Hydraulic systems are critical components in many industrial and mobile applications, and the temperature of hydraulic oil plays a significant role in their performance and longevity. The ideal operating temperature for hydraulic oil typically ranges between 100°F (38°C) and 140°F (60°C). However, temperatures exceeding 180°F (82°C) are considered too hot and can lead to accelerated degradation of the oil, reduced efficiency, and potential damage to system components. At such high temperatures, the oil's viscosity decreases, leading to poor lubrication, increased wear, and potential system failure. Understanding the temperature limits and implementing proper cooling and maintenance practices are essential to ensure the reliability and efficiency of hydraulic systems.
Key Points Explained:
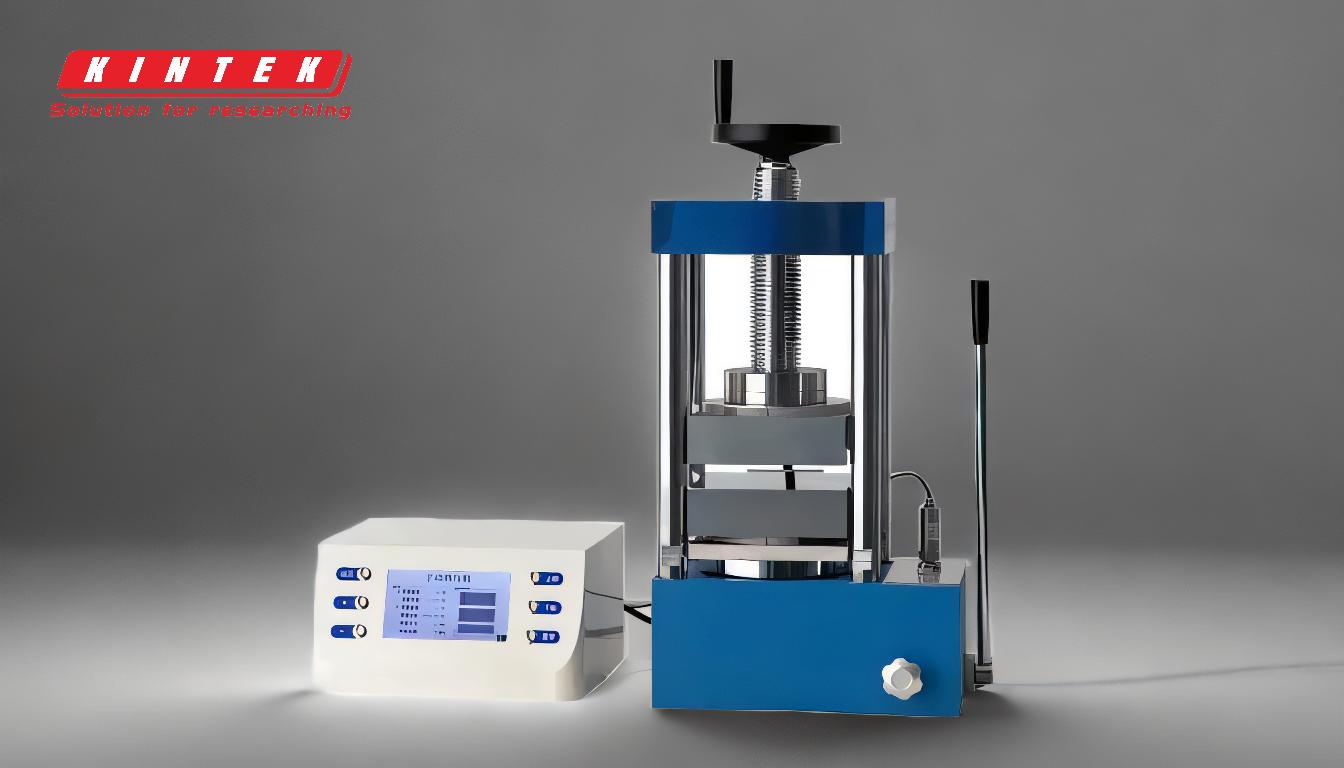
-
Ideal Operating Temperature Range:
- Hydraulic oil performs optimally within a temperature range of 100°F (38°C) to 140°F (60°C). This range ensures proper viscosity, lubrication, and efficient heat dissipation.
- Operating within this range helps maintain the oil's chemical stability and prevents premature degradation.
-
Temperature Thresholds:
- 180°F (82°C): This is generally considered the upper limit for hydraulic oil. Beyond this temperature, the oil begins to degrade rapidly, losing its lubricating properties and increasing the risk of system failure.
- 200°F (93°C): At this temperature, the oil's oxidation rate accelerates significantly, leading to sludge formation, varnish deposits, and reduced system efficiency.
- 240°F (116°C): At such extreme temperatures, hydraulic oil can break down completely, causing severe damage to system components and potentially leading to catastrophic failure.
-
Consequences of Excessive Heat:
- Viscosity Breakdown: High temperatures cause the oil to thin out, reducing its ability to lubricate moving parts effectively. This can lead to increased friction, wear, and potential component failure.
- Oxidation and Degradation: Elevated temperatures accelerate the oxidation process, leading to the formation of acids, sludge, and varnish. These by-products can clog filters, valves, and other critical components, reducing system efficiency and increasing maintenance costs.
- Seal and Hose Damage: Excessive heat can cause seals and hoses to harden, crack, or fail, leading to leaks and potential system contamination.
- Reduced System Efficiency: High temperatures reduce the overall efficiency of the hydraulic system, leading to increased energy consumption and reduced performance.
-
Causes of Overheating:
- Inadequate Cooling: Insufficient cooling capacity or malfunctioning cooling systems can lead to overheating. Regular maintenance and proper sizing of cooling components are essential to prevent this issue.
- High Ambient Temperatures: Operating hydraulic systems in hot environments without adequate cooling can lead to overheating. It's important to consider the operating environment when designing and maintaining hydraulic systems.
- Excessive Load: Overloading the hydraulic system can generate excessive heat, leading to overheating. Ensuring that the system is properly sized for the intended load is crucial.
- Contaminated Oil: Contaminants in the hydraulic oil can increase friction and generate heat. Regular oil analysis and filtration are necessary to maintain oil cleanliness.
-
Preventive Measures:
- Regular Maintenance: Routine inspection and maintenance of hydraulic systems, including oil analysis, filter changes, and cooling system checks, can help prevent overheating.
- Proper Cooling: Ensuring that the hydraulic system has adequate cooling capacity, such as using heat exchangers or coolers, is essential to maintain optimal operating temperatures.
- Oil Selection: Choosing the right hydraulic oil with the appropriate viscosity and thermal stability for the specific application can help mitigate the effects of high temperatures.
- System Design: Properly designing the hydraulic system, including the selection of components and the layout, can help minimize heat generation and ensure efficient heat dissipation.
-
Monitoring and Control:
- Temperature Sensors: Installing temperature sensors and monitoring systems can help detect overheating early and allow for timely intervention.
- Automatic Shutdown: Implementing automatic shutdown systems that activate when the oil temperature exceeds safe limits can prevent catastrophic failure.
- Thermal Relief Valves: Using thermal relief valves can help manage pressure and temperature spikes, protecting the system from damage.
In conclusion, maintaining the hydraulic oil temperature within the recommended range is crucial for the efficient and reliable operation of hydraulic systems. Exceeding the temperature limits can lead to severe consequences, including oil degradation, component failure, and reduced system efficiency. By understanding the temperature thresholds, identifying the causes of overheating, and implementing preventive measures, operators can ensure the longevity and performance of their hydraulic systems.
Summary Table:
Temperature | Impact on Hydraulic Oil |
---|---|
100°F (38°C) - 140°F (60°C) | Optimal operating range for viscosity, lubrication, and heat dissipation. |
180°F (82°C) | Upper limit; oil begins to degrade, increasing failure risk. |
200°F (93°C) | Oxidation accelerates, leading to sludge, varnish, and reduced efficiency. |
240°F (116°C) | Extreme breakdown; severe damage to components and potential catastrophic failure. |
Ensure your hydraulic system operates efficiently—contact our experts today for tailored solutions!