Sintering is a critical process in manufacturing that involves heating materials to bond particles without melting them. The atmosphere used during sintering plays a vital role in determining the final properties of the sintered product. Different atmospheres, such as inert/protective, hydrogen, oxidizing, reducing, neutral, alkaline, and acidic, are selected based on the material being sintered and the desired characteristics. For example, a reducing atmosphere prevents oxidation and allows the reduction of surface oxides, while an inert atmosphere protects reactive materials from chemical reactions. The choice of atmosphere is crucial for achieving optimal density, strength, and other mechanical properties in the final product.
Key Points Explained:
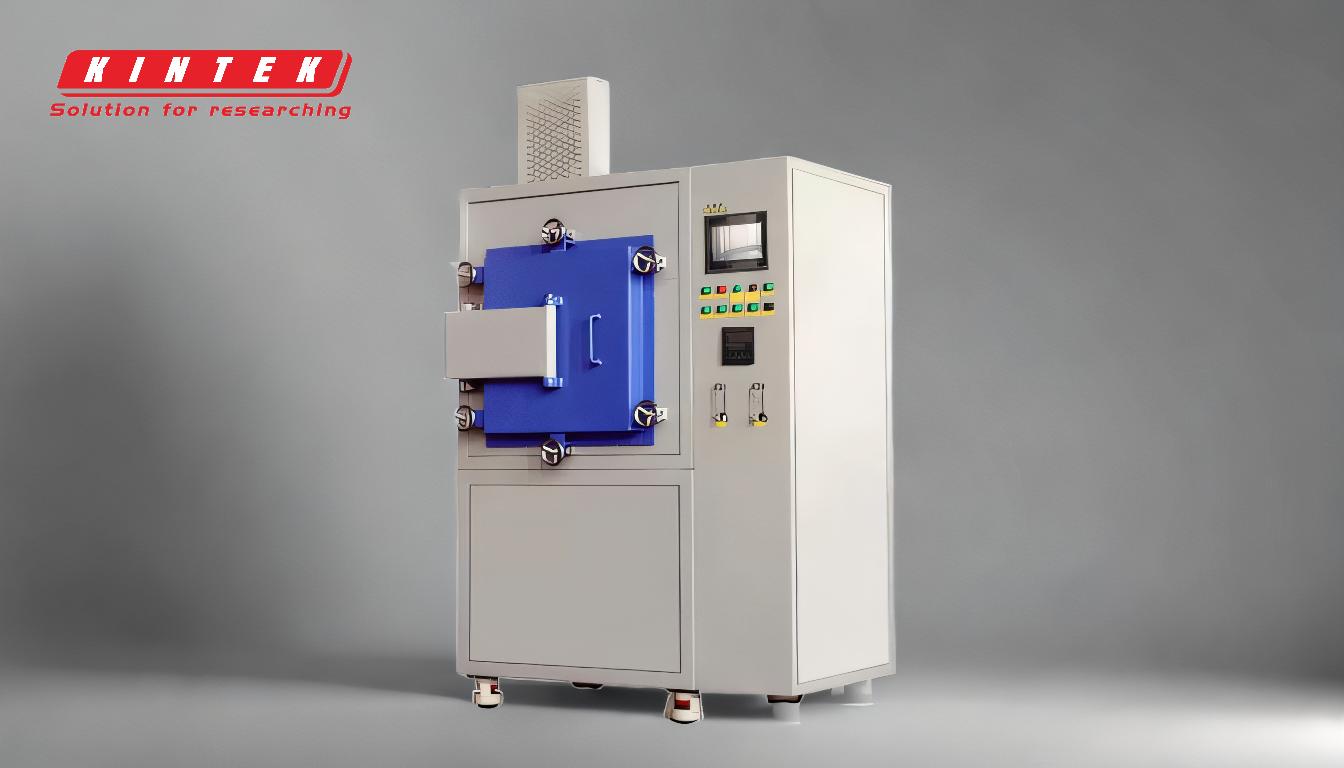
-
Types of Sintering Atmospheres:
-
Inert/Protective Atmosphere:
- Used to prevent chemical reactions, such as oxidation, during sintering.
- Common gases include argon and nitrogen.
- Ideal for sintering reactive metals like titanium or aluminum.
-
Hydrogen Atmosphere:
- Acts as a reducing agent, removing oxides from the material surface.
- Commonly used for sintering metals like tungsten or molybdenum.
-
Oxidizing Atmosphere:
- Contains oxygen, which can promote oxidation of the material.
- Rarely used in metal sintering but may be applicable for certain ceramics.
-
Reducing Atmosphere:
- Contains gases like hydrogen or carbon monoxide to reduce oxides.
- Prevents oxidation and improves material density.
-
Neutral Atmosphere:
- Neither oxidizing nor reducing, used when minimal chemical interaction is desired.
- Often used for sintering non-reactive materials.
-
Alkaline Atmosphere:
- Contains alkaline compounds to neutralize acidic impurities.
- Rarely used but can be beneficial for specific applications.
-
Acidic Atmosphere:
- Contains acidic gases to remove alkaline impurities.
- Used in specialized sintering processes.
-
Inert/Protective Atmosphere:
-
Factors Influencing Atmosphere Selection:
-
Material Properties:
- Reactive metals like titanium require inert atmospheres to prevent oxidation.
- Metals prone to oxidation, such as iron, benefit from reducing atmospheres.
-
Desired Product Characteristics:
- A reducing atmosphere improves density and mechanical strength.
- An inert atmosphere preserves the material's chemical composition.
-
Temperature and Pressure:
- Sintering typically occurs at 750–1300°C, with the atmosphere adjusted to match the temperature range.
- Vacuum or partial vacuum conditions may be used for specific materials.
-
Material Properties:
-
Applications of Different Atmospheres:
-
Inert Atmospheres:
- Used in aerospace and medical industries for sintering titanium and other reactive metals.
-
Hydrogen Atmospheres:
- Common in the production of tungsten filaments and molybdenum components.
-
Reducing Atmospheres:
- Widely used in powder metallurgy for sintering iron-based alloys.
-
Vacuum Sintering:
- Preferred for high-purity materials and advanced ceramics.
-
Inert Atmospheres:
-
Impact of Atmosphere on Sintered Products:
-
Density and Porosity:
- Reducing atmospheres enhance densification by removing oxides and promoting particle bonding.
-
Mechanical Properties:
- Proper atmosphere selection improves strength, hardness, and wear resistance.
-
Surface Quality:
- Inert and reducing atmospheres prevent surface oxidation, resulting in a cleaner finish.
-
Density and Porosity:
-
Operational Considerations:
-
Furnace Design:
- Continuous furnaces are commonly used for sintering under controlled atmospheres.
- Furnaces must be capable of maintaining precise temperature and atmosphere control.
-
Cost and Safety:
- Hydrogen atmospheres require careful handling due to flammability.
- Inert gases like argon and nitrogen are safer but may be more expensive.
-
Furnace Design:
By carefully selecting the appropriate sintering atmosphere, manufacturers can achieve the desired material properties and ensure the quality and performance of the final product.
Summary Table:
Atmosphere Type | Key Features | Common Applications |
---|---|---|
Inert/Protective | Prevents oxidation; uses argon or nitrogen. | Sintering reactive metals like titanium. |
Hydrogen | Reduces surface oxides; acts as a reducing agent. | Sintering tungsten and molybdenum. |
Oxidizing | Promotes oxidation; rarely used in metals. | Certain ceramics. |
Reducing | Prevents oxidation; improves density and strength. | Powder metallurgy for iron-based alloys. |
Neutral | Minimal chemical interaction; used for non-reactive materials. | General sintering. |
Alkaline | Neutralizes acidic impurities; rarely used. | Specialized applications. |
Acidic | Removes alkaline impurities; used in specialized processes. | Specialized sintering. |
Need help selecting the right sintering atmosphere for your materials? Contact our experts today!