To measure the temperature of a furnace, specialized instruments and sensors are used, each designed to handle the extreme conditions and provide accurate readings. The most common devices include thermocouples, pyrometers, and infrared thermometers. Thermocouples are widely used due to their durability and ability to measure high temperatures directly. Pyrometers, on the other hand, measure temperature by detecting the thermal radiation emitted by the furnace, making them ideal for non-contact measurements. Infrared thermometers are also used for non-contact temperature readings, especially in situations where direct sensor placement is impractical. Each method has its advantages and is chosen based on the specific requirements of the furnace and the application.
Key Points Explained:
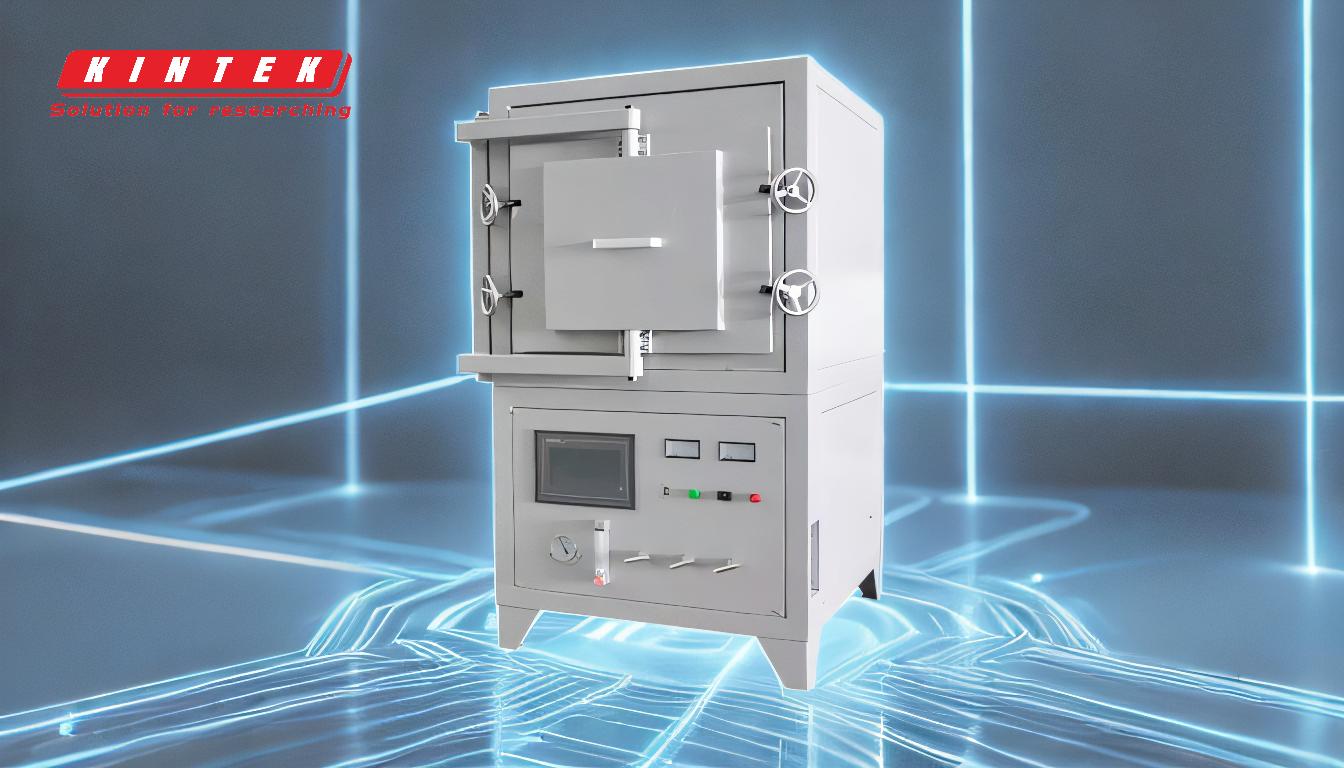
-
Thermocouples:
- How They Work: Thermocouples consist of two different metal wires joined at one end. When exposed to heat, they generate a voltage proportional to the temperature difference between the hot junction (in the furnace) and the cold junction (outside the furnace).
- Advantages: They are durable, can measure very high temperatures (up to 2300°C), and provide direct temperature readings.
- Applications: Commonly used in industrial furnaces, kilns, and ovens where direct contact with the heat source is possible.
-
Pyrometers:
- How They Work: Pyrometers measure temperature by detecting the thermal radiation emitted by the furnace. They do not require physical contact with the furnace, making them ideal for high-temperature environments where contact sensors might fail.
- Advantages: Non-contact measurement, suitable for extremely high temperatures, and can measure temperature from a distance.
- Applications: Used in steel manufacturing, glass production, and other industries where non-contact temperature measurement is necessary.
-
Infrared Thermometers:
- How They Work: These devices detect infrared energy emitted by the furnace and convert it into a temperature reading. They are similar to pyrometers but are often more portable and easier to use.
- Advantages: Non-contact, quick readings, and can measure temperature from a safe distance.
- Applications: Ideal for spot-checking temperatures in various industrial settings, including furnaces, where direct contact is not feasible.
-
Resistance Temperature Detectors (RTDs):
- How They Work: RTDs measure temperature by correlating the resistance of the RTD element with temperature. They are made from pure metals like platinum, which have a predictable resistance change with temperature.
- Advantages: High accuracy and stability over a wide temperature range.
- Applications: Used in applications where precise temperature control is required, such as in laboratory furnaces.
-
Thermistors:
- How They Work: Thermistors are temperature-sensitive resistors that change their resistance with temperature. They are typically made from ceramic or polymer materials.
- Advantages: High sensitivity and accuracy over a limited temperature range.
- Applications: Suitable for lower temperature ranges and precise temperature measurement in controlled environments.
-
Bimetallic Thermometers:
- How They Work: These thermometers use two different metals bonded together, which expand at different rates when heated. The differential expansion causes the bimetallic strip to bend, indicating the temperature.
- Advantages: Simple, durable, and do not require external power.
- Applications: Often used in industrial settings for basic temperature monitoring where high accuracy is not critical.
-
Optical Pyrometers:
- How They Work: Optical pyrometers measure temperature by comparing the brightness of the furnace's glow to a calibrated light source. The observer adjusts the light source until it matches the furnace's glow, indicating the temperature.
- Advantages: High accuracy for very high temperatures and non-contact measurement.
- Applications: Used in metalworking and glass manufacturing where visual temperature estimation is necessary.
Each of these temperature measurement devices has its own set of advantages and is chosen based on the specific requirements of the furnace and the application. Understanding the working principles and applications of these devices helps in selecting the most appropriate tool for accurate and reliable temperature measurement in various industrial processes.
Summary Table:
Device | How It Works | Advantages | Applications |
---|---|---|---|
Thermocouples | Two metal wires generate voltage proportional to temperature difference. | Durable, measures up to 2300°C, direct readings. | Industrial furnaces, kilns, ovens. |
Pyrometers | Detects thermal radiation emitted by the furnace. | Non-contact, measures high temperatures from a distance. | Steel manufacturing, glass production. |
Infrared Thermometers | Detects infrared energy and converts it into temperature readings. | Non-contact, quick readings, portable. | Spot-checking in industrial settings. |
RTDs | Measures temperature by correlating resistance changes in platinum. | High accuracy, stable over a wide range. | Laboratory furnaces, precise temperature control. |
Thermistors | Temperature-sensitive resistors change resistance with temperature. | High sensitivity, accurate over limited ranges. | Controlled environments, lower temperature ranges. |
Bimetallic Thermometers | Two metals expand at different rates, bending to indicate temperature. | Simple, durable, no external power needed. | Basic temperature monitoring in industrial settings. |
Optical Pyrometers | Compares furnace glow to a calibrated light source. | High accuracy for very high temperatures, non-contact. | Metalworking, glass manufacturing. |
Need help selecting the right temperature measurement tool for your furnace? Contact our experts today!