Hydraulic systems generate heat due to friction, fluid compression, and inefficiencies in the system. To maintain optimal performance and prevent damage, this heat must be effectively removed. Heat removal is typically achieved through cooling mechanisms such as heat exchangers, reservoir designs, and external cooling systems. These methods ensure that the hydraulic fluid operates within a safe temperature range, preventing overheating, fluid degradation, and component failure. Understanding the various cooling methods and their applications is crucial for maintaining the efficiency and longevity of hydraulic systems.
Key Points Explained:
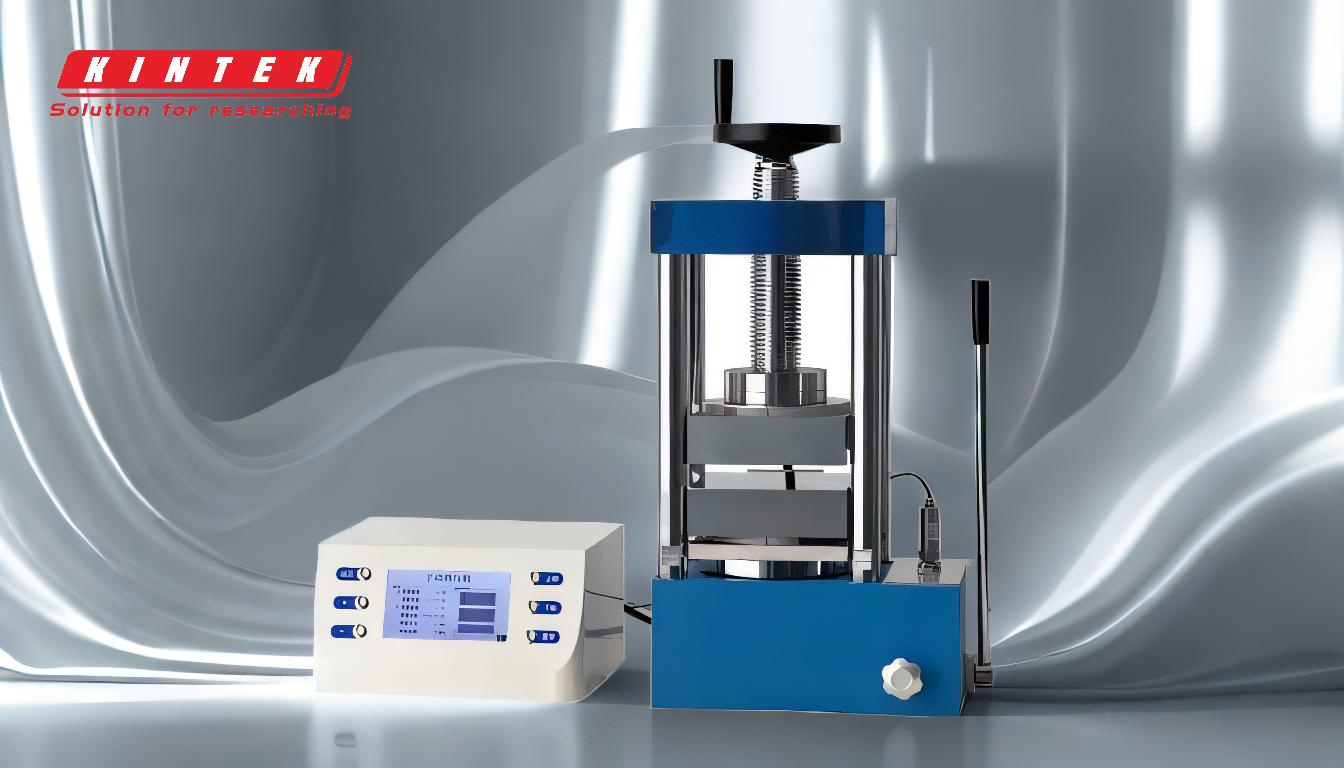
-
Heat Generation in Hydraulic Systems
- Hydraulic systems generate heat primarily through:
- Friction: Moving parts, such as pumps, valves, and actuators, create friction, which converts mechanical energy into heat.
- Fluid Compression: Hydraulic fluids compress under pressure, generating heat as a byproduct.
- Inefficiencies: Energy losses in the system, such as pressure drops and leakage, also contribute to heat buildup.
- Excessive heat can degrade hydraulic fluid, reduce system efficiency, and damage components, making heat removal essential.
- Hydraulic systems generate heat primarily through:
-
Role of Heat Exchangers
- Heat exchangers are the most common method for removing heat from hydraulic fluid. They transfer heat from the fluid to a cooling medium, such as air or water.
-
Types of Heat Exchangers:
- Air-Cooled Heat Exchangers: Use fans to blow air over finned tubes, cooling the fluid. These are commonly used in mobile and industrial applications.
- Water-Cooled Heat Exchangers: Use water as the cooling medium, which is more efficient than air cooling. These are often used in high-power systems or where space is limited.
- Proper sizing and placement of heat exchangers are critical to ensure effective heat dissipation.
-
Reservoir Design for Heat Dissipation
- The hydraulic reservoir plays a key role in heat removal. A well-designed reservoir allows the fluid to cool naturally by:
- Increasing the surface area exposed to air.
- Using baffles to improve fluid circulation and prevent localized hot spots.
- Incorporating cooling fins or external cooling systems for additional heat dissipation.
- Reservoirs should be sized appropriately to provide sufficient cooling capacity for the system.
- The hydraulic reservoir plays a key role in heat removal. A well-designed reservoir allows the fluid to cool naturally by:
-
External Cooling Systems
- In high-power or high-temperature applications, external cooling systems may be required. These include:
- Chillers: Use refrigeration cycles to cool the hydraulic fluid to a specific temperature.
- Cooling Towers: Circulate water to remove heat from the system.
- Oil-to-Water Heat Exchangers: Transfer heat from the hydraulic fluid to a water circuit for efficient cooling.
- These systems are often used in industrial settings where heat loads are significant.
- In high-power or high-temperature applications, external cooling systems may be required. These include:
-
Fluid Selection and Maintenance
- The choice of hydraulic fluid can impact heat removal. High-quality fluids with good thermal stability and viscosity properties can better withstand high temperatures.
- Regular maintenance, such as fluid replacement and system cleaning, ensures that the hydraulic system operates efficiently and minimizes heat generation.
-
System Design Considerations
- Proper system design is essential for effective heat removal. Key considerations include:
- Minimizing pressure drops and fluid leakage to reduce heat generation.
- Ensuring adequate flow rates and fluid circulation to distribute heat evenly.
- Incorporating temperature sensors and control systems to monitor and regulate fluid temperature.
- Proper system design is essential for effective heat removal. Key considerations include:
By implementing these heat removal strategies, hydraulic systems can maintain optimal operating temperatures, ensuring reliable performance and extending the lifespan of components.
Summary Table:
Cooling Method | Description | Applications |
---|---|---|
Heat Exchangers | Transfer heat from hydraulic fluid to air or water. | Mobile, industrial, and high-power systems. |
Reservoir Design | Uses surface area, baffles, and cooling fins for natural heat dissipation. | General hydraulic systems. |
External Cooling Systems | Includes chillers, cooling towers, and oil-to-water heat exchangers. | High-power or high-temperature industrial applications. |
Fluid Selection | High-quality fluids with thermal stability and viscosity properties. | All hydraulic systems. |
System Design | Minimizes heat generation through efficient flow rates and temperature control. | Customized hydraulic systems. |
Need help optimizing your hydraulic system's cooling? Contact our experts today for tailored solutions!