Induction heating is a highly efficient method for heating conductive materials, primarily metals, through the generation of eddy currents within the material. This process relies on electromagnetic induction, where an alternating current in a coil creates a magnetic field that induces currents in the conductive material, leading to internal heating. While metals are the primary materials that can be directly heated, non-conductive materials like plastics can be indirectly heated by first heating a conductive metal inductor. Induction heating is widely used in melting precious metals, non-ferrous metals, and their alloys, making it a versatile and precise heating method in various industrial applications.
Key Points Explained:
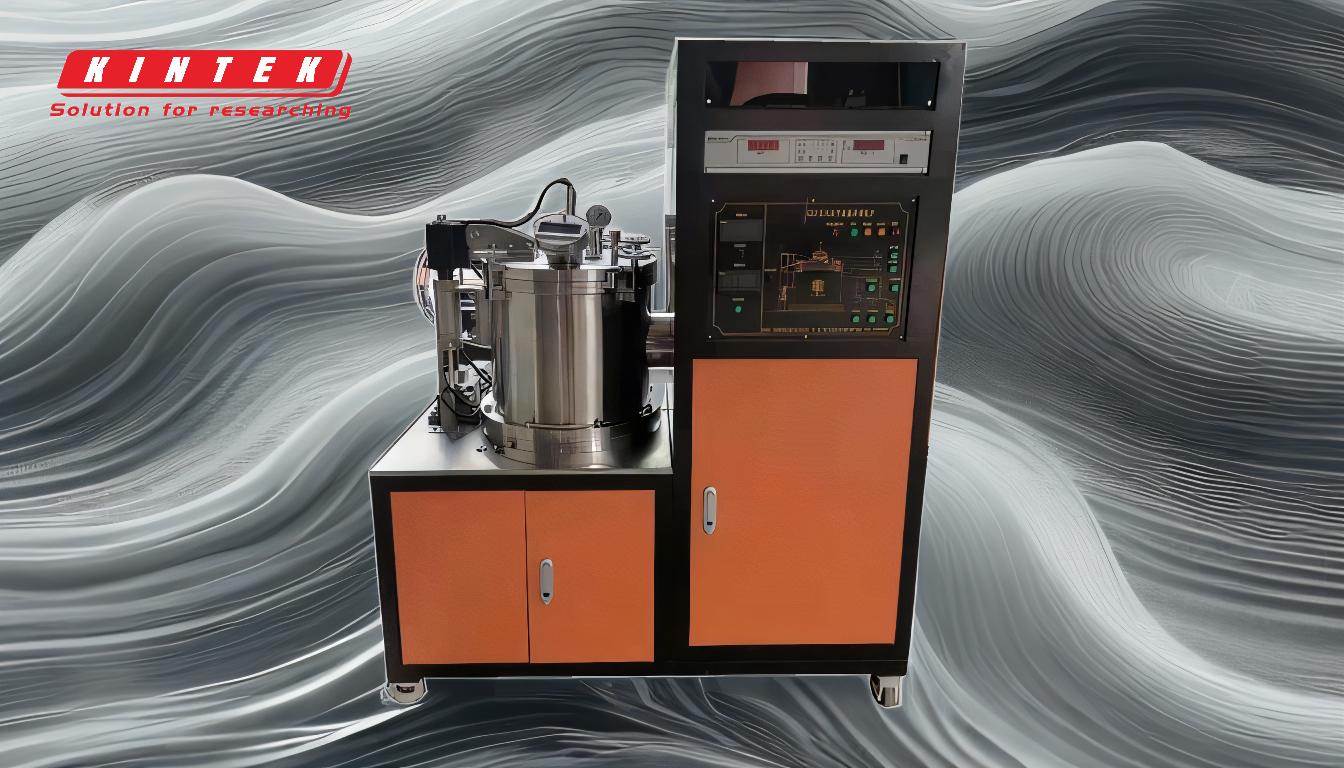
-
Conductive Materials (Metals) Can Be Directly Heated:
- Induction heating works by generating eddy currents within conductive materials, which then produce heat due to electrical resistance. This makes it ideal for metals, which are naturally conductive.
- Examples of metals that can be directly heated include:
- Precious Metals: Gold, silver, copper, palladium, and platinum, as well as their alloys.
- Non-Ferrous Metals: Copper, aluminum, brass, and bronze.
- The process is efficient because the heat is generated internally within the material, ensuring uniform heating and minimizing energy loss.
-
Non-Conductive Materials (e.g., Plastics) Require Indirect Heating:
- Non-conductive materials like plastics cannot be directly heated by induction because they do not conduct electricity and therefore cannot generate eddy currents.
- However, these materials can still be heated indirectly by placing a conductive metal inductor (such as a metal plate or container) within the induction field. The metal heats up, and the heat is then transferred to the non-conductive material through conduction or radiation.
- This method is commonly used in applications like plastic welding or molding, where precise and localized heating is required.
-
Mechanism of Induction Heating:
- Induction heating relies on the principle of electromagnetic induction. An alternating current is passed through a coil, creating a powerful alternating magnetic field.
- When a conductive material is placed within this magnetic field, eddy currents are induced within the material. These currents flow in closed loops and generate heat due to the Joule effect (resistance to the flow of electricity) and, in the case of ferromagnetic materials, hysteresis (energy loss due to magnetic domain realignment).
- This internal heating mechanism ensures that the material is heated uniformly and efficiently, with minimal heat loss to the surrounding environment.
-
Applications of Induction Heating:
- Melting Metals: Induction heating is widely used in foundries and metalworking industries for melting metals and creating alloys. It is particularly useful for precious metals and non-ferrous metals due to its precise temperature control and efficiency.
- Heat Treatment: Induction heating is used for processes like hardening, annealing, and tempering, where localized and controlled heating is required.
- Indirect Heating of Non-Conductive Materials: As mentioned earlier, induction heating can be used to heat non-conductive materials indirectly, making it versatile for applications in industries like plastics, food processing, and more.
-
Advantages of Induction Heating:
- Efficiency: Induction heating is highly efficient because the heat is generated directly within the material, reducing energy waste.
- Precision: The process allows for precise control over the heating area and temperature, making it ideal for applications requiring localized heating.
- Speed: Induction heating is fast, as the material heats up almost instantaneously when exposed to the magnetic field.
- Cleanliness: Since induction heating does not involve open flames or combustion, it is a clean process with minimal environmental impact.
In summary, induction heating is a versatile and efficient method primarily used for heating conductive materials like metals. Non-conductive materials can also be heated indirectly by using a conductive metal inductor. The process is widely applied in various industries, from metal melting and heat treatment to plastic welding, due to its precision, speed, and energy efficiency.
Summary Table:
Key Aspect | Details |
---|---|
Conductive Materials | Metals like gold, silver, copper, and alloys can be directly heated. |
Non-Conductive Materials | Plastics require indirect heating via a conductive metal inductor. |
Mechanism | Eddy currents generate heat through electromagnetic induction. |
Applications | Melting metals, heat treatment, and indirect heating of non-conductive materials. |
Advantages | High efficiency, precision, speed, and cleanliness. |
Discover how induction heating can transform your industrial processes—contact our experts today!