Sintering is a thermal process that involves heating powdered materials to temperatures below their melting point to bond particles together, resulting in a solid structure. The temperature at which sintering occurs varies significantly depending on the material, desired characteristics, and specific application. Generally, sintering temperatures range from 750°C to 1800°C, with some processes requiring even higher temperatures. The choice of temperature is influenced by factors such as the material's properties, the presence of shielding gases, and the need to prevent oxidation or contamination. For instance, metals like copper and bronze may sinter at lower temperatures with the use of refractory ballasts, while advanced ceramics or dental materials often require higher temperatures (1200°C to 1400°C). Additionally, sintering can occur at lower temperatures if sufficient pressure is applied, though this is less common. The process is typically conducted in controlled environments, such as continuous furnaces, to ensure consistent temperature and atmosphere management.
Key Points Explained:
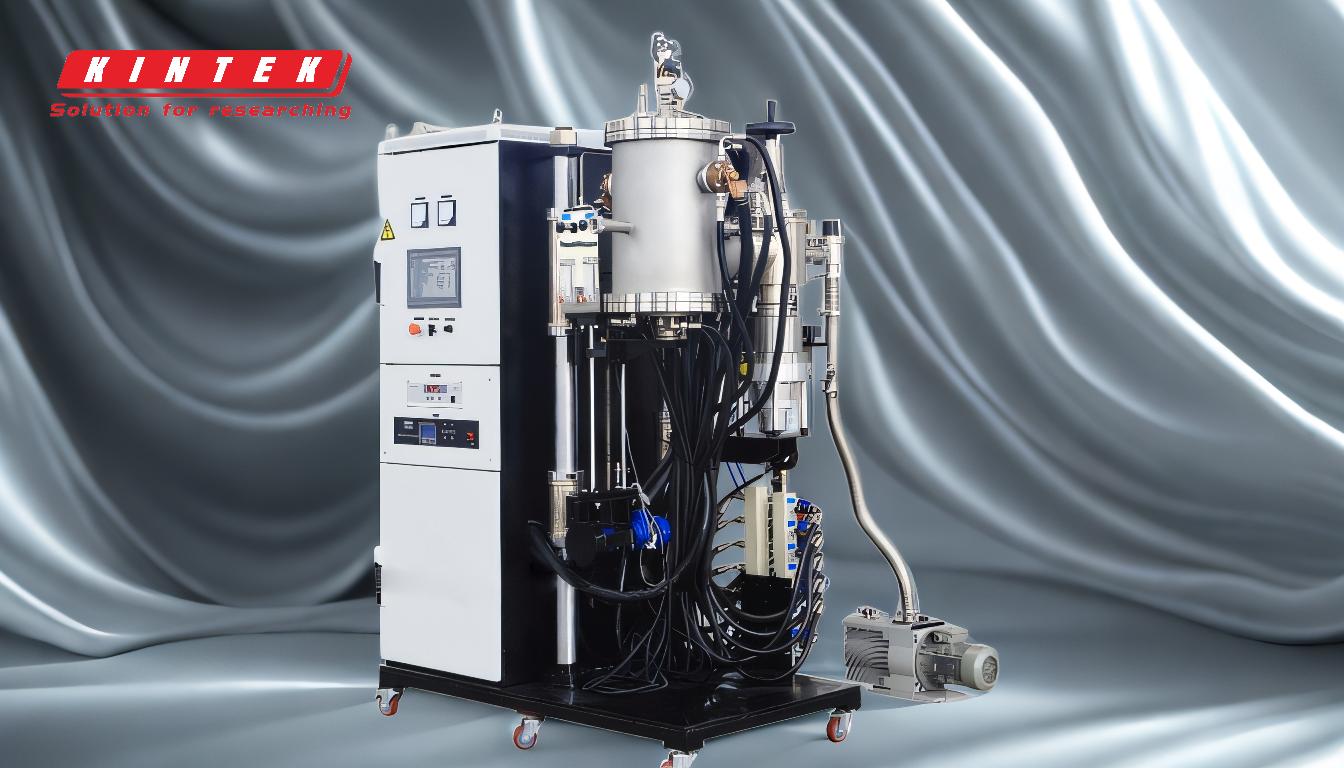
-
General Temperature Range for Sintering:
- Sintering typically occurs between 750°C and 1300°C for most materials, though this range can extend up to 1800°C or higher for specialized applications.
- The exact temperature depends on the material being sintered and the desired properties of the final product.
-
Material-Specific Sintering Temperatures:
- Metals: Pure metals, especially those sintered in a vacuum or with shielding gases, often require temperatures between 750°C and 1300°C.
- Dental Materials: Dental sintering furnaces operate at higher temperatures, typically ranging from 1200°C to 1400°C.
- Advanced Ceramics and Powders: Some powdered materials may require sintering at temperatures above 1800°C, particularly in specialized applications.
-
Role of Pressure in Sintering:
- Sintering can occur at lower temperatures if sufficient pressure is applied. This is particularly useful for materials that are sensitive to high temperatures or for processes requiring densification without melting.
-
Importance of Atmosphere Control:
- Sintering often requires a controlled atmosphere to prevent oxidation or contamination. Shielding gases, such as endothermic gas, are commonly used in atmospheric pressure sintering.
- For metals like copper and bronze, refractory ballasts (e.g., Al2O3) are used to support the shape of the part, while Sintering Carbon helps manage oxygen exposure.
-
Critical Temperature Zones:
- From room temperature to 900°C, there is little effect on the material. However, the ramp rate (heating rate) from 900°C to the top temperature, the consistency of temperature during the hold time, and the cooling rate back to about 900°C are critical for achieving optimal results.
-
Sintering in Specialized Applications:
- In experiments or advanced manufacturing processes, sintering temperatures can reach 1800°C or higher, depending on the material and desired characteristics.
- The process is often conducted in continuous furnaces to maintain precise control over temperature and atmosphere.
-
Influence of Material Properties:
- The sintering temperature is heavily influenced by the melting point and thermal stability of the material. Materials with higher melting points generally require higher sintering temperatures.
-
Trade-offs in Sintering Temperature:
- Higher sintering temperatures can lead to better particle bonding and densification but may also increase the risk of material degradation or warping.
- Lower temperatures, when combined with pressure, can achieve similar results while minimizing thermal stress.
By understanding these key points, purchasers and engineers can make informed decisions about the sintering process, ensuring optimal results for their specific materials and applications.
Summary Table:
Material Type | Sintering Temperature Range | Key Considerations |
---|---|---|
Metals | 750°C to 1300°C | Requires shielding gases or vacuum; refractory ballasts may be used. |
Dental Materials | 1200°C to 1400°C | High precision and controlled atmosphere are critical. |
Advanced Ceramics | Up to 1800°C or higher | Specialized applications; continuous furnaces ensure precise temperature control. |
Pressure-Assisted | Lower than standard range | Useful for sensitive materials; minimizes thermal stress. |
Need help selecting the right sintering temperature for your materials? Contact our experts today for personalized advice!