Vacuum brazing is a specialized process used to join materials in a high-temperature, low-oxygen environment, ensuring strong, clean, and precise bonds. The materials used in vacuum brazing include base metals like stainless steel, titanium, and nickel alloys, as well as filler metals such as silver, copper, and gold-based alloys. The process relies on a vacuum brazing furnace to create the necessary conditions for brazing, including precise temperature control and a vacuum environment to prevent oxidation. The furnace's ability to maintain high-temperature uniformity and rapid cooling capabilities ensures consistent and high-quality brazed joints. This process is widely used in industries like aerospace, particle physics, and metallurgical research, where precision and reliability are critical.
Key Points Explained:
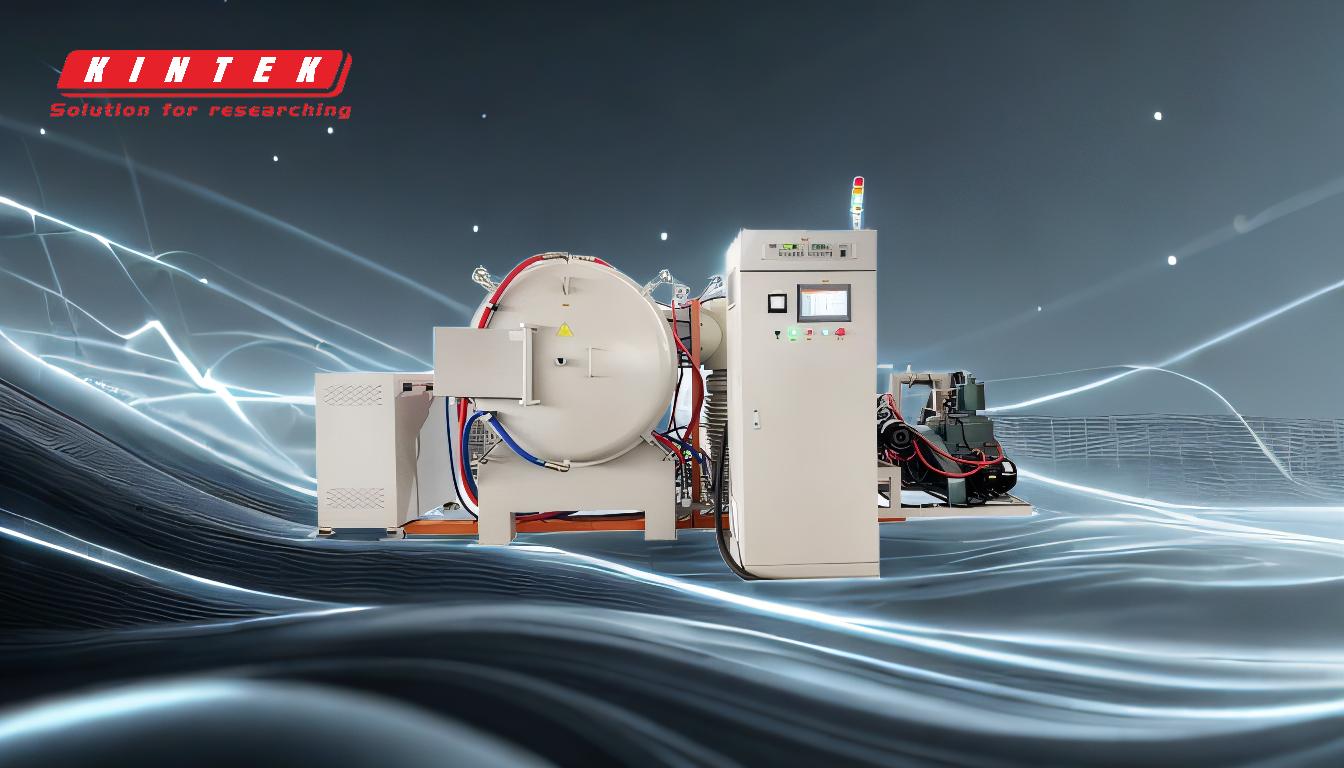
-
Materials Used in Vacuum Brazing:
- Base Metals: Common base metals include stainless steel, titanium, and nickel alloys. These materials are chosen for their strength, corrosion resistance, and compatibility with high-temperature processes.
- Filler Metals: Filler metals, such as silver, copper, and gold-based alloys, are used to create the bond between the base metals. These materials have lower melting points than the base metals and flow into the joint during heating, forming a strong bond upon cooling.
-
Role of the Vacuum Brazing Furnace:
- The vacuum brazing furnace is essential for creating the controlled environment required for the process. It ensures high-temperature uniformity, rapid cooling, and a vacuum environment to prevent oxidation.
- The furnace's heating system melts the filler metal, while the vacuum system removes oxygen and other gases that could interfere with the brazing process.
-
Process Steps:
- Preparation: The workpiece is cleaned and assembled with the filler metal in place.
- Brazing: The assembled workpiece is placed in the furnace, heated to the brazing temperature, and held at that temperature until the filler metal flows and forms the joint.
- Cooling and Inspection: After brazing, the workpiece is cooled in a controlled manner to prevent oxidation and inspected for quality.
-
Applications and Industries:
- Vacuum brazing is used in industries that require high precision and reliability, such as aerospace, particle physics, and metallurgical research. The process meets stringent standards like NADCAP, ensuring consistent quality.
-
Safety and Operational Considerations:
- Operators must follow strict safety protocols, including wearing protective equipment and maintaining a clean environment. The furnace's water, power, and gas supplies must be checked regularly to ensure safe and efficient operation.
By understanding the materials, equipment, and processes involved in vacuum brazing, purchasers can make informed decisions about the tools and consumables needed for their specific applications.
Summary Table:
Category | Materials |
---|---|
Base Metals | Stainless steel, titanium, nickel alloys |
Filler Metals | Silver, copper, gold-based alloys |
Applications | Aerospace, particle physics, metallurgical research |
Key Features | High-temperature resistance, corrosion resistance, precise bonding |
Need help selecting the right materials for vacuum brazing? Contact our experts today for tailored solutions!