To measure high temperatures in a furnace, thermocouples or other temperature sensors are commonly used. These devices are placed inside the furnace to monitor and control the temperature accurately. Thermocouples, in particular, are widely used due to their ability to withstand extreme temperatures and provide reliable readings. The process involves placing the sensor in direct contact with the furnace environment, ensuring real-time temperature feedback for precise control.
Key Points Explained:
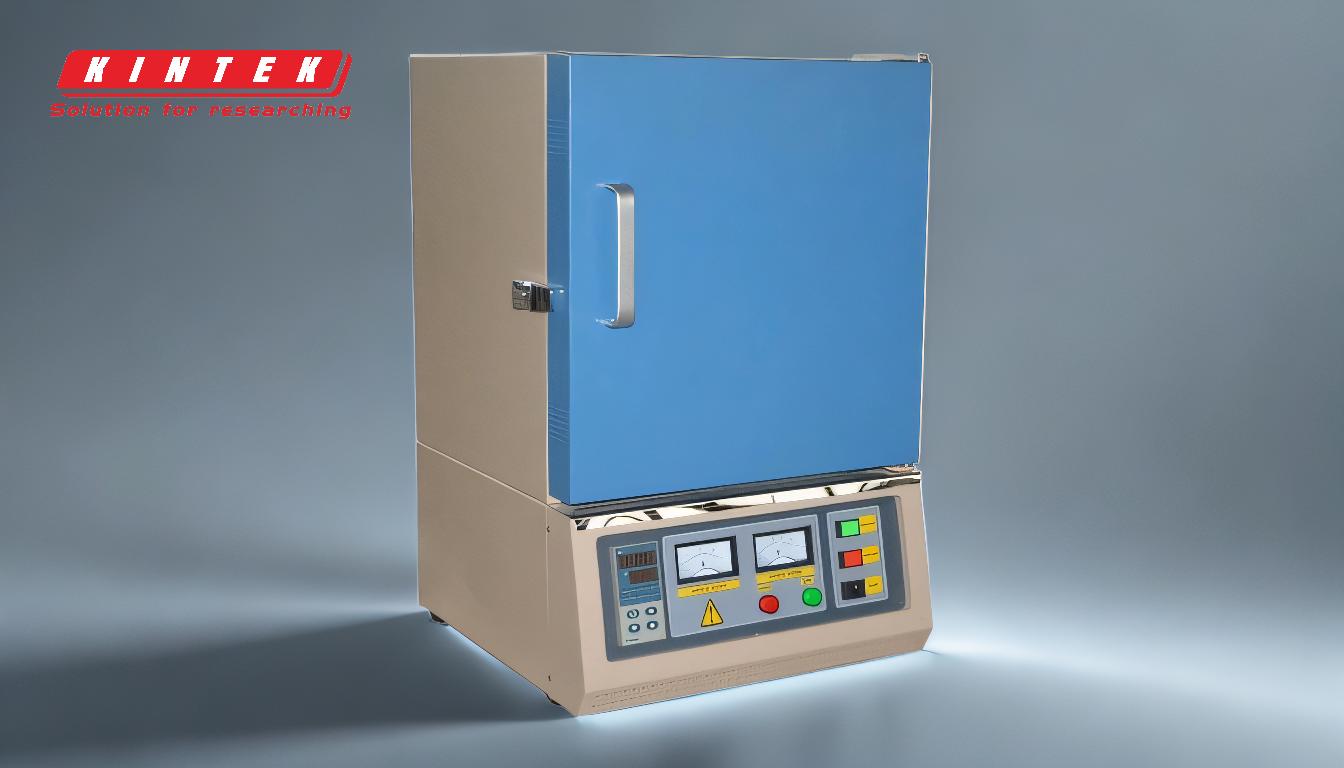
-
Thermocouples as Primary Sensors:
- Thermocouples are the most common devices used to measure high temperatures in furnaces. They consist of two dissimilar metals joined at one end, which generate a voltage proportional to the temperature difference between the junction and the other end.
- They are capable of measuring temperatures ranging from -200°C to over 2300°C, making them suitable for various furnace applications.
- Their durability and ability to withstand harsh environments make them ideal for high-temperature measurements.
-
Placement of Sensors:
- Temperature sensors, including thermocouples, are strategically placed inside the furnace to ensure accurate readings. For example, in a tube furnace, the thermocouple is often inserted directly into the tube where the sample is heated.
- Proper placement ensures that the sensor measures the temperature of the furnace environment accurately, providing reliable data for control systems.
-
Control and Monitoring Systems:
- The data from thermocouples or other sensors is fed into a control system, which adjusts the furnace's heating elements to maintain the desired temperature.
- Modern furnaces often integrate digital controllers that display real-time temperature readings and allow users to set precise temperature profiles.
-
Alternative Temperature Sensors:
- In addition to thermocouples, other sensors like resistance temperature detectors (RTDs) and infrared pyrometers may be used, depending on the specific requirements of the furnace.
- RTDs are more accurate at lower temperatures but have a limited range compared to thermocouples.
- Infrared pyrometers measure temperature without direct contact, making them suitable for applications where physical sensors cannot be used.
-
Importance of Calibration:
- Regular calibration of temperature sensors is crucial to ensure accurate measurements. Over time, sensors may drift or degrade, leading to incorrect readings.
- Calibration involves comparing the sensor's output to a known standard and adjusting it if necessary.
By using thermocouples or other temperature sensors, furnaces can achieve precise temperature control, which is essential for processes requiring high-temperature conditions. Proper placement, calibration, and integration with control systems ensure reliable and accurate temperature measurements.
Summary Table:
Sensor Type | Temperature Range | Key Features |
---|---|---|
Thermocouples | -200°C to 2300°C | Durable, withstands harsh environments, widely used for high-temperature furnaces |
RTDs | -200°C to 850°C | High accuracy at lower temperatures, limited range compared to thermocouples |
Infrared Pyrometers | Varies | Non-contact measurement, ideal for applications where direct sensors can't be used |
Need help choosing the right temperature sensor for your furnace? Contact our experts today!