Sintering is a versatile manufacturing process used to produce a wide range of products across various industries. It involves heating powdered materials below their melting points to form solid structures through particle bonding. This process is particularly useful for materials with high melting points, such as metals, ceramics, and polymers. Sintering is employed in industries like automotive, aerospace, electronics, biomedical, and additive manufacturing. Products made through sintering include automotive parts (gears, actuators), electrical components (switchgear), cutting tools (milling, drilling, reaming), aerospace components (fuel valve components, turbine blades), and biomedical implants (prosthetic joints). Additionally, sintering is used in the production of ceramics, refractory metals, and 3D-printed metal components.
Key Points Explained:
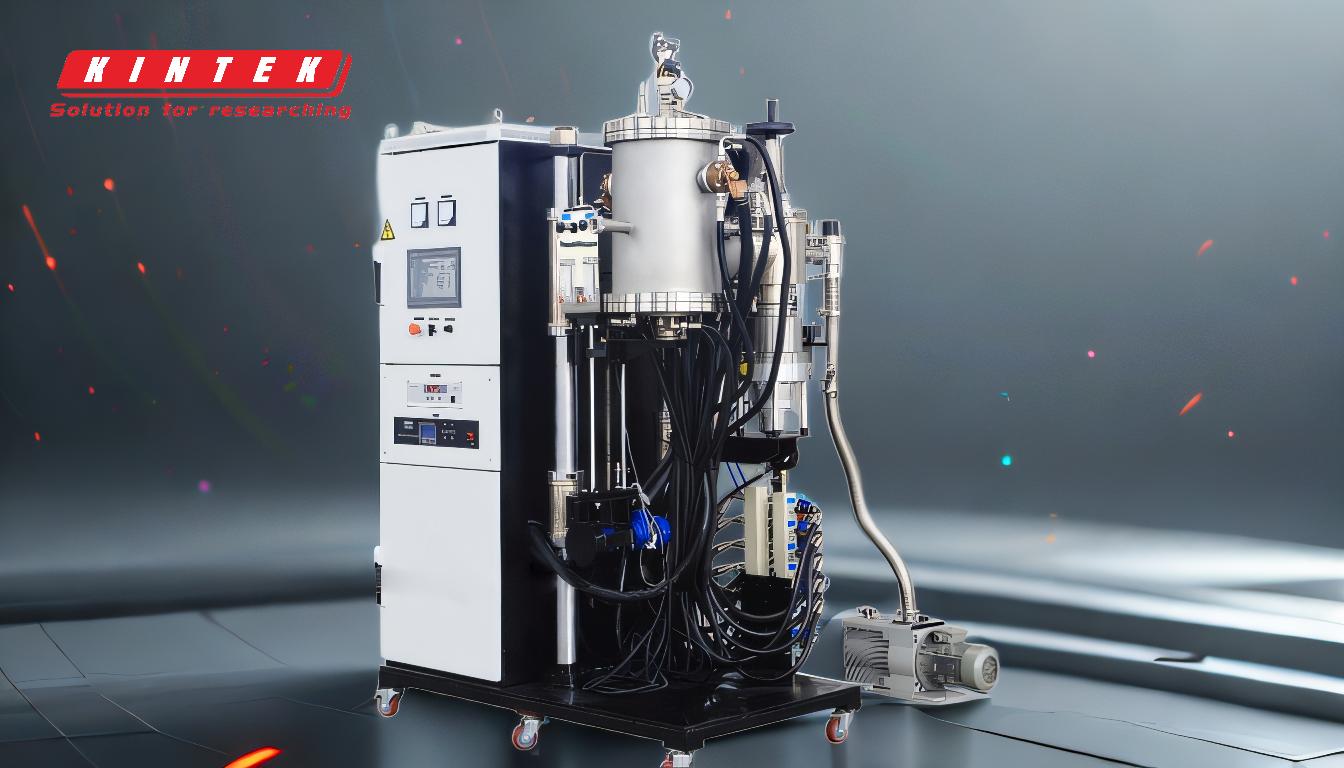
-
Automotive Industry:
- Gears and Actuators: Sintering is used to produce durable and precise automotive components like gears and actuators. These parts require high strength and wear resistance, which sintering effectively provides.
- Other Components: Sintering is also used for manufacturing pulleys, bearings, and other small, intricate parts that are essential for vehicle functionality.
-
Electrical and Electronics Industry:
- Switchgear: Sintered components are used in electrical switchgear due to their ability to withstand high electrical loads and thermal stress.
- Connectors and Contacts: Sintering is ideal for producing electrical connectors and contacts that require high conductivity and durability.
-
Cutting Tools:
- Milling, Drilling, and Reaming Tools: Sintering is widely used to manufacture cutting tools that require high hardness and wear resistance. These tools are essential in machining operations across various industries.
-
Aerospace Industry:
- Fuel Valve Components: Sintered parts are used in aerospace fuel systems due to their ability to withstand extreme temperatures and pressures.
- Actuators and Turbine Blades: Sintering is employed to produce lightweight yet strong components like actuators and turbine blades, which are critical for aircraft performance.
-
Biomedical Implants:
- Prosthetic Joints: Sintering is used to create biocompatible prosthetic joints and other implants. The process ensures that these components are strong, durable, and compatible with human tissue.
- Dental Implants: Sintered ceramics and metals are also used in dental implants due to their precision and biocompatibility.
-
Ceramics and Refractory Materials:
- Porcelain and Alumina: Sintering is essential in producing high-temperature ceramics like porcelain and alumina, which are used in applications requiring thermal and chemical resistance.
- Refractory Metals: Materials like tungsten and molybdenum, which have extremely high melting points, are sintered to form components used in high-temperature environments.
-
Additive Manufacturing (3D Printing):
- Metal 3D Printing: Sintering is a key process in metal 3D printing, where metal powders are sintered layer by layer to create complex, high-strength components.
- Rapid Prototyping: Sintering is used in rapid prototyping to quickly produce functional prototypes from polymer or metal powders.
-
Polymers and Filters:
- Polymer Components: Sintering is used to produce polymer components for various applications, including rapid prototyping and filter manufacturing.
- Filters: Sintered metal and polymer filters are used in industries like pharmaceuticals, food processing, and water treatment due to their fine porosity and durability.
-
Metal Powders and Alloys:
- Stainless Steel, Aluminum, Nickel, Copper, and Titanium Alloys: Sintering is used to process a wide range of metal powders, creating components with improved mechanical properties and precision. These materials are refined through sintering to meet the demands of advanced manufacturing techniques.
-
Advantages of Sintering:
- Material Efficiency: Sintering minimizes material waste by using powdered materials, making it a cost-effective manufacturing process.
- Complex Geometries: The process allows for the production of complex shapes and intricate designs that are difficult to achieve with traditional manufacturing methods.
- High Purity and Consistency: Sintering preserves the chemical composition and purity of materials, ensuring consistent quality in the final product.
In summary, sintering is a critical process in modern manufacturing, enabling the production of high-performance components across a wide range of industries. Its ability to work with diverse materials and produce complex, durable, and precise parts makes it indispensable in fields like automotive, aerospace, electronics, and biomedical engineering.
Summary Table:
Industry | Applications |
---|---|
Automotive | Gears, actuators, pulleys, bearings |
Electronics | Switchgear, connectors, contacts |
Cutting Tools | Milling, drilling, reaming tools |
Aerospace | Fuel valve components, turbine blades, actuators |
Biomedical | Prosthetic joints, dental implants |
Ceramics | Porcelain, alumina, refractory metals |
Additive Manufacturing | Metal 3D printing, rapid prototyping |
Polymers & Filters | Polymer components, sintered filters |
Metal Powders | Stainless steel, aluminum, nickel, copper, titanium alloys |
Interested in leveraging sintering for your manufacturing needs? Contact our experts today to learn more!