PVD (Physical Vapor Deposition) TiN (Titanium Nitride) coatings are applied at relatively low temperatures compared to other coating methods like CVD (Chemical Vapor Deposition). The ideal temperature range for PVD TiN coating typically falls between 200°C and 400°C (392°F to 752°F), depending on the substrate material and the specific application requirements. This temperature range is chosen to minimize thermal distortion, maintain substrate integrity, and ensure optimal coating adhesion and hardness. For heat-sensitive materials like aluminum, the lower end of this range is preferred to avoid melting or structural changes. The choice of temperature is critical to achieving the desired coating properties while preserving the substrate's mechanical and thermal characteristics.
Key Points Explained:
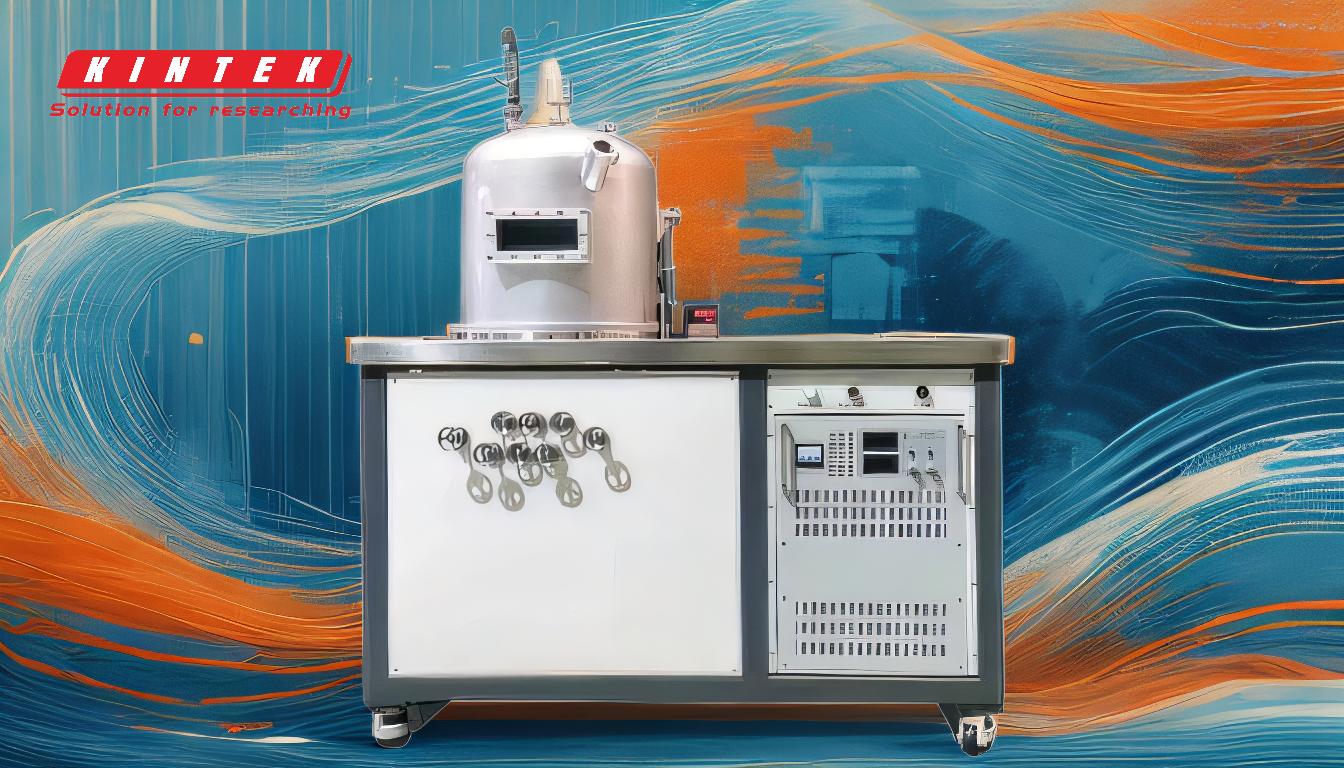
-
PVD TiN Coating Temperature Range:
- The typical temperature range for PVD TiN coating is 200°C to 400°C (392°F to 752°F).
- This range is significantly lower than CVD processes, which often operate at 600°C to 1100°C (1112°F to 2012°F).
- The lower temperatures in PVD are essential to avoid thermal distortion, especially for heat-sensitive materials like aluminum.
-
Substrate Material Considerations:
- Aluminum: PVD TiN is applied at temperatures below 800°F to prevent melting or structural changes.
- Steel, Zinc, Brass, and Plastic: The process temperature can be adjusted between 50°F to 400°F depending on the material's thermal properties and sensitivity.
- The substrate's thermal stability and melting point are critical factors in determining the optimal coating temperature.
-
Impact of Temperature on Coating Quality:
- Adhesion: Proper temperature ensures strong adhesion of the TiN coating to the substrate.
- Hardness: Temperature control is crucial to achieving the desired hardness and wear resistance of the coating.
- Distortion: Excessive temperatures can cause thermal distortion or changes in the substrate's microstructure, particularly in heat-sensitive materials.
-
Comparison with CVD:
- PVD operates at much lower temperatures (200-400°C) compared to CVD (800-1000°C).
- The lower temperatures in PVD make it suitable for coating a wider range of materials, including those with lower melting points or higher thermal sensitivity.
-
Practical Considerations for Equipment Purchasers:
- When selecting PVD equipment, ensure it offers precise temperature control within the 200°C to 400°C range.
- Consider the substrate materials you will be coating and choose equipment that can accommodate their thermal properties.
- Evaluate the need for additional pre-treatment (e.g., tempering at 900-950°F for heat-sensitive parts) to enhance coating performance.
-
Optimization for Specific Applications:
- For high-precision tools or heat-sensitive components, aim for the lower end of the temperature range (200-300°C).
- For durable industrial parts, temperatures closer to 400°C may be appropriate to maximize coating hardness and wear resistance.
By carefully controlling the temperature during PVD TiN coating, manufacturers can achieve high-quality, durable coatings while preserving the integrity of the substrate material. This balance is critical for applications requiring both performance and precision.
Summary Table:
Aspect | Details |
---|---|
Temperature Range | 200°C to 400°C (392°F to 752°F) |
Substrate Materials | Aluminum, Steel, Zinc, Brass, Plastic |
Key Benefits | Minimizes thermal distortion, ensures strong adhesion, and enhances hardness |
Comparison with CVD | PVD operates at lower temperatures (200-400°C vs. CVD's 600-1100°C) |
Applications | High-precision tools, heat-sensitive components, durable industrial parts |
Optimize your PVD TiN coating process—contact our experts today for tailored solutions!