Cold isostatic pressing (CIP) is a versatile manufacturing process used to form a wide range of products from various materials. It involves applying uniform pressure from all directions to a powder material contained within a flexible mold, resulting in high-density compacts with complex shapes. CIP is particularly valuable for materials that are difficult to process using traditional methods, such as high-temperature refractory materials, ceramics, cemented carbides, and rare metals. It is also used for large parts or components that do not require high precision in their final sintered state. The process is divided into wet bag and dry bag methods, each suited for specific applications. CIP is widely employed in industries such as aerospace, automotive, medical, and food processing, producing items like artificial bones, wear-resistant tools, and isotropic graphite.
Key Points Explained:
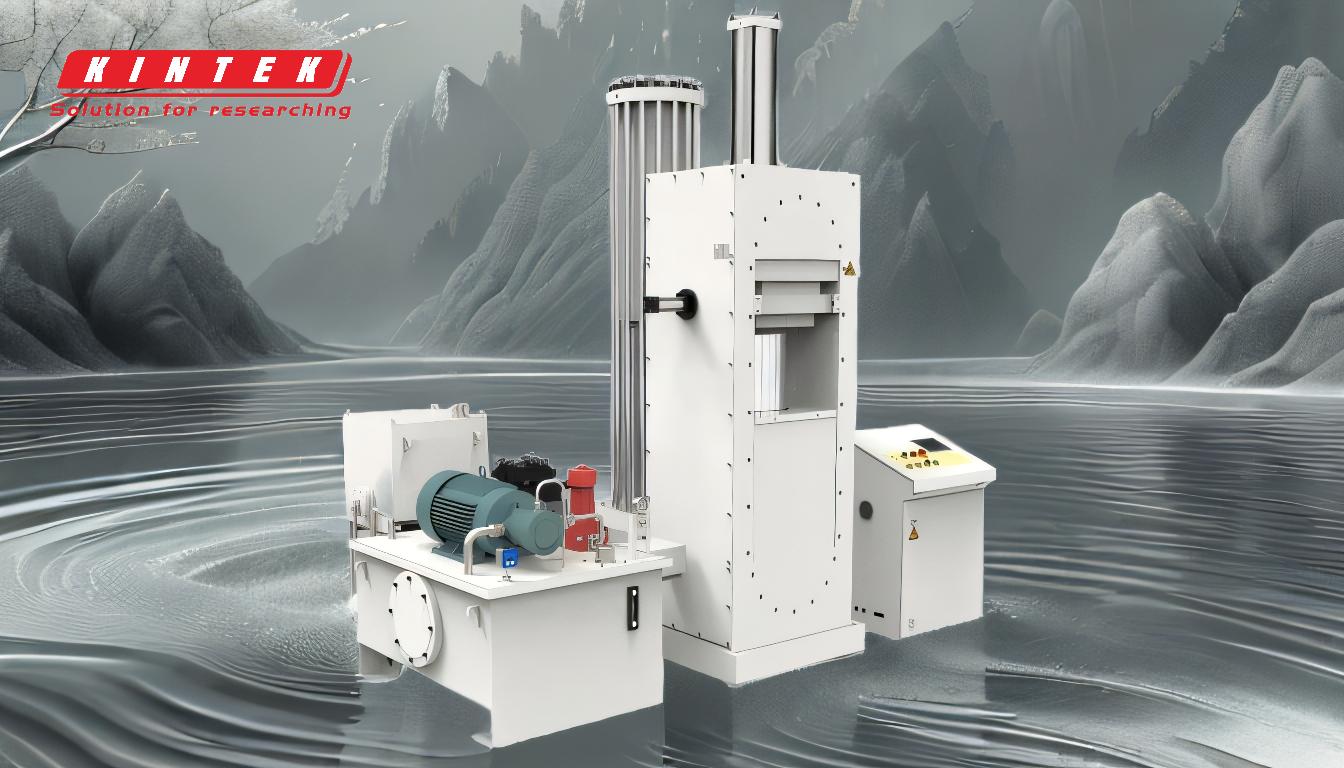
-
Materials Processed by CIP:
- Cold isostatic pressing is used to form a variety of materials, including:
- Refractory materials: High-temperature ceramics and insulators.
- Cemented carbides: Used in cutting tools and wear-resistant components.
- Isotropic graphite: Essential for applications requiring uniform properties in all directions.
- High-melting-point metals: Such as tungsten, which is pressed into various shapes.
- Ceramics: Including alumina (Al2O3), silicon nitride (Si3N4), silicon carbide (SiC), and sialons (Si-Al-O-N).
- Rare metal powders: Used in specialized applications like aerospace and electronics.
- Cold isostatic pressing is used to form a variety of materials, including:
-
Applications of CIP Products:
- Wear and metal-forming tools: CIP is ideal for producing durable tools that require high density and uniformity.
- Large parts: CIP is used for components that are too large for uniaxial presses and do not need high precision after sintering.
- Artificial bones: Medical applications benefit from CIP's ability to create biocompatible materials with complex shapes.
- Food processing: CIP is used to form certain food products, ensuring uniform density and texture.
-
CIP Methods:
- Wet bag method: The powder is encapsulated in a flexible mold and submerged in a pressurized liquid. This method is suitable for low-volume production and complex shapes.
- Dry bag method: The mold is fixed within the pressure vessel, making it more efficient for high-volume production of simpler shapes.
-
Advantages of CIP:
- Uniform density: The isostatic pressure ensures consistent density throughout the compact, reducing defects.
- Complex shapes: CIP can produce intricate geometries that are difficult to achieve with other methods.
- Material versatility: Almost any powder material can be processed using CIP, including ceramics, metals, and composites.
-
Industries Utilizing CIP:
- Aerospace: For components requiring high strength and thermal resistance.
- Automotive: For wear-resistant parts and tools.
- Medical: For biocompatible implants and prosthetics.
- Energy: For materials used in high-temperature environments, such as nuclear reactors.
-
Examples of CIP Products:
- Alumina spark-plug shells: Used in automotive engines for their thermal and electrical insulation properties.
- Tungsten components: Pressed into shapes for use in lighting, electronics, and aerospace.
- High alloy ferrous billets: Prepared for subsequent hot isostatic pressing (HIP) to achieve near-net-shape components.
In summary, cold isostatic pressing is a critical process for producing high-density, complex-shaped components from a wide range of materials. Its applications span multiple industries, making it a cornerstone of modern manufacturing for advanced materials and components.
Summary Table:
Category | Examples |
---|---|
Materials Processed | Refractory materials, cemented carbides, isotropic graphite, rare metals |
Applications | Wear-resistant tools, artificial bones, large parts, food processing |
CIP Methods | Wet bag (low-volume, complex shapes), dry bag (high-volume, simpler shapes) |
Industries | Aerospace, automotive, medical, energy |
Product Examples | Alumina spark-plug shells, tungsten components, high alloy ferrous billets |
Interested in leveraging cold isostatic pressing for your manufacturing needs? Contact us today to learn more!