Physical vapor deposition (PVD) is a versatile technique used to deposit thin films of materials onto substrates. The process involves vaporizing a solid material in a vacuum environment and then condensing it onto a target surface. The materials used in PVD depend on the specific application, but they generally fall into categories such as metals, ceramics, and alloys. Common techniques like thermal evaporation and sputtering utilize specific materials for heating elements, targets, and substrates. Understanding the materials involved is crucial for optimizing the PVD process and achieving desired coating properties.
Key Points Explained:
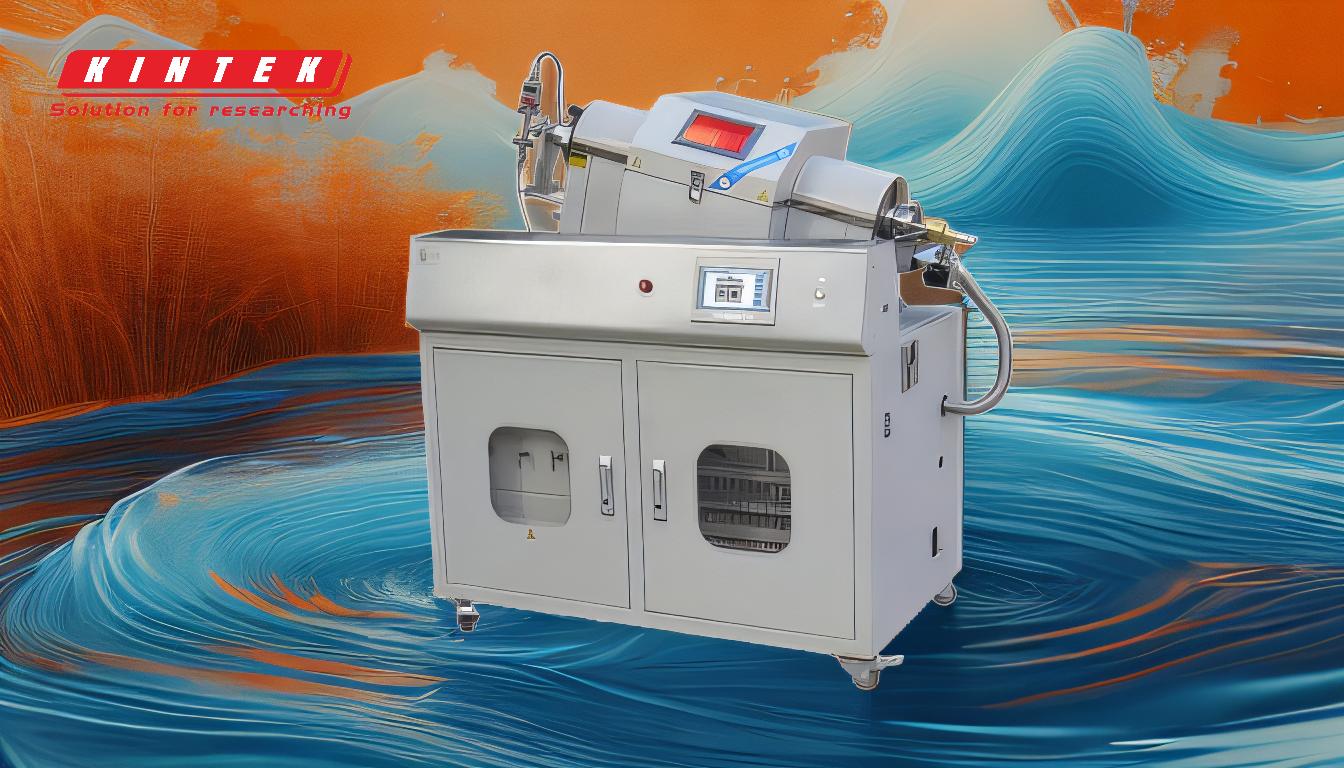
-
Common PVD Techniques:
- Thermal Evaporation: This technique involves heating a material until it vaporizes. The vapor then condenses on a substrate to form a thin film. Materials used for heating elements in thermal evaporation include tungsten, molybdenum, niobium, graphite, and alumina. These materials are chosen for their high melting points and thermal stability.
- Sputtering: In this method, a target material is bombarded with high-energy ions, causing atoms to be ejected and deposited onto a substrate. Sputtering targets can be made from a wide range of materials, including metals, alloys, and ceramics, depending on the desired coating properties.
-
Materials Used in PVD:
- Metals: Metals such as aluminum, titanium, chromium, and gold are commonly used in PVD for their excellent conductivity, reflectivity, and corrosion resistance. These metals are often deposited as thin films for applications in electronics, optics, and decorative coatings.
- Ceramics: Ceramic materials like titanium nitride (TiN), chromium nitride (CrN), and aluminum oxide (Al2O3) are used in PVD to create hard, wear-resistant coatings. These coatings are ideal for cutting tools, molds, and other components subjected to high wear and friction.
- Alloys: Alloys such as stainless steel, nickel-chromium, and titanium-aluminum are used in PVD to achieve specific mechanical and chemical properties. These materials are often chosen for their combination of strength, durability, and resistance to oxidation.
-
Heating Elements and Carriers:
- Tungsten: Known for its high melting point and excellent thermal conductivity, tungsten is commonly used in filaments and heating elements for thermal evaporation.
- Molybdenum: Molybdenum is used in heating elements and crucibles due to its high melting point and resistance to thermal shock.
- Graphite: Graphite is used in boats and crucibles for its thermal stability and ability to withstand high temperatures without reacting with the material being evaporated.
- Alumina: Alumina is used in crucibles and insulating components for its high thermal resistance and chemical inertness.
-
Applications of PVD Coatings:
- Electronics: PVD coatings are used in the production of semiconductors, thin-film transistors, and solar cells. Materials like aluminum and gold are commonly used for their electrical conductivity and reflectivity.
- Optics: PVD coatings are applied to lenses, mirrors, and other optical components to enhance their reflectivity, durability, and resistance to environmental factors. Materials like titanium dioxide (TiO2) and silicon dioxide (SiO2) are often used in these applications.
- Decorative Coatings: PVD is used to apply thin, durable, and aesthetically pleasing coatings to items like watches, jewelry, and automotive parts. Materials like gold, titanium nitride, and zirconium nitride are popular choices for their color and durability.
-
Advantages of PVD:
- Durability: PVD coatings are highly durable and resistant to wear, corrosion, and oxidation, making them ideal for demanding applications.
- Precision: The process allows for precise control over the thickness and composition of the deposited films, enabling the creation of coatings with specific properties.
- Versatility: PVD can be used with a wide range of materials, including metals, ceramics, and alloys, making it suitable for a variety of industries and applications.
In summary, the materials used in physical vapor deposition are diverse and depend on the specific technique and application. Metals, ceramics, and alloys are commonly used, with specific materials chosen for their thermal, mechanical, and chemical properties. Understanding these materials and their roles in the PVD process is essential for achieving high-quality coatings and optimizing performance in various applications.
Summary Table:
Category | Materials | Applications |
---|---|---|
Metals | Aluminum, Titanium, Chromium, Gold | Electronics, Optics, Decorative Coatings |
Ceramics | Titanium Nitride (TiN), Chromium Nitride (CrN), Aluminum Oxide (Al2O3) | Cutting Tools, Molds, Wear-Resistant Coatings |
Alloys | Stainless Steel, Nickel-Chromium, Titanium-Aluminum | High-Strength, Durable, Oxidation-Resistant Coatings |
Heating Elements | Tungsten, Molybdenum, Graphite, Alumina | Thermal Evaporation, Sputtering |
Optimize your PVD process with the right materials—contact our experts today for tailored solutions!