materials reduce heat loss, leading to significant energy savings. This is particularly important in industrial furnaces where energy costs can be substantial.
- Heat Loss Prevention: Effective insulation minimizes heat loss to the surrounding environment, ensuring that the furnace operates at optimal efficiency.
- Durability: Insulation materials like refractory bricks and ceramic fibers are highly durable and can withstand the harsh conditions inside a furnace, including high temperatures and thermal cycling.
- Temperature Control: Advanced insulation materials like high-purity microcrystalline alumina fiber provide precise temperature control, which is essential for processes requiring consistent and accurate heat application.
In summary, the choice of insulation material in a furnace is critical for achieving energy efficiency, heat retention, and operational performance. The selection depends on the specific type of furnace, its operational requirements, and the desired thermal properties. By using a combination of refractory bricks, ceramic fibers, and other advanced insulation materials, furnaces can achieve optimal performance and energy efficiency.
Summary Table:
Insulation Material | Properties | Common Uses |
---|---|---|
Refractory Bricks | Rigid, durable, withstands high temperatures, reduces heat storage | Lining of furnaces, structural support |
Ceramic Fibers | Lightweight, flexible, superior thermal insulation, rapid heating/cooling | Blankets, mats, boards for rapid temperature changes |
Ceramic Wool | Excellent thermal insulation, reduces heat loss, minimal energy consumption | Muffle furnaces, high-temperature applications |
Mineral Wool | Fibrous, enhances thermal insulation, made from molten rock or slag | Combined with ceramic wool for improved insulation |
High-Purity Alumina Fiber | Exceptional insulation, precise temperature control, heat preservation | High-performance furnaces, critical temperature applications |
Optimize your furnace's performance with the right insulation—contact our experts today!