Diamond-like carbon (DLC) coatings are typically applied at relatively low temperatures compared to other coating processes, making them suitable for a wide range of substrates, including temperature-sensitive materials. The deposition temperature for DLC coatings generally ranges between 100°C to 300°C, depending on the specific deposition method and the desired properties of the coating. This low-temperature application is one of the key advantages of DLC, as it minimizes thermal stress and distortion in the substrate. The process often involves techniques such as plasma-enhanced chemical vapor deposition (PECVD) or physical vapor deposition (PVD), which allow for precise control over the coating's properties, including hardness, friction coefficient, and adhesion.
Key Points Explained:
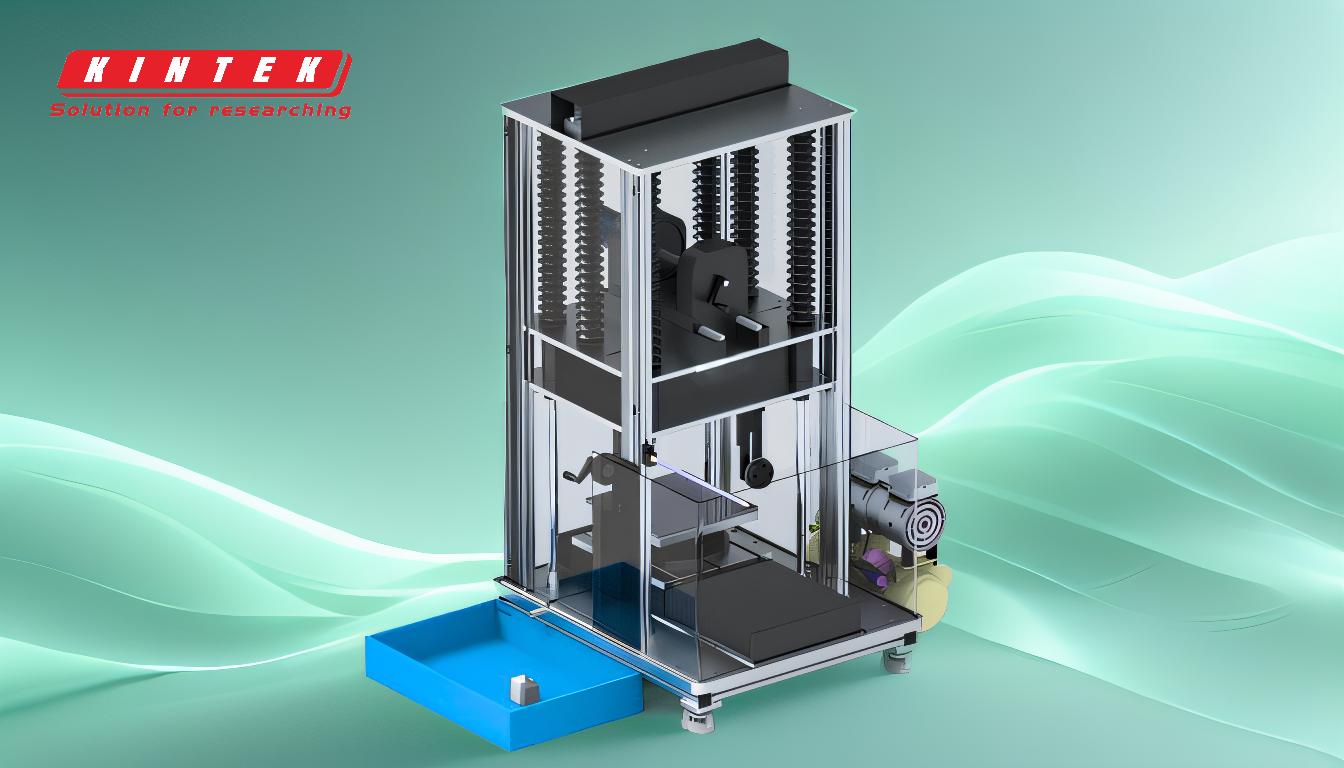
-
Temperature Range for DLC Deposition
- DLC coatings are applied at temperatures typically ranging from 100°C to 300°C.
- This range is significantly lower than many other coating processes, such as thermal spray or high-temperature CVD, which can exceed 800°C.
- The low-temperature deposition is crucial for substrates like plastics, polymers, or heat-treated metals, which may degrade or deform at higher temperatures.
-
Deposition Methods and Their Impact on Temperature
-
Plasma-Enhanced Chemical Vapor Deposition (PECVD):
- PECVD is the most common method for applying DLC coatings. It operates at relatively low temperatures (100°C–300°C) and uses plasma to activate the deposition process.
- This method allows for excellent control over the coating's properties, such as hardness and adhesion, while keeping the substrate temperature low.
-
Physical Vapor Deposition (PVD):
- PVD techniques, such as sputtering or arc evaporation, can also be used to deposit DLC coatings. These methods typically operate at slightly higher temperatures (200°C–300°C) but still remain within the safe range for most substrates.
-
Plasma-Enhanced Chemical Vapor Deposition (PECVD):
-
Advantages of Low-Temperature Deposition
-
Substrate Compatibility:
- The low-temperature process makes DLC suitable for a wide variety of substrates, including metals, ceramics, and polymers.
-
Minimized Thermal Stress:
- By avoiding high temperatures, DLC coatings reduce the risk of thermal distortion, warping, or degradation of the substrate material.
-
Enhanced Adhesion:
- Lower temperatures help maintain the integrity of the substrate-coating interface, improving adhesion and overall performance.
-
Substrate Compatibility:
-
Factors Influencing Deposition Temperature
-
Substrate Material:
- The thermal stability of the substrate material plays a significant role in determining the maximum allowable deposition temperature. For example, polymers may require temperatures below 150°C, while metals can tolerate higher temperatures.
-
Coating Properties:
- The desired properties of the DLC coating, such as hardness, friction coefficient, or wear resistance, may influence the deposition temperature. Higher temperatures can sometimes improve coating density and adhesion but must be balanced against substrate limitations.
-
Deposition Technique:
- Different techniques (e.g., PECVD vs. PVD) have varying temperature requirements and capabilities, which must be considered when selecting the appropriate method.
-
Substrate Material:
-
Applications of DLC Coatings
- DLC coatings are widely used in industries such as automotive, aerospace, medical devices, and consumer electronics due to their excellent wear resistance, low friction, and biocompatibility.
- The ability to apply these coatings at low temperatures is particularly beneficial for components like plastic gears, medical implants, and precision-engineered parts, where high-temperature processes could cause damage.
-
Challenges and Considerations
-
Adhesion Issues:
- While low temperatures are advantageous, they can sometimes lead to weaker adhesion between the coating and the substrate. Proper surface preparation, such as cleaning and etching, is critical to ensure strong bonding.
-
Uniformity and Thickness Control:
- Achieving uniform coating thickness and properties can be challenging at lower temperatures, requiring precise control of deposition parameters.
-
Cost and Complexity:
- The equipment and processes for low-temperature DLC deposition can be more complex and costly compared to higher-temperature methods, but the benefits often justify the investment.
-
Adhesion Issues:
By understanding the temperature requirements and deposition methods for DLC coatings, manufacturers can select the optimal process for their specific application, ensuring high performance and durability while protecting the integrity of the substrate.
Summary Table:
Aspect | Details |
---|---|
Temperature Range | 100°C to 300°C |
Deposition Methods | PECVD (100°C–300°C), PVD (200°C–300°C) |
Advantages | Substrate compatibility, minimized thermal stress, enhanced adhesion |
Key Applications | Automotive, aerospace, medical devices, consumer electronics |
Challenges | Adhesion issues, uniformity control, cost and complexity of equipment |
Optimize your coating process with DLC—contact our experts today for tailored solutions!