The temperature for Plasma Enhanced Chemical Vapor Deposition (PECVD) of silicon nitride typically ranges between 200°C and 400°C, although some processes may operate at temperatures as low as 80°C or as high as 540°C. This wide range is due to the flexibility of PECVD, which allows for lower temperatures compared to traditional CVD methods, making it suitable for temperature-sensitive substrates. The process involves vaporizing materials and depositing them onto a silicon wafer, producing dense and uniform thin-film membranes of silicon nitride. The low-temperature operation of PECVD minimizes substrate damage and allows for the deposition of a wide range of materials, including silicon nitride, without compromising film quality.
Key Points Explained:
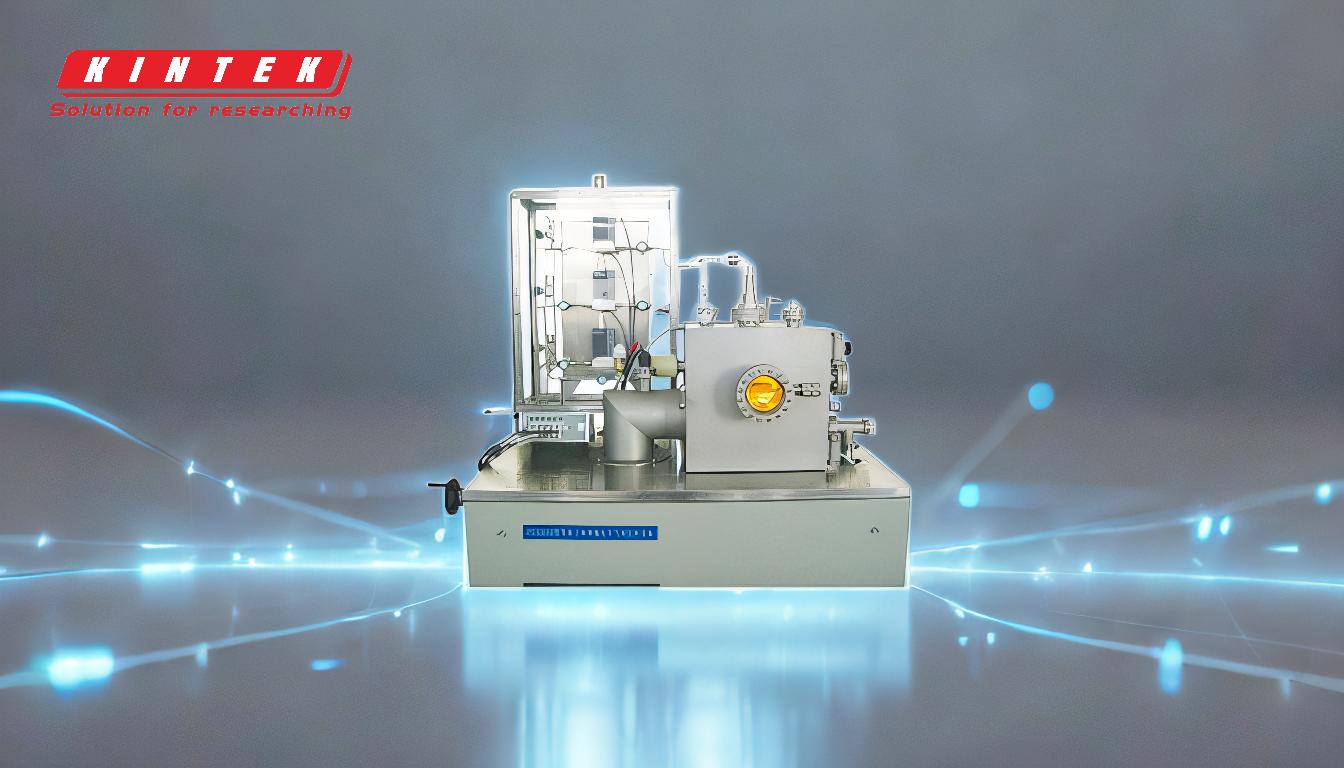
-
Typical Temperature Range for PECVD Silicon Nitride:
- PECVD silicon nitride is typically deposited at temperatures between 200°C and 400°C.
- This range is lower than traditional CVD methods, which often require temperatures above 700°C.
- The lower temperature range is advantageous for temperature-sensitive substrates, reducing the risk of thermal damage.
-
Flexibility in Temperature Operation:
- PECVD can operate at temperatures as low as 80°C and as high as 540°C, depending on the specific application and material requirements.
- For example, some processes may require room temperature deposition for highly sensitive materials or substrates.
-
Advantages of Low-Temperature PECVD:
- Reduced Substrate Damage: Lower temperatures minimize thermal stress and damage to the substrate, which is critical for delicate materials.
- Wide Material Compatibility: The ability to deposit at lower temperatures allows for the use of a broader range of materials, including polymers and other temperature-sensitive substrates.
- Uniform Film Deposition: The low-pressure environment (typically 0.1-10 Torr) in PECVD reduces scattering and promotes film uniformity, even at lower temperatures.
-
Chemical Reactions in PECVD Silicon Nitride Deposition:
- Silicon nitride is deposited using reactions such as:
- 3 SiH4 + 4 NH3 → Si3N4 + 12 H2
- 3 SiCl2H2 + 4 NH3 → Si3N4 + 6 HCl + 6 H2
- These reactions occur at the lower temperatures characteristic of PECVD, producing dense and uniform films.
- Silicon nitride is deposited using reactions such as:
-
Comparison with LPCVD:
- LPCVD (Low Pressure Chemical Vapor Deposition) typically operates at temperatures >700°C, which can result in films with higher tensile stress and hydrogen content (up to 8%).
- PECVD, on the other hand, produces films with less tensile stress and better mechanical properties, even though the electrical properties may be slightly inferior.
-
Applications of PECVD Silicon Nitride:
- PECVD silicon nitride is used in various applications, including:
- Thin-film membranes for MEMS (Micro-Electro-Mechanical Systems).
- Insulating layers in semiconductor devices.
- Protective coatings for sensitive electronic components.
- PECVD silicon nitride is used in various applications, including:
-
Process Parameters and Their Impact:
- Pressure: PECVD typically operates at low pressures (0.1-10 Torr), which helps in reducing scattering and achieving uniform film deposition.
- Temperature Control: Precise temperature control is crucial to ensure the desired film properties, such as density, uniformity, and stress levels.
-
Challenges and Considerations:
- While PECVD offers lower temperature deposition, it may result in films with worse electrical properties compared to LPCVD.
- The choice of temperature and process parameters must balance the need for low-temperature deposition with the desired film properties for the specific application.
In summary, PECVD silicon nitride is typically deposited at temperatures between 200°C and 400°C, with the flexibility to operate at lower or higher temperatures depending on the application. This process offers significant advantages in terms of reduced substrate damage, wide material compatibility, and uniform film deposition, making it a preferred method for many applications in semiconductor and MEMS technologies.
Summary Table:
Aspect | Details |
---|---|
Typical Temperature Range | 200°C–400°C |
Flexible Range | 80°C–540°C (room temperature possible for sensitive materials) |
Advantages | Reduced substrate damage, wide material compatibility, uniform deposition |
Pressure Range | 0.1–10 Torr |
Key Applications | MEMS thin-film membranes, insulating layers, protective coatings |
Comparison with LPCVD | Lower tensile stress, better mechanical properties, slightly inferior electrical properties |
Optimize your PECVD process for silicon nitride—contact our experts today!