Tube annealing is a heat treatment process used to alter the physical and sometimes chemical properties of metal tubes, particularly stainless steel, to improve their ductility, reduce hardness, and relieve internal stresses. The temperature for tube annealing varies depending on the material and the desired outcome, but it typically falls within a range of 200°C to 1250°C. This process is crucial in industries such as semiconductors, new energy, and metals, where precise control over material properties is essential. The annealing process can be performed in specialized furnaces like rapid annealing furnaces or tube furnaces, which are designed to handle a wide range of temperatures and ensure uniform heating.
Key Points Explained:
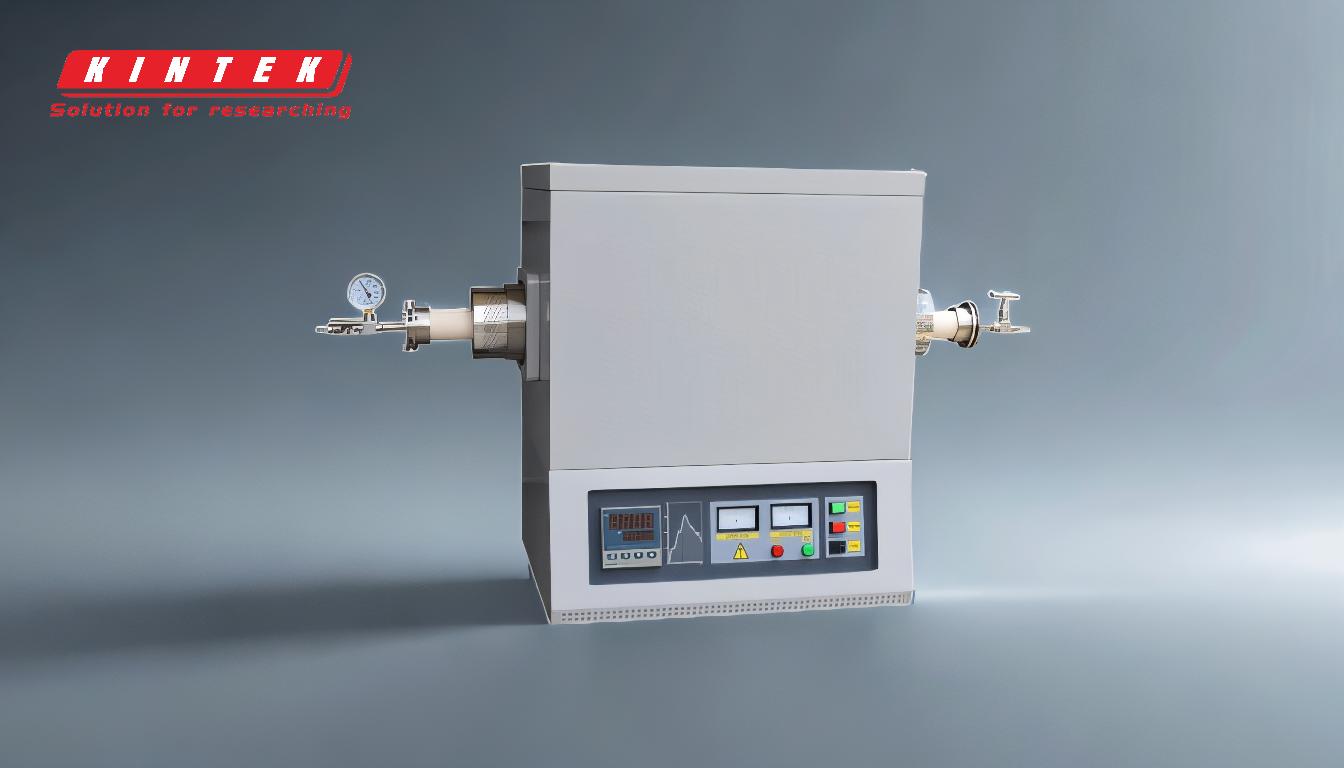
-
Temperature Range for Tube Annealing:
- Tube annealing typically occurs within a temperature range of 200°C to 1250°C. This range is suitable for various materials, including stainless steel, and is chosen based on the specific requirements of the material and the desired outcome of the annealing process.
- For stainless steel tubes, the annealing temperature is often set to around 1050°C to achieve optimal results, such as improved ductility and stress relief.
-
Types of Furnaces Used:
- Rapid Annealing Furnaces: These furnaces are designed to operate within the temperature range of 200~1250℃ and are commonly used in industries like semiconductors, new energy, and metals. They are capable of quickly heating and cooling the tubes, which is essential for achieving the desired material properties.
- Tube Furnaces: These furnaces have a wider temperature range and can be used for various heat treatment processes, including annealing, sintering, and drying. They are particularly useful for processes that require precise temperature control and uniform heating.
-
Importance of Temperature Control:
- Uniform Heating: Ensuring that the tube is heated uniformly is critical to prevent issues like cracking, which can occur due to thermal stress caused by temperature differences between the heating and non-heating zones. A temperature difference of at least 1000°C between these zones can lead to significant thermal stress and potential cracking.
- Cooling Rate: The rate at which the tube is cooled after annealing also plays a crucial role in determining the final properties of the material. Controlled cooling helps in achieving the desired microstructure and mechanical properties.
-
Material-Specific Considerations:
- Stainless Steel Tubes: For stainless steel tubes, the annealing process not only improves ductility and reduces hardness but also enhances the surface finish. The use of highly polished rolls during cold rolling, as mentioned in the reference, helps achieve a bright finish on both the inside and outside surfaces of the tube.
- Other Materials: Different materials may require different annealing temperatures and cooling rates. For example, copper tubes might be annealed at lower temperatures compared to stainless steel.
-
Applications of Tube Annealing:
- Semiconductor Industry: In the semiconductor industry, tube annealing is used to modify the electrical properties of materials, making them suitable for use in electronic components.
- New Energy Sector: In the new energy sector, annealing is used to improve the performance of materials used in batteries and fuel cells.
- Metal Industry: In the metal industry, annealing is a common process used to prepare tubes for further processing, such as bending or welding, by making them more ductile and easier to work with.
In summary, tube annealing is a critical process that involves heating metal tubes to specific temperatures (typically between 200°C and 1250°C) to improve their properties. The choice of temperature, type of furnace, and cooling rate are all important factors that influence the outcome of the annealing process. Proper control of these parameters ensures that the tubes achieve the desired mechanical and surface properties, making them suitable for various industrial applications.
Summary Table:
Aspect | Details |
---|---|
Temperature Range | 200°C to 1250°C, with 1050°C optimal for stainless steel |
Furnace Types | Rapid annealing furnaces (200~1250℃) and tube furnaces |
Key Considerations | Uniform heating, controlled cooling, and material-specific requirements |
Applications | Semiconductors, new energy, and metal industries |
Ready to optimize your tube annealing process? Contact our experts today for tailored solutions!