Chemical vapor deposition (CVD) is a versatile and widely used technique for depositing thin films and coatings onto substrates. The choice of substrate in CVD is critical as it directly influences the quality, adhesion, and properties of the deposited material. Substrates must be carefully selected based on their thermal, chemical, and structural compatibility with the deposition process and the desired end product. Commonly used substrates include metals like copper, cobalt, and nickel, which are particularly effective for graphene production due to their catalytic properties. Additionally, substrates must withstand the high temperatures and reactive environments typical of CVD processes. The selection of a substrate depends on the specific application, such as electronics, optics, or nanotechnology, and the material being deposited.
Key Points Explained:
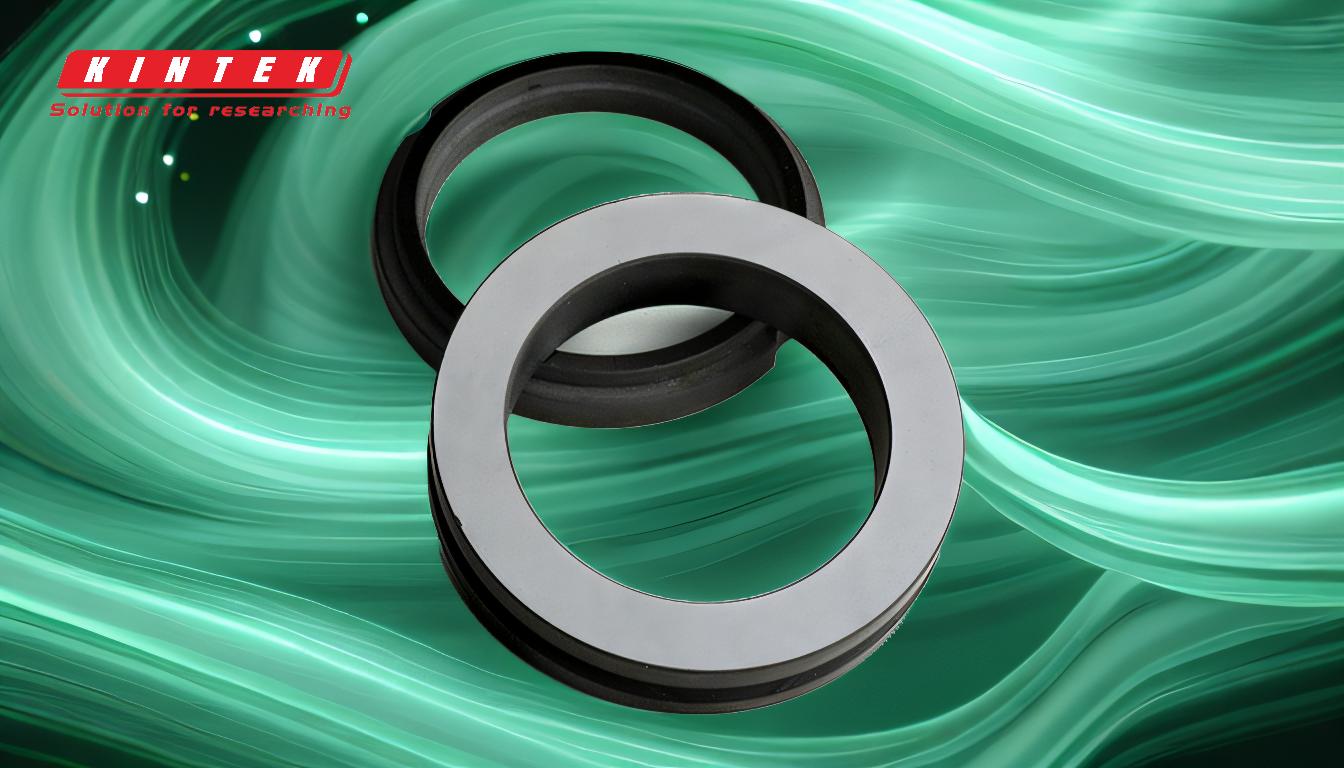
-
Role of Substrates in CVD:
- Substrates act as the foundation for thin-film deposition in CVD. They provide a surface where chemical reactions occur, leading to the formation of the desired material.
- The substrate's properties, such as thermal stability, surface roughness, and chemical reactivity, significantly influence the quality and uniformity of the deposited film.
-
Common Substrates Used in CVD:
- Metals: Copper, cobalt, and nickel are widely used, especially for graphene production. These metals act as catalysts, enabling the formation of single- and multi-layer graphene films.
- Silicon: Often used in semiconductor manufacturing due to its compatibility with electronic applications.
- Glass and Ceramics: Used in optical and protective coating applications due to their transparency and thermal stability.
- Polymers: Used in flexible electronics and coatings, but they require lower deposition temperatures to avoid degradation.
-
Substrate Selection Criteria:
- Thermal Stability: Substrates must withstand the high temperatures (often exceeding 500°C) required for CVD processes without degrading or warping.
- Chemical Compatibility: The substrate should not react with the precursor gases or by-products, which could lead to contamination or poor adhesion.
- Surface Properties: A smooth and clean surface ensures uniform deposition and strong adhesion of the film.
- Catalytic Activity: For certain applications, such as graphene growth, the substrate must have catalytic properties to facilitate the desired chemical reactions.
-
Applications and Substrate-Specific Considerations:
- Graphene Production: Copper and nickel are preferred due to their ability to catalyze the decomposition of carbon precursors and support the growth of high-quality graphene layers.
- Semiconductors: Silicon wafers are the standard substrate for electronic devices due to their excellent electrical properties and compatibility with microfabrication processes.
- Optical Coatings: Glass and quartz are used for their transparency and ability to withstand high temperatures during deposition.
- Protective Coatings: Metals and ceramics are chosen for their durability and resistance to wear and corrosion.
-
Challenges in Substrate Usage:
- Thermal Expansion Mismatch: Differences in thermal expansion coefficients between the substrate and the deposited material can lead to stress and cracking.
- Surface Contamination: Impurities on the substrate surface can interfere with film growth, necessitating thorough cleaning and preparation.
- Cost and Availability: Some high-performance substrates, such as single-crystal sapphire, can be expensive and difficult to source.
-
Future Trends in CVD Substrates:
- Flexible Substrates: With the rise of flexible electronics, there is growing interest in using polymer-based substrates that can withstand lower deposition temperatures.
- Composite Materials: Combining different materials to create substrates with tailored properties, such as enhanced thermal conductivity or mechanical strength.
- Nanostructured Substrates: Using substrates with engineered surface features to control film growth at the nanoscale, enabling advanced applications in nanotechnology.
In conclusion, the choice of substrate in CVD is a critical factor that determines the success of the deposition process. By carefully considering the substrate's properties and compatibility with the deposition environment, manufacturers can achieve high-quality films tailored to specific applications. As technology advances, new substrate materials and designs will continue to expand the capabilities of CVD in fields such as electronics, optics, and nanotechnology.
Summary Table:
Substrate Type | Key Applications | Properties |
---|---|---|
Metals (Copper, Cobalt, Nickel) | Graphene production, catalytic films | High thermal stability, catalytic activity |
Silicon | Semiconductors, electronics | Excellent electrical properties, compatibility with microfabrication |
Glass and Ceramics | Optical coatings, protective layers | Transparency, thermal stability |
Polymers | Flexible electronics, low-temperature coatings | Flexibility, low thermal tolerance |
Need help selecting the right substrate for your CVD process? Contact our experts today!