Crucibles are essential tools in high-temperature processes, but improper handling or usage can lead to damage, contamination, or even safety hazards. To ensure their longevity and effectiveness, it is crucial to avoid common mistakes such as rolling, stacking, or exposing them to rapid temperature changes. Proper handling, storage, and usage practices, including using the right tools and avoiding incompatible materials, are key to maintaining crucible integrity. Additionally, preheating, gradual cooling, and adhering to temperature limits are critical steps to prevent thermal shock and ensure accurate results in chemical analysis or metal melting processes.
Key Points Explained:
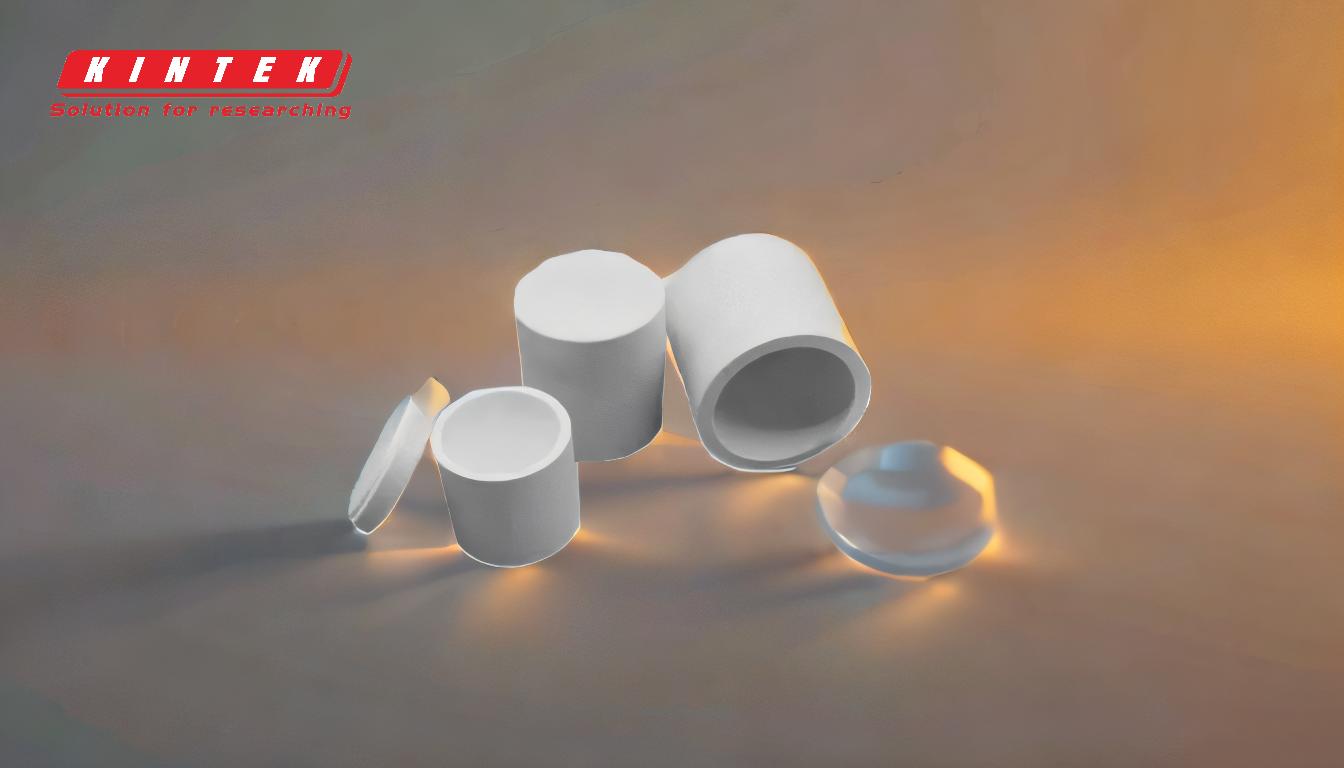
-
Avoid Rolling or Stacking Crucibles
- Rolling crucibles during transportation or storage can damage the protective glaze, compromising their structural integrity.
- Stacking crucibles inside one another can lead to cracking due to pressure or uneven weight distribution.
- Always handle crucibles individually and with care to prevent physical damage.
-
Do Not Place Crucibles Directly on Concrete or Cold Surfaces
- Concrete surfaces can cause crucibles to absorb moisture, leading to cracks when heated.
- Placing hot crucibles on cold metal tables can result in thermal shock and breakage due to rapid cooling.
- Use insulating materials like cardboard or proper stands to protect crucibles from moisture and temperature extremes.
-
Use Proper Tools for Handling
- Always use properly fitting tongs to handle crucibles, as improper tools can cause chips, cracks, or other damage.
- Avoid gripping crucibles too tightly or at awkward angles, which can lead to stress points and breakage.
-
Prevent Contamination by Using Separate Crucibles for Different Materials
- Using the same crucible for different metals or chemicals can lead to contamination, affecting the purity of the materials being processed.
- Always empty and clean crucibles thoroughly after each use to avoid residue buildup, which can cause damage during subsequent heating.
-
Avoid Thermal Shock by Gradual Heating and Cooling
- Rapid temperature changes can cause crucibles, especially ceramic or graphite types, to crack or fail.
- Preheat crucibles gradually along with the furnace to ensure even temperature distribution.
- Allow crucibles to cool down slowly after use to prevent thermal stress.
-
Do Not Use Crucibles Beyond Their Specified Limits
- Each crucible material has specific temperature and chemical compatibility limits.
- For example, alumina ceramic crucibles should not be used with alkaline substances or hydrofluoric acid, as these can cause corrosion.
- Always adhere to the manufacturer's guidelines for temperature ranges and compatible materials.
-
Proper Storage and Preheating
- Store crucibles in a dry environment to prevent moisture absorption, which can lead to cracking during heating.
- Preheating crucibles before use ensures they are free from moisture and ready for high-temperature processes.
- Even small amounts of moisture can cause significant damage when exposed to sudden heat.
-
Avoid Bonding with Furnace Bases
- Placing a cardboard plate or other insulating material between the crucible and the furnace base can prevent bonding caused by high temperatures.
- This step ensures easy removal of the crucible after heating and prevents damage to both the crucible and the furnace.
-
Handle Crucible Covers Correctly
- When using a crucible with a cover, place the cover on the sintered base first, then place the crucible on top.
- This method prevents crushing or misalignment, ensuring proper handling during the sintering process.
By following these guidelines, users can maximize the lifespan of their crucibles, ensure accurate results in chemical or metallurgical processes, and avoid unnecessary damage or safety risks. Proper care and attention to detail are essential for maintaining the performance and reliability of crucibles in high-temperature applications.
Summary Table:
Common Mistake | Impact | Prevention Tips |
---|---|---|
Rolling or stacking crucibles | Damages protective glaze, causes cracking | Handle individually, avoid pressure or uneven weight distribution |
Placing on concrete or cold surfaces | Absorbs moisture, leads to cracks or thermal shock | Use insulating materials like cardboard or proper stands |
Improper handling tools | Causes chips, cracks, or stress points | Use properly fitting tongs, avoid tight grips or awkward angles |
Contamination from mixed materials | Affects material purity, causes residue buildup | Use separate crucibles, clean thoroughly after each use |
Rapid temperature changes | Leads to thermal shock, cracking, or failure | Preheat gradually, allow slow cooling |
Exceeding specified limits | Corrosion or damage from incompatible materials or temperatures | Follow manufacturer guidelines for temperature and chemical compatibility |
Improper storage or preheating | Moisture absorption causes cracking during heating | Store in a dry environment, preheat before use |
Bonding with furnace bases | Difficult removal, damage to crucible and furnace | Use insulating materials like cardboard plates |
Incorrect cover handling | Crushing or misalignment during sintering | Place cover on sintered base first, then crucible |
Ensure your crucibles perform at their best—contact our experts today for personalized advice and solutions!