PVD, or Physical Vapor Deposition, is a material deposition technique used to create thin films and coatings on various surfaces. It involves the use of metals and other materials to form highly durable, wear-resistant, and corrosion-resistant coatings. PVD coatings are known for their ability to enhance the properties of substrates, such as improving hardness, reducing friction, and increasing resistance to oxidation and high temperatures. The process is carried out at lower temperatures compared to other methods like CVD (Chemical Vapor Deposition), making it suitable for a wide range of applications, including aerospace, decorative coatings, and glass treatments.
Key Points Explained:
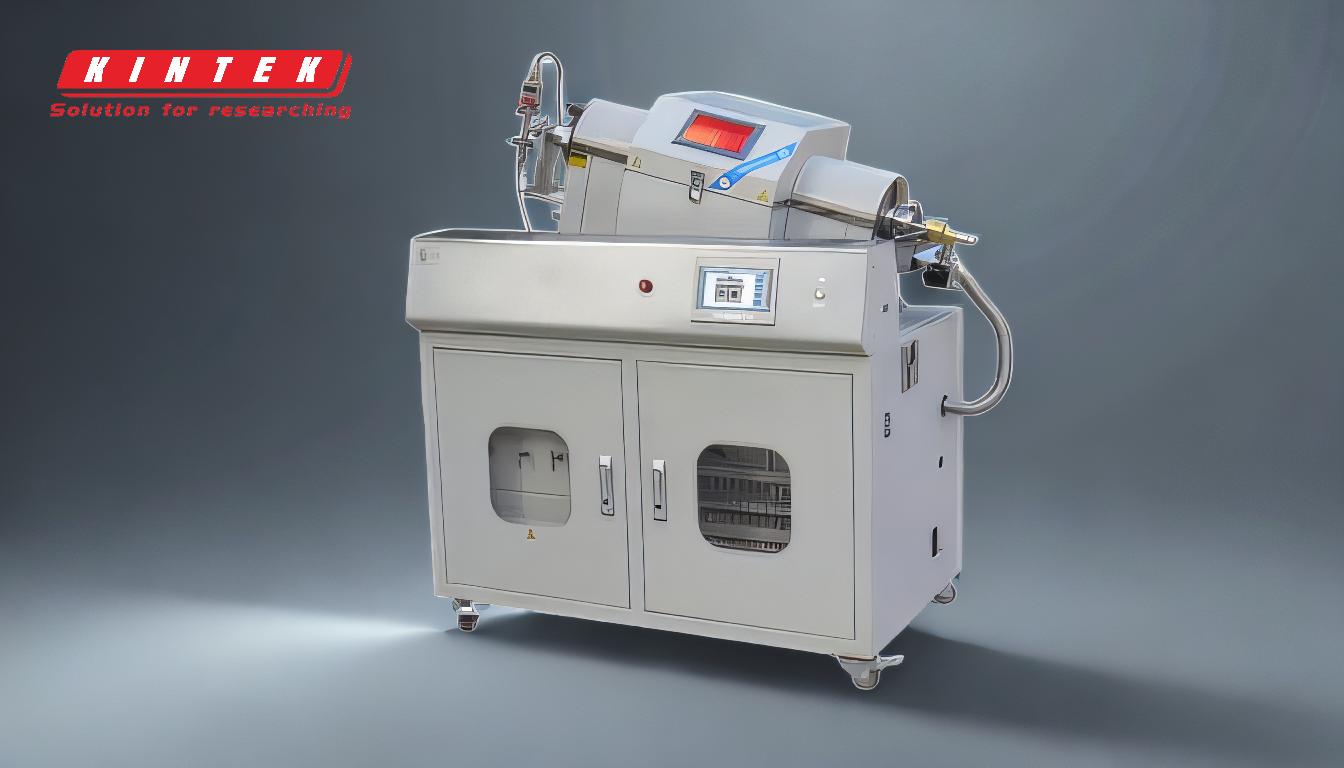
-
Definition of PVD:
- PVD stands for Physical Vapor Deposition, a technique used to deposit thin films and coatings onto surfaces.
- It involves the physical transfer of material from a source to a substrate, typically in a vacuum environment.
-
Materials Used in PVD:
- PVD materials primarily include metals such as titanium, chromium, aluminum, and their compounds (e.g., titanium nitride (TiN), chromium nitride (CrN)).
- These materials are chosen for their ability to form hard, durable, and corrosion-resistant coatings.
-
Properties of PVD Coatings:
- Wear Resistance: PVD coatings are highly wear-resistant, making them ideal for applications where durability is critical.
- Compressive Stress: PVD films often have higher compressive stress compared to CVD films, which contributes to their durability.
- Thickness: PVD coatings are very thin, typically ranging from 0.5 to 5 microns, yet they provide significant protection and enhancement to the substrate.
- Hardness: The hardness of PVD coatings is a key factor in their ability to improve the fatigue limit and endurance of substrates. For example, TiN coatings can increase the fatigue limit of Ti-6Al-4V alloy by 22%.
-
Advantages of PVD:
- Lower Temperature Deposition: PVD can be performed at lower temperatures compared to CVD, making it suitable for temperature-sensitive materials.
- Improved Oxidation Resistance: PVD coatings enhance the oxidation resistance of substrates, making them suitable for high-temperature applications.
- Friction Reduction: PVD coatings reduce friction, which is beneficial in mechanical and industrial applications.
- Corrosion Resistance: PVD coatings are highly resistant to corrosion, making them ideal for use in harsh environments.
-
Applications of PVD:
- Aerospace: PVD is used in aerospace technology to improve the resistance of components to high temperatures and ablation.
- Decorative Coatings: PVD is well-suited for decorative applications, such as coatings on watches, jewelry, and architectural elements.
- Glass Coatings: PVD is used to apply thin, durable coatings to glass, enhancing its properties and appearance.
- Diffusion Barrier Layers: PVD coatings are used as diffusion barriers in electronic components to prevent the migration of materials.
-
Comparison with CVD:
- PVD coatings are generally more wear-resistant and have higher compressive stress compared to CVD coatings.
- PVD can be deposited at lower temperatures, which is advantageous for substrates that cannot withstand high temperatures.
-
Replication of Original Finish:
- PVD coatings can replicate the original finish of materials with minimal effort, making them ideal for applications where aesthetics are important.
In summary, PVD is a versatile and effective technique for depositing thin, durable, and high-performance coatings on various substrates. Its ability to enhance properties such as hardness, wear resistance, and corrosion resistance makes it a valuable process in industries ranging from aerospace to decorative applications.
Summary Table:
Aspect | Details |
---|---|
Definition | Physical Vapor Deposition (PVD) deposits thin films in a vacuum environment. |
Materials | Titanium, chromium, aluminum, and their compounds (e.g., TiN, CrN). |
Properties | Wear resistance, compressive stress, thin coatings (0.5–5 µm), high hardness. |
Advantages | Lower temperature deposition, oxidation resistance, friction reduction. |
Applications | Aerospace, decorative coatings, glass treatments, diffusion barriers. |
Comparison with CVD | More wear-resistant, higher compressive stress, lower deposition temperature. |
Ready to explore how PVD can improve your materials? Contact us today for expert advice!