Induction heating is a process that uses electromagnetic induction to heat conductive materials, typically metals. However, not all metals can be effectively induction heated. The ability of a metal to be induction heated depends on its electrical conductivity, magnetic permeability, and other material properties. Metals that are non-conductive or have very low electrical conductivity, such as certain non-metallic materials or highly resistive metals, cannot be induction heated directly. Additionally, metals that are non-magnetic or have low magnetic permeability may also be difficult to heat using induction. Understanding these limitations is crucial for selecting the right materials for induction heating applications.
Key Points Explained:
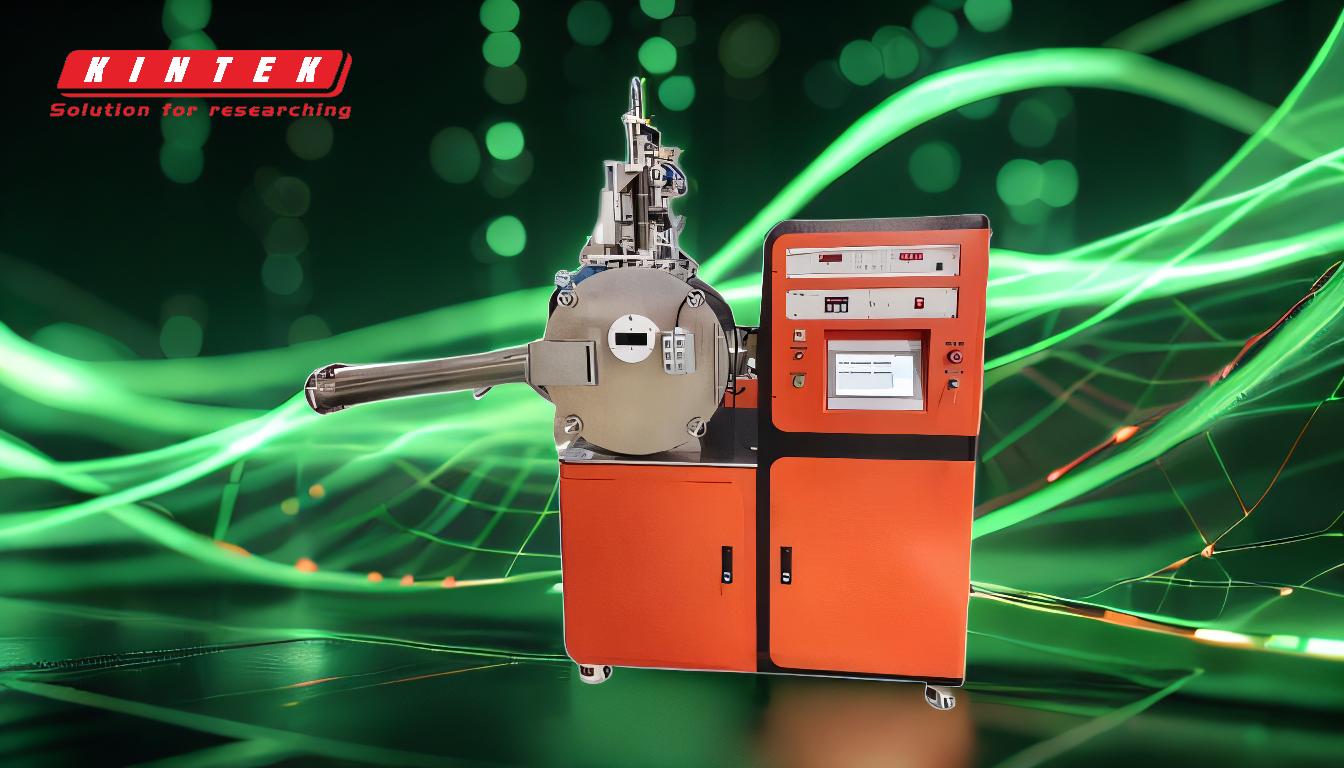
-
Electrical Conductivity:
- Explanation: Induction heating relies on the principle of electromagnetic induction, where an alternating magnetic field induces eddy currents in a conductive material. These eddy currents generate heat due to the material's electrical resistance. Metals with high electrical conductivity, such as copper and aluminum, are excellent candidates for induction heating because they allow for efficient eddy current generation.
- Non-Conductive Metals: Metals with very low electrical conductivity, such as certain non-metallic materials or highly resistive metals, cannot be induction heated directly. For example, materials like ceramics or certain types of glass are non-conductive and cannot be heated using induction.
-
Magnetic Permeability:
- Explanation: Magnetic permeability is a measure of a material's ability to support the formation of a magnetic field within itself. Ferromagnetic materials, such as iron, nickel, and cobalt, have high magnetic permeability and are easily heated by induction. The magnetic field induces additional heating through hysteresis losses in these materials.
- Non-Magnetic Metals: Metals that are non-magnetic or have low magnetic permeability, such as austenitic stainless steels (e.g., 304 and 316), are more difficult to heat using induction. These materials do not experience significant hysteresis losses, making them less suitable for induction heating.
-
Material Thickness and Skin Depth:
- Explanation: The effectiveness of induction heating also depends on the material's thickness relative to the skin depth, which is the depth at which the electromagnetic field penetrates the material. For thin materials, the skin depth may be larger than the material thickness, leading to inefficient heating.
- Thin or Non-Uniform Materials: Metals that are too thin or have non-uniform thickness may not heat evenly or effectively using induction. This is because the induced currents may not penetrate deeply enough to generate sufficient heat throughout the material.
-
Temperature Limitations:
- Explanation: Some metals have temperature limitations that make them unsuitable for induction heating. For example, certain metals may melt or degrade at the temperatures required for effective induction heating.
- Low Melting Point Metals: Metals with low melting points, such as lead or tin, may not be suitable for induction heating if the required temperatures exceed their melting points. Additionally, some metals may undergo undesirable phase changes or oxidation at high temperatures.
-
Indirect Heating of Non-Metals:
- Explanation: Non-conductive materials, such as plastics or ceramics, cannot be directly induction heated. However, they can be heated indirectly by first heating a conductive metal inductor and then transferring the heat to the non-conductive material.
- Applications: This method is often used in applications where non-metallic materials need to be heated, such as in plastic welding or curing processes. The metal inductor acts as a heat source, and the heat is transferred to the non-conductive material through conduction or radiation.
In summary, the ability to induction heat a metal depends on its electrical conductivity, magnetic permeability, thickness, and temperature limitations. Metals that are non-conductive, non-magnetic, too thin, or have low melting points may not be suitable for direct induction heating. Understanding these factors is essential for selecting the appropriate materials and methods for induction heating applications.
Summary Table:
Factor | Impact on Induction Heating |
---|---|
Electrical Conductivity | Metals with low conductivity (e.g., ceramics) cannot generate sufficient eddy currents. |
Magnetic Permeability | Non-magnetic metals (e.g., austenitic stainless steel) experience minimal hysteresis losses. |
Material Thickness | Thin or non-uniform materials may not heat evenly due to insufficient skin depth penetration. |
Temperature Limits | Metals with low melting points (e.g., lead, tin) may degrade or melt during induction heating. |
Non-Metals | Non-conductive materials (e.g., plastics) require indirect heating via a conductive inductor. |
Need help selecting the right materials for induction heating? Contact our experts today for tailored solutions!