Annealing is a heat treatment process used to alter the physical and sometimes chemical properties of materials, primarily to relieve internal stresses, increase ductility, and reduce hardness. This process is applicable to a wide range of metals, including steel, alloy steel, aluminum, brass, and copper. By heating the material to a specific temperature, holding it there, and then cooling it slowly, annealing helps repair defects in the crystalline structure, making the material more workable and suitable for machining or cold working. The process is essential for improving machinability, facilitating cold working, and enhancing mechanical or electrical properties.
Key Points Explained:
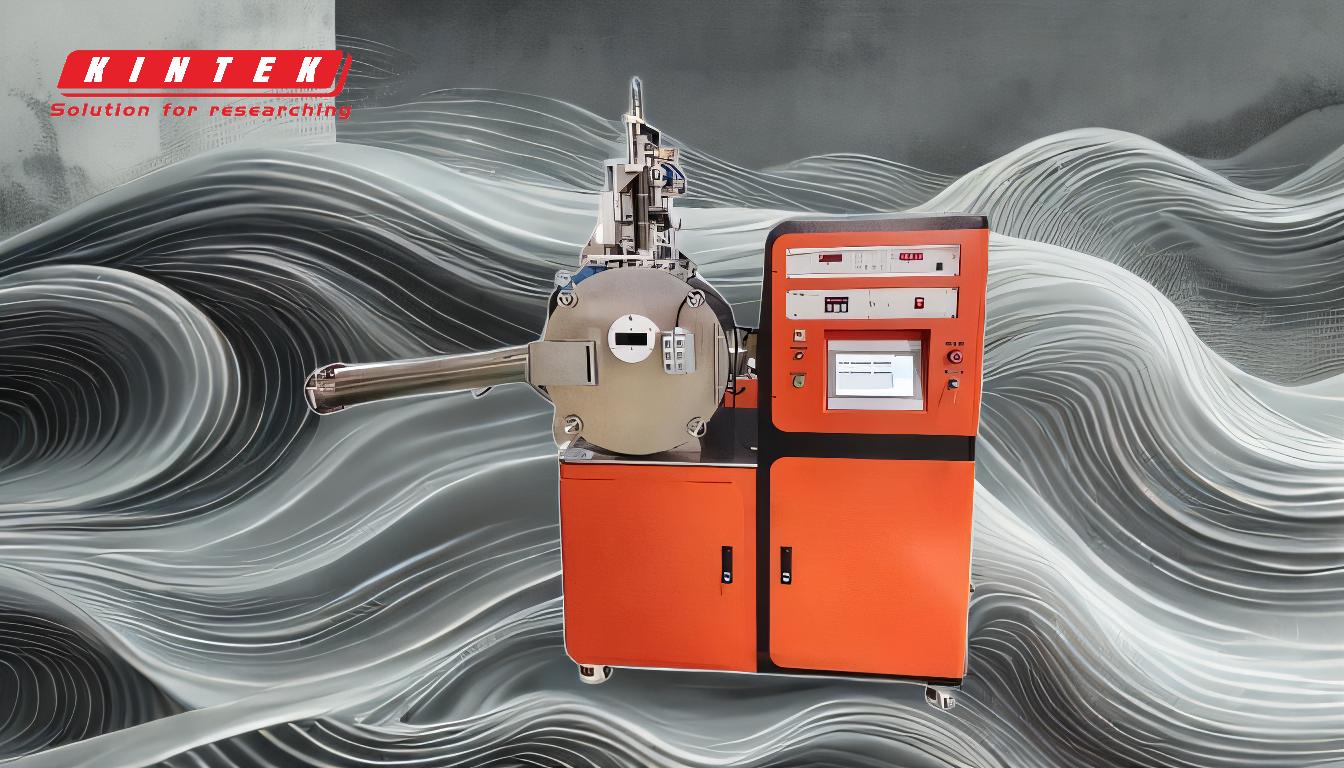
-
Purpose of Annealing:
- Relieve Internal Stresses: Annealing is primarily used to eliminate internal stresses caused by fabrication processes like casting, welding, or machining. These stresses can lead to material failure or deformation during service.
- Increase Ductility: By reducing hardness, annealing makes materials more ductile, which is crucial for processes like cold working or machining.
- Improve Workability: The process makes materials easier to shape, cut, or form without cracking or breaking.
-
Materials Commonly Annealed:
- Steel and Alloy Steel: These are the most common materials subjected to annealing due to their widespread use in manufacturing and construction.
- Aluminum: Annealing is used to soften aluminum, making it more suitable for forming and shaping.
- Brass and Copper: These metals are annealed to improve their ductility and reduce brittleness, which is essential for applications in electrical wiring and plumbing.
-
Annealing Process:
- Heating Phase: The material is heated to a temperature above its recrystallization point but below its melting point. This allows the crystalline structure to become fluid while remaining solid.
- Holding Phase: The material is held at this temperature for a specific duration to allow defects in the crystalline structure to repair themselves.
- Cooling Phase: The material is cooled slowly to room temperature, which helps in forming a more uniform and ductile crystalline structure.
-
Benefits of Annealing:
- Enhanced Machinability: Annealing makes materials easier to machine by reducing hardness and internal stresses.
- Improved Cold Working: The process increases ductility, making materials more suitable for cold working processes like bending or stamping.
- Increased Dimensional Stability: Annealing helps in reducing the risk of warping or distortion during manufacturing processes.
- Enhanced Mechanical and Electrical Properties: The process can improve the material's mechanical strength and electrical conductivity.
-
Applications of Annealing:
- Manufacturing: Annealing is widely used in the manufacturing of metal components, tools, and machinery parts.
- Construction: It is essential for producing structural steel and other construction materials that require high ductility and strength.
- Electronics: Annealed copper and aluminum are commonly used in electrical wiring and components due to their improved conductivity and flexibility.
- Automotive: The process is used in the production of automotive parts that require high strength and durability.
In summary, annealing is a critical heat treatment process used across various industries to improve the properties of metals, making them more suitable for a wide range of applications. By understanding the materials that benefit from annealing and the specific steps involved in the process, manufacturers can produce components with enhanced mechanical properties, improved workability, and greater reliability.
Summary Table:
Aspect | Details |
---|---|
Purpose | Relieve internal stresses, increase ductility, and improve workability. |
Common Materials | Steel, alloy steel, aluminum, brass, and copper. |
Process Steps | Heating, holding, and slow cooling. |
Key Benefits | Enhanced machinability, improved cold working, and dimensional stability. |
Applications | Manufacturing, construction, electronics, and automotive industries. |
Learn how annealing can optimize your metal components—contact our experts today!