When performing a sieve analysis, it is essential to follow a series of precautions to ensure accurate and reliable results. These precautions include proper sample preparation, selection of appropriate sieves, careful handling during the sieving process, and thorough cleaning and maintenance of equipment. Additionally, specific considerations must be taken for wet sieving to prevent sample alteration. By adhering to these precautions, one can minimize errors and obtain consistent and precise data.
Key Points Explained:
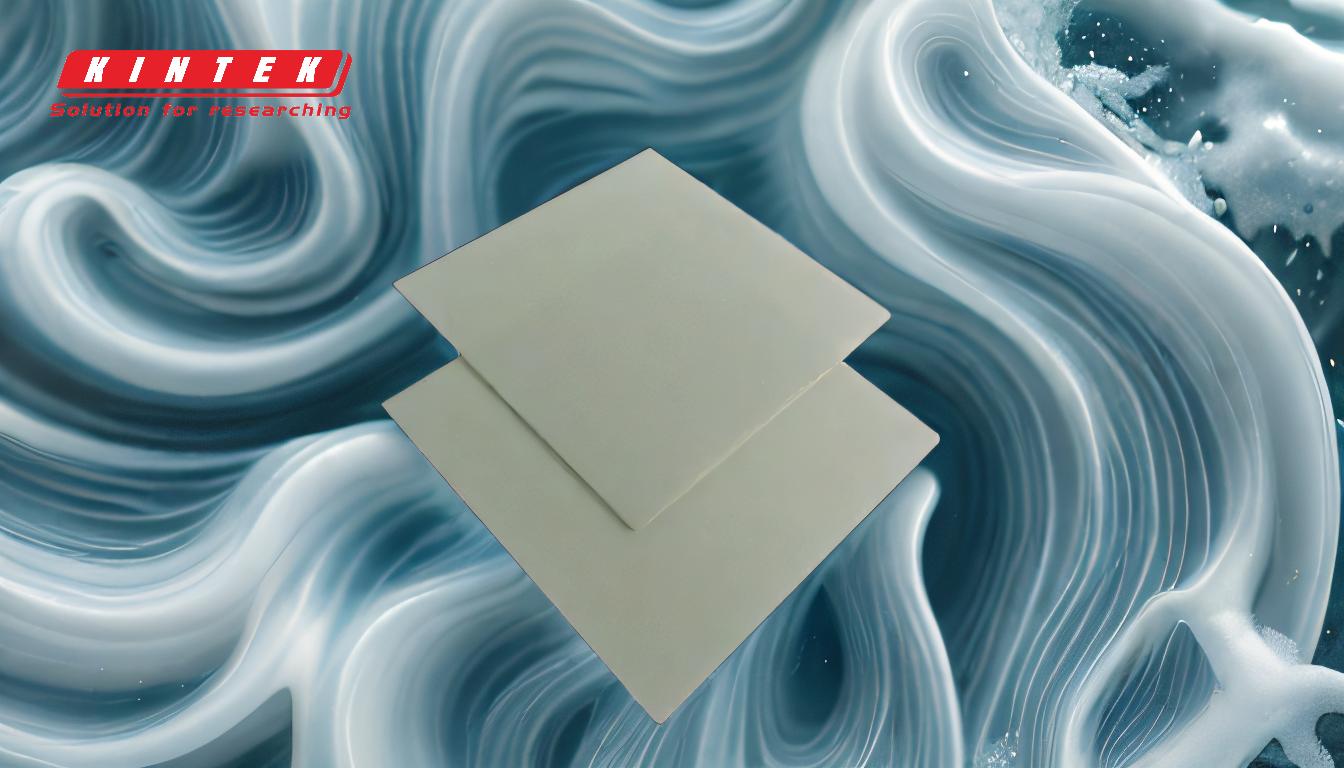
-
Sample Preparation:
- Pre-drying and Conditioning: Ensure the sample is dry and free from moisture unless wet sieving is required. For wet sieving, avoid using liquids that may cause the sample to swell, dissolve, or react.
- Sample Division: Use proper techniques to divide the sample into representative portions to avoid bias in the analysis.
- Weighing: Accurately weigh the sample before and after sieving to calculate the percentage retained on each sieve.
-
Selection of Sieves:
- Mesh Size and Standards: Choose sieves with appropriate mesh sizes that comply with applicable standards (e.g., ASTM or ISO). Ensure the wire cloth is uniform and free from defects.
- Sieve Stack Preparation: Pre-record the identification and tare weight of each sieve to avoid confusion during the analysis.
-
Sieving Process:
- Manual or Mechanical Shaking: Use a sieve shaker for consistent and efficient sieving. If done manually, ensure uniform shaking to avoid errors.
- Wet Sieving Precautions: For wet sieving, ensure the liquid used does not alter the sample's properties. Monitor the sample for any changes in volume or composition.
- Duration of Sieving: Follow the recommended sieving time to ensure all particles have had sufficient opportunity to pass through the sieve openings.
-
Data Collection and Analysis:
- Weighing Fractions: After sieving, weigh the material retained on each sieve accurately. Calculate the percentage retained and ensure the total mass matches the initial sample mass.
- Result Interpretation: Analyze the data to determine the particle size distribution. Ensure the results are within acceptable limits and repeat the analysis if inconsistencies are observed.
-
Equipment Maintenance:
- Cleaning and Drying: Clean and dry the sieves thoroughly after each use to prevent contamination and ensure longevity.
- Inspection: Regularly inspect the sieves for wear and tear, especially the wire mesh, to maintain accuracy. Replace damaged sieves promptly.
-
Minimizing Errors:
- Wire Cloth Variation: Ensure the uniformity of the woven mesh by working with reputable manufacturers who monitor the actual opening sizes and uniformity of the wire cloth.
- Environmental Factors: Conduct the analysis in a controlled environment to avoid external influences such as humidity or vibrations.
By following these precautions, you can ensure the accuracy and reliability of your sieve analysis results, whether for quality control, research, or other applications. Proper attention to detail at every stage of the process will minimize errors and provide consistent data for decision-making.
Summary Table:
Key Precautions | Details |
---|---|
Sample Preparation | Pre-dry samples, divide representatively, and weigh accurately. |
Sieve Selection | Choose ASTM/ISO-compliant sieves with uniform mesh sizes. |
Sieving Process | Use mechanical shaking or manual uniformity; monitor wet sieving. |
Data Collection | Weigh fractions accurately and interpret particle size distribution. |
Equipment Maintenance | Clean, dry, and inspect sieves regularly to prevent errors. |
Error Minimization | Ensure mesh uniformity and control environmental factors. |
Need help with sieve analysis? Contact our experts today for reliable solutions!