Brazing stainless steel requires careful preparation and precise temperature control to ensure a strong and durable joint. The process involves cleaning the surfaces to remove contaminants, selecting the appropriate filler metal, and heating the assembly to the correct brazing temperature. The temperature needed for brazing stainless steel typically ranges between 600°C and 1200°C, depending on the filler metal used and the specific type of stainless steel. Common methods include flame, induction, or furnace heating, with vacuum or controlled atmospheres often used to prevent oxidation. Proper inspection of the brazed joint is essential to ensure quality.
Key Points Explained:
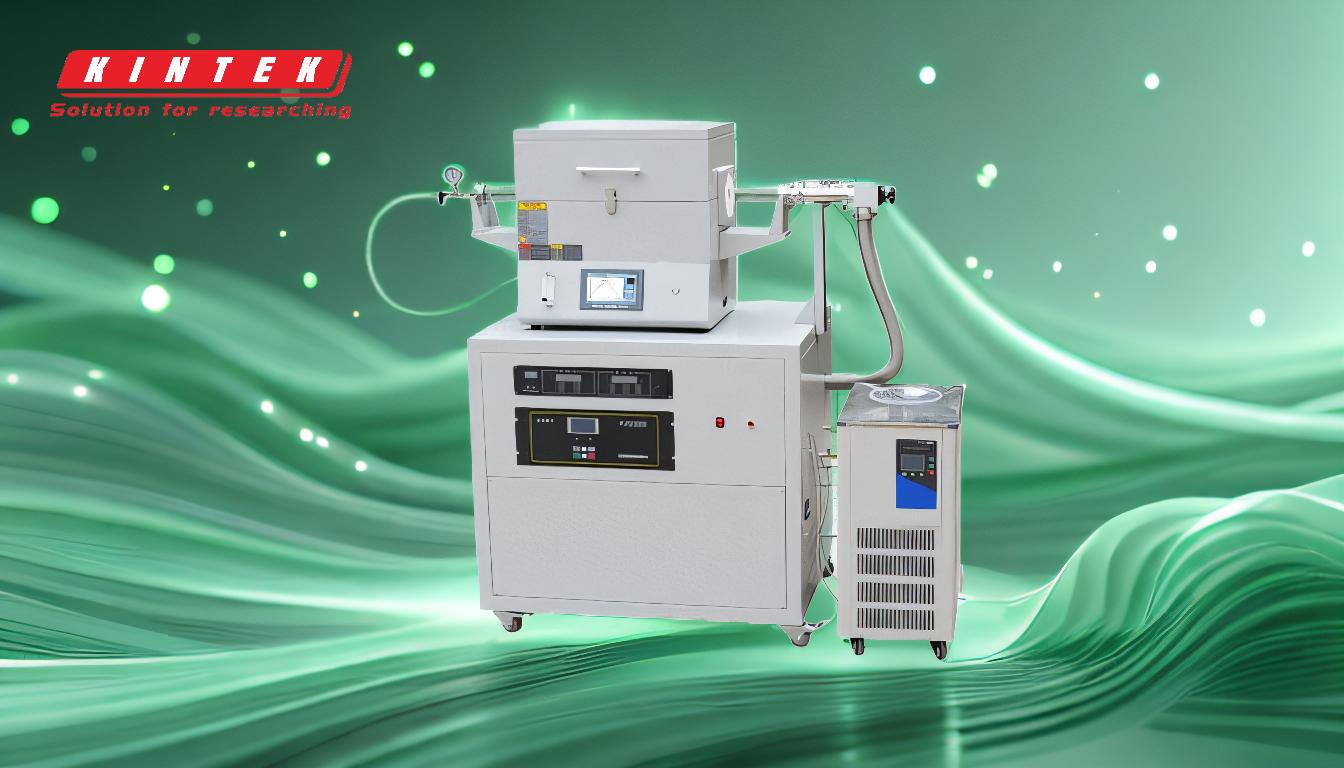
-
Preparation Before Brazing:
- Cleaning: Before brazing, stainless steel must be thoroughly cleaned to remove grease, oil, and other contaminants. This ensures proper wetting and bonding of the filler metal. Cleaning methods include degreasing, pickling, and mechanical abrasion.
- Immediate Brazing: After cleaning, brazing should be performed as soon as possible to prevent recontamination or oxidation of the surfaces.
-
Brazing Temperature Range:
- The brazing temperature for stainless steel typically ranges between 600°C and 1200°C, depending on the filler metal and the specific stainless steel alloy. For example:
- Silver-based filler metals: Typically require temperatures around 600°C to 800°C.
- Copper-based filler metals: Require higher temperatures, usually between 1080°C and 1200°C.
- Nickel-based filler metals: Often used for high-temperature applications, requiring temperatures above 1000°C.
- The brazing temperature for stainless steel typically ranges between 600°C and 1200°C, depending on the filler metal and the specific stainless steel alloy. For example:
-
Filler Metals:
- The choice of filler metal depends on the application and the properties required for the joint. Commonly used filler metals include:
- Silver-based alloys: Suitable for general-purpose brazing with good strength and corrosion resistance.
- Copper-based alloys: Ideal for high-temperature applications and vacuum brazing.
- Nickel-based alloys: Used for high-strength and high-temperature resistance.
- Manganese-based alloys: Offer good ductility and oxidation resistance.
- Precious metal alloys: Used in specialized applications requiring high purity and corrosion resistance.
- The choice of filler metal depends on the application and the properties required for the joint. Commonly used filler metals include:
-
Brazing Methods:
- Flame Brazing: Uses a gas torch to heat the joint and melt the filler metal. Suitable for small-scale or manual operations.
- Induction Brazing: Uses electromagnetic induction to heat the joint quickly and precisely. Ideal for high-volume production.
- Furnace Brazing: Involves heating the assembly in a controlled atmosphere or vacuum furnace. This method is suitable for complex or large assemblies and ensures uniform heating and minimal oxidation.
-
Atmosphere Control:
- Vacuum Brazing: Performed in a vacuum furnace to prevent oxidation and ensure a clean joint. Commonly used for high-precision applications.
- Controlled Atmospheres: Dry hydrogen or inert gases like argon are used to remove oxides and protect the joint during heating. Nickel plating can also be applied to facilitate wet hydrogen brazing.
-
Post-Brazing Inspection:
- After brazing, the joint must be inspected for defects such as voids, cracks, or incomplete bonding. Non-destructive testing methods like X-ray or ultrasonic inspection are commonly used to ensure the quality of the brazed joint.
By following these steps and adhering to the appropriate temperature range, stainless steel can be successfully brazed to create strong, reliable joints suitable for various applications.
Summary Table:
Aspect | Details |
---|---|
Temperature Range | 600°C to 1200°C, depending on filler metal and stainless steel type. |
Filler Metals | Silver-based (600°C–800°C), Copper-based (1080°C–1200°C), Nickel-based (above 1000°C). |
Brazing Methods | Flame, Induction, or Furnace heating with vacuum/controlled atmospheres. |
Atmosphere Control | Vacuum or inert gases (e.g., argon) to prevent oxidation. |
Post-Brazing Inspection | Non-destructive testing (e.g., X-ray, ultrasonic) to ensure joint quality. |
Need expert advice on brazing stainless steel? Contact us today for tailored solutions!