Calcination is a heat treatment process that involves heating materials, such as ores or other solid substances, to high temperatures below their melting point in the absence or limited supply of air or oxygen. This process is used to induce thermal decomposition, remove volatile substances, or cause phase transitions. The primary machine used for calcination is a calciner, which is a specialized reactor designed for this purpose. Calcination can also be performed in furnaces, such as muffle, reverberatory, or shaft furnaces, depending on the specific requirements of the process. These machines are designed to operate under controlled conditions, ensuring the desired chemical and physical transformations occur efficiently.
Key Points Explained:
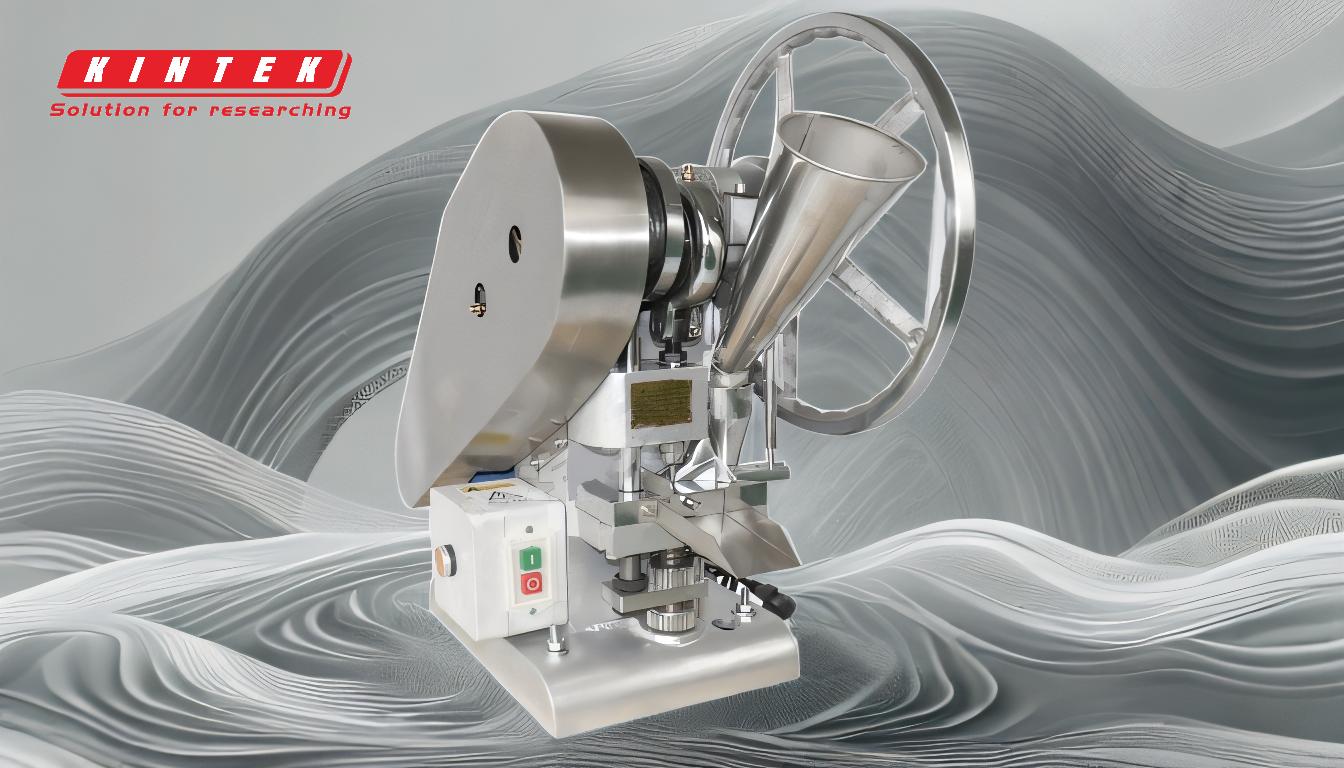
-
What is Calcination?
- Calcination is a thermal treatment process where materials are heated to high temperatures (below their melting point) in the absence or limited supply of air or oxygen.
- It is used to induce thermal decomposition, remove volatile substances, or cause phase transitions in materials like ores or solid compounds.
-
Primary Machine for Calcination: The Calciner
- A calciner is the most common machine used for calcination. It is a cylindrical reactor designed to handle high temperatures and controlled environments.
- Calcination in a calciner typically produces carbon dioxide as a byproduct, which is released during the reaction.
- The calciner's design ensures uniform heating and efficient processing of materials.
-
Alternative Machines: Furnaces
- In some cases, furnaces are used for calcination due to the high temperatures required.
- Common types of furnaces used include:
- Muffle Furnaces: Enclosed furnaces where the material is heated indirectly, protecting it from direct exposure to flames or combustion gases.
- Reverberatory Furnaces: Furnaces where heat is reflected from the roof and walls onto the material, providing uniform heating.
- Shaft Furnaces or Kilns: Vertical furnaces where materials are heated as they move through the furnace, often used for continuous processes.
-
Key Features of Calcination Equipment
- Temperature Control: Calcination requires precise temperature control to ensure the material is heated below its melting point but high enough to induce the desired chemical changes.
- Controlled Atmosphere: The absence or limited supply of air or oxygen is critical to prevent oxidation and ensure the desired reactions occur.
- Efficient Heat Transfer: Equipment like calciners and furnaces are designed to provide uniform heating and efficient heat transfer to the material.
-
Applications of Calcination
- Calcination is widely used in industries such as metallurgy, cement production, and chemical manufacturing.
- Common applications include:
- Extracting metals from ores (e.g., converting limestone to lime).
- Removing impurities or volatile substances from materials.
- Producing materials with specific chemical or physical properties.
-
Considerations for Equipment Selection
- When selecting equipment for calcination, factors to consider include:
- Material Properties: The type of material being processed and its thermal stability.
- Process Requirements: The desired temperature, atmosphere, and duration of the calcination process.
- Scale of Operation: Whether the process is batch or continuous, and the required throughput.
- Energy Efficiency: The energy consumption and heat recovery capabilities of the equipment.
- When selecting equipment for calcination, factors to consider include:
By understanding these key points, a purchaser can make informed decisions about the type of equipment needed for calcination based on the specific requirements of their application.
Summary Table:
Aspect | Details |
---|---|
What is Calcination? | A thermal process heating materials below melting point, removing volatiles. |
Primary Machine | Calciner: A cylindrical reactor for high-temperature, controlled processing. |
Alternative Machines | Muffle, Reverberatory, and Shaft Furnaces for specific calcination needs. |
Key Features | Precise temperature control, controlled atmosphere, efficient heat transfer. |
Applications | Metallurgy, cement production, chemical manufacturing, and more. |
Equipment Selection | Consider material properties, process requirements, scale, and efficiency. |
Need help selecting the right calcination equipment? Contact our experts today!