When brazing cast iron, preheating is a critical step to ensure proper bonding and to prevent cracking due to thermal stress. The recommended preheating temperature for cast iron typically ranges between 250°F (120°C) and a dull red color, which is approximately 1200°F (650°C). The exact temperature depends on the size of the part, the type of brazing material, and the specific application. Smaller parts can often be preheated in a conventional oven, while larger parts may require localized heating using tools like an oxy-fuel or LPG burner torch. Gradual and indirect preheating is essential to avoid thermal shock and ensure even heat distribution.
Key Points Explained:
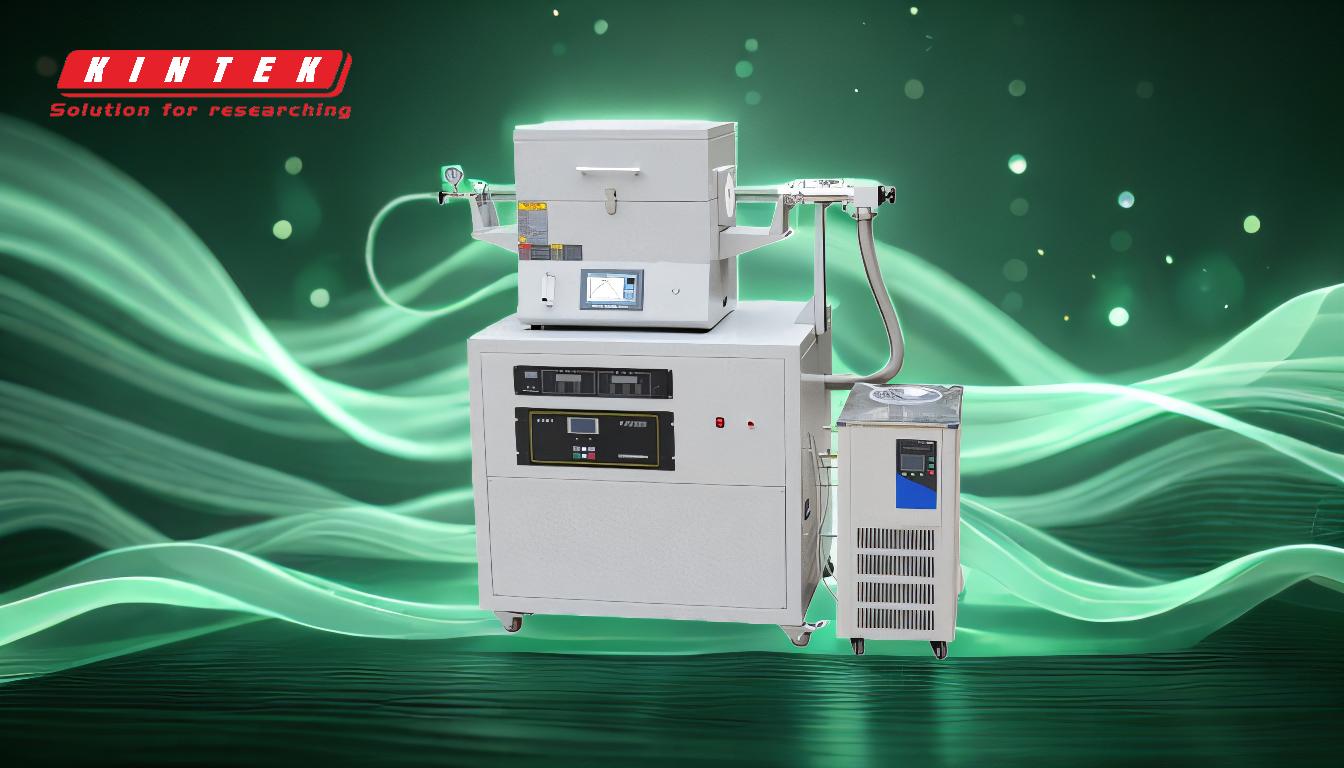
-
Preheating Temperature Range:
- The general preheating temperature for cast iron brazing ranges from 250°F (120°C) to a dull red color (approximately 1200°F or 650°C).
- This range ensures the material is sufficiently heated to allow proper brazing without causing thermal stress or cracking.
-
Importance of Gradual Preheating:
- Preheating should be done gradually to avoid thermal shock, which can lead to cracking in cast iron.
- Indirect preheating, where surrounding areas are also heated, helps distribute heat evenly and reduces the risk of localized stress.
-
Methods of Preheating:
- Small Parts: Can be preheated in a conventional oven, which provides controlled and even heating.
- Large Parts: Require localized heating methods such as an oxy-fuel torch or LPG burner torch. These tools allow for targeted heating of specific areas.
-
Visual Cue for Preheating:
- A dull red color is a visual indicator that the cast iron has reached an appropriate preheating temperature. This color corresponds to a temperature of around 1200°F (650°C) and ensures the material is ready for brazing.
-
Electrode Considerations:
- When welding cast iron, preheating to at least 250°F (120°C) is recommended if using cast iron or copper electrodes.
- Nickel electrodes, however, can often be used without preheating, making them a convenient option for certain applications.
-
Application-Specific Adjustments:
- The exact preheating temperature and method may vary depending on the size of the cast iron part, the type of brazing material, and the specific requirements of the job. Always consider the manufacturer's guidelines and the specific conditions of the application.
By following these guidelines, you can ensure a successful brazing process for cast iron, minimizing the risk of defects and achieving a strong, durable bond.
Summary Table:
Key Factor | Details |
---|---|
Preheating Temperature | 250°F (120°C) to 1200°F (650°C), depending on part size and brazing material. |
Gradual Preheating | Essential to avoid thermal shock and ensure even heat distribution. |
Small Parts Preheating | Use a conventional oven for controlled, even heating. |
Large Parts Preheating | Use oxy-fuel or LPG burner torches for localized heating. |
Visual Cue | A dull red color indicates ~1200°F (650°C), the optimal preheating point. |
Electrode Considerations | Preheat to 250°F (120°C) for cast iron/copper electrodes; nickel often needs no preheating. |
Application-Specific Tips | Adjust based on part size, brazing material, and job requirements. |
Need help with cast iron brazing? Contact our experts today for tailored solutions!