Temperature control in resistance furnaces is a critical aspect of ensuring efficient and precise heating processes. Various methods are employed to achieve this, depending on the type of furnace and its specific application. These methods include adjusting the voltage supplied to the heating elements, using temperature sensors and controllers, and employing advanced systems that regulate fuel and air supply. Additionally, in specialized furnaces, such as those used in laboratories or high-temperature applications, additional controls like flow and pressure regulation of the medium, or atmosphere control, may be used to maintain the desired temperature. Each method has its advantages and is chosen based on the furnace's requirements, the process being carried out, and the level of precision needed.
Key Points Explained:
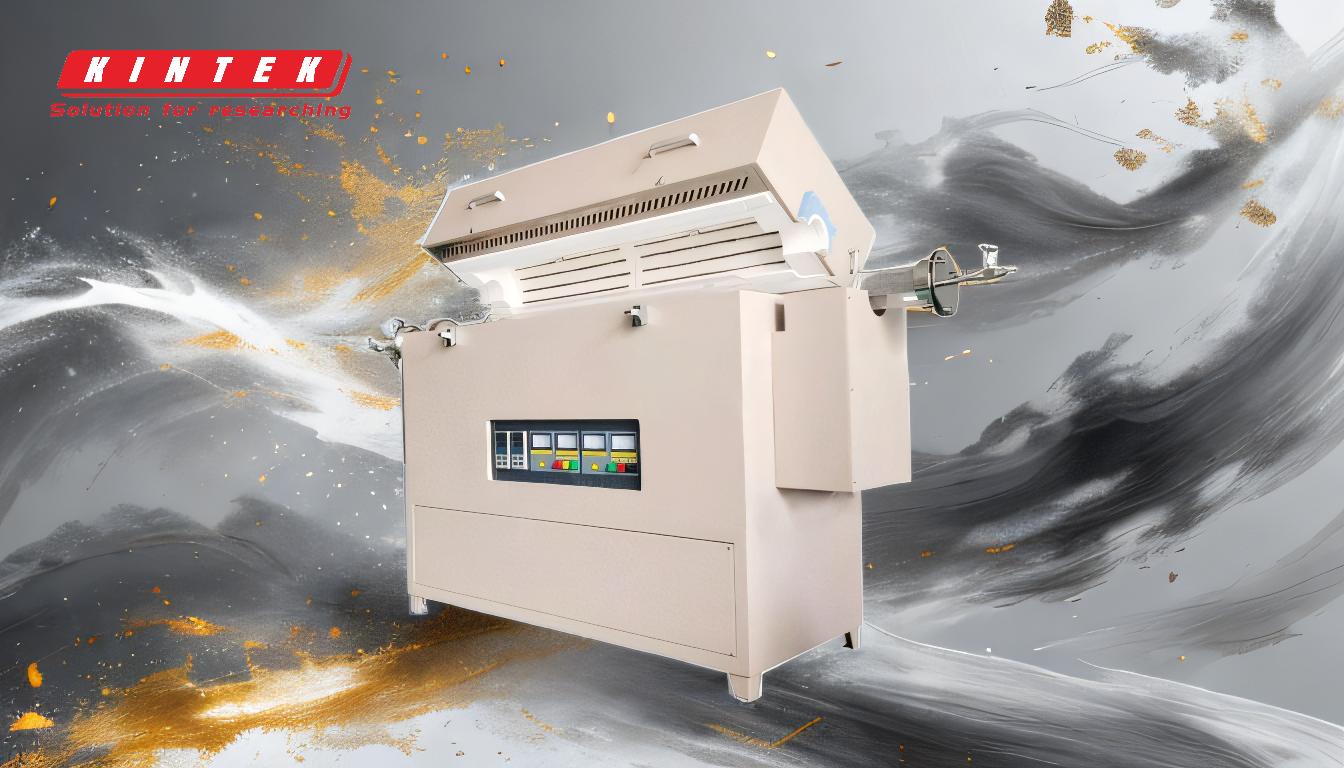
-
Voltage Control Methods:
- Transformer Tappings: By changing the transformer tappings, the voltage supplied to the heating elements can be adjusted, thereby controlling the temperature.
- Auto-Transformer: An auto-transformer can be used to vary the voltage smoothly, providing precise control over the temperature.
- Induction Regulator: This device allows for continuous adjustment of the voltage, offering fine-tuned temperature control.
- Independent Generating Set: In large furnaces, an independent generating set may be used to provide a variable voltage supply, ensuring stable and controlled heating.
-
Temperature Sensors and Controllers:
- Thermocouples: These sensors detect the furnace temperature and send the data to a temperature controller. The controller then adjusts the power input to the furnace to maintain the desired temperature.
- Automatic Temperature Controllers: Devices like the transistor constant temperature automatic temperature controller or constant temperature controllers are used in high-temperature muffle furnaces to maintain a stable temperature.
-
Flow and Pressure Control:
- Flow Control: In laboratory electric furnaces, controlling the flow rate of the medium before it enters the furnace helps in achieving the desired temperature.
- Pressure Control: Regulating the pressure of the medium after it enters the furnace ensures that the temperature is maintained consistently, meeting the needs of both front and rear processes.
-
Atmosphere Control:
- Flow Control: Adjusting the flow of gases within the furnace helps in controlling the type and composition of the atmosphere, which in turn affects the temperature.
- Air Pressure Control: By regulating the air pressure within the heating chamber, the temperature can be more precisely controlled.
- Mass Spectrometry Control: This advanced method allows for precise monitoring and control of the atmosphere, ensuring optimal temperature conditions.
-
Industrial Furnace Control Systems:
- Basic Systems: These systems only regulate the fuel flow, making them cost-effective but less efficient. They are suitable for applications where precision is not critical.
- Proportional Systems: These systems control both the fuel and air supply, improving fuel efficiency and reducing operating costs. They offer better temperature control compared to basic systems.
- Pulse Control Systems: These systems maintain a fixed ratio of fuel and air with high flame velocity, ensuring consistent temperatures throughout the process cycle. They are highly efficient and provide precise temperature control.
-
Automatic Adjustment and Control:
- Temperature Signal Transmission: The temperature control system detects the furnace temperature through a thermocouple and transmits the temperature signal to the controller.
- Power Output Adjustment: The controller adjusts the current according to the set temperature curve, controlling the power output of the heating element. This allows for automatic adjustment and control of the furnace temperature, ensuring it remains within the desired range.
In summary, the methods used to control the temperature of resistance furnaces are diverse and tailored to the specific requirements of the furnace and the process it is used for. From simple voltage adjustments to sophisticated proportional and pulse control systems, each method offers unique advantages in terms of efficiency, precision, and cost-effectiveness. Understanding these methods is crucial for selecting the right temperature control strategy for any given application.
Summary Table:
Method | Description |
---|---|
Voltage Control | Adjusts voltage via transformer tappings, auto-transformers, or induction regulators. |
Temperature Sensors | Uses thermocouples and controllers to maintain precise temperature levels. |
Flow & Pressure Control | Regulates medium flow and pressure for consistent temperature in lab furnaces. |
Atmosphere Control | Controls gas flow and air pressure to optimize furnace temperature. |
Industrial Control Systems | Includes basic, proportional, and pulse systems for efficient temperature control. |
Automatic Adjustment | Adjusts power output based on temperature signals for precise control. |
Need the right temperature control solution for your furnace? Contact our experts today!