Annealing is a heat treatment process used to alter the physical and sometimes chemical properties of a material, primarily metals, to increase ductility, reduce hardness, and improve machinability. The primary goal of annealing is to relieve internal stresses that develop during fabrication processes, such as casting, welding, or cold working. This process involves heating the metal to a specific temperature, holding it at that temperature for a certain period, and then cooling it slowly. The slow cooling process allows the metal to achieve a more stable, less stressed state, which enhances its workability and performance.
Key Points Explained:
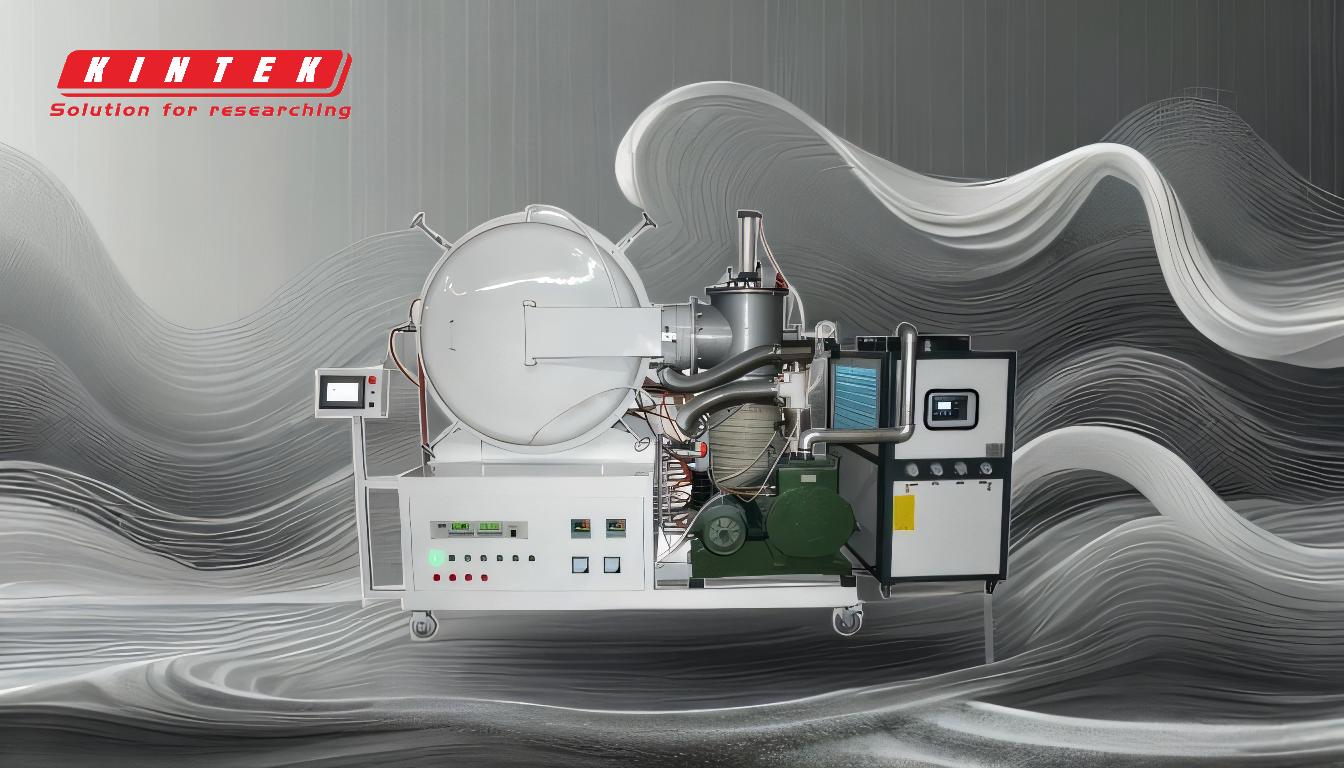
-
Purpose of Annealing:
- Relieve Internal Stresses: Annealing helps to eliminate internal stresses that occur during manufacturing processes like casting, welding, or cold working. These stresses can lead to defects such as hot or cold shuts, which are cracks or voids in the metal.
- Improve Ductility: By reducing hardness, annealing makes the metal more ductile, which is essential for further processing, such as machining or forming.
- Enhance Machinability: Softer metals are easier to machine, leading to better surface finishes and longer tool life.
-
Metals That Undergo Annealing:
- Steel: One of the most common metals subjected to annealing. Different types of steel, such as carbon steel, alloy steel, and stainless steel, undergo annealing to improve their properties.
- Copper: Annealing is frequently used for copper to increase its ductility, making it easier to draw into wires or form into shapes.
- Aluminum: Although aluminum is naturally soft, annealing can be used to relieve stresses after cold working processes.
- Brass and Bronze: These copper alloys are often annealed to improve their workability and reduce brittleness.
- Nickel Alloys: High-performance alloys like Inconel are annealed to relieve stresses and improve their mechanical properties.
-
Annealing Process:
- Heating: The metal is heated to a specific temperature, which varies depending on the type of metal. For example, steel is typically heated to between 1,200°F and 1,600°F (650°C to 870°C).
- Soaking: The metal is held at the annealing temperature for a period of time to ensure uniform heating throughout the material.
- Cooling: The metal is cooled slowly, often in the furnace or in a controlled environment, to prevent the reintroduction of stresses.
-
Types of Annealing:
- Full Annealing: Involves heating the metal above its critical temperature and then cooling it slowly. This process is used to achieve maximum softness and ductility.
- Process Annealing: Used to relieve stresses in cold-worked metals without significantly altering the microstructure. It is often used for low-carbon steels.
- Stress Relief Annealing: Specifically aimed at reducing internal stresses without changing the material's hardness or strength significantly.
-
Applications of Annealing:
- Manufacturing: Annealing is widely used in the manufacturing of components that require high precision and durability, such as gears, bearings, and automotive parts.
- Electrical Industry: Copper and aluminum wires are annealed to improve their conductivity and flexibility.
- Aerospace: High-performance alloys used in aerospace applications are annealed to ensure they can withstand extreme conditions without failure.
In summary, annealing is a critical heat treatment process used across various industries to improve the properties of metals. By relieving internal stresses and enhancing ductility, annealing makes metals more suitable for further processing and end-use applications. Common metals that undergo annealing include steel, copper, aluminum, brass, bronze, and nickel alloys. The process involves precise heating, soaking, and slow cooling to achieve the desired material properties.
Summary Table:
Metal | Purpose of Annealing |
---|---|
Steel | Relieves internal stresses, improves ductility, and enhances machinability. |
Copper | Increases ductility, making it easier to draw into wires or form into shapes. |
Aluminum | Relieves stresses after cold working processes. |
Brass/Bronze | Improves workability and reduces brittleness. |
Nickel Alloys | Relieves stresses and improves mechanical properties for high-performance applications. |
Need annealing solutions for your metal processing? Contact our experts today!